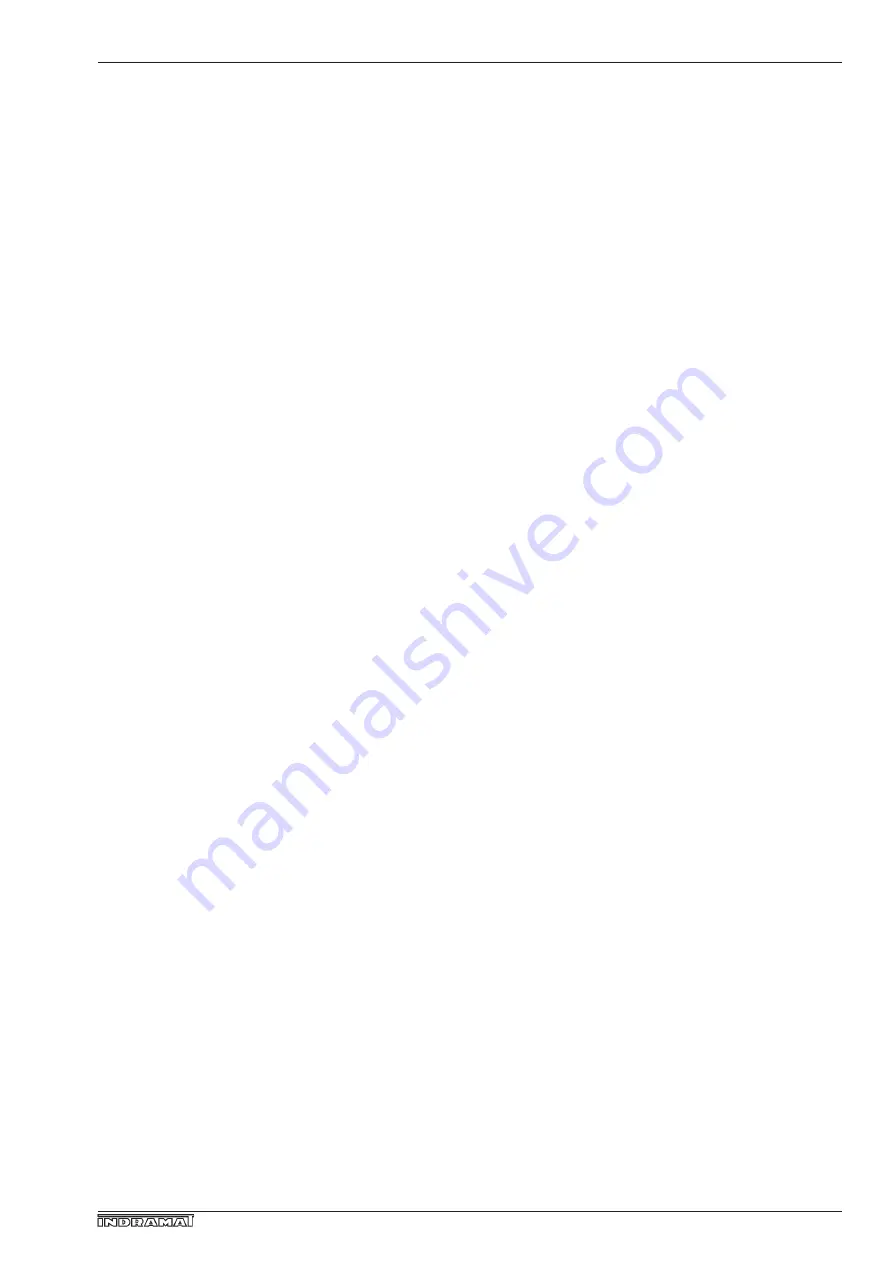
12
• DOK-DIAX01-TDA********-PRJ1-EN-E1,44 • 07.97
Programming module
The various parameters relating to both the machine and the application
are entered on site during commissioning using the keypad on the control
panel. Together with the parameter values for motor matching, these
parameter values are stored in the controller’s plug-in programming
module.
In the event of a fault requiring unit replacement, only the controller itself
is replaced, the programming module being transferred to the new
controller. The characteristics of the drive are stored in the programming
module and are therefore immediately available on re-start.
1. Presentation of the modular main spindle controller TDA 1
Interface options
The controllers can be supplied with a variety of speed command
interfaces:
• Analogue speed command
±
10 V for connection to commercially available NC controllers,
• Digital speed command
16 bit parallel for connection to PLCs, useful in the case of long cables
and small command values,
• SERCOS interface
for real time communication with the NC controller relating to command
and actual value of speed, position and torque, including parameter
handling.
An additional encoder input is available for connection of a spindle
feedback signal to the controller’s internal position loop. For spindle
synchronisation, both the additional encoder input and a synchronous
input (connection for master spindle feedback signal) are supplied.
The controller TDA 1 also comprises an additional interface, available as:
• Incremental encoder output
for position control by the NC controller in C-axis mode or for thread
cutting,
• Serial interface
for saving and loading parameter values using a PC,
• Input for digital position command
16 bit parallel, for 3600 positions selectable by PLC.
Speed command value
Additional encoder input,
synchronisation input
Additional interface