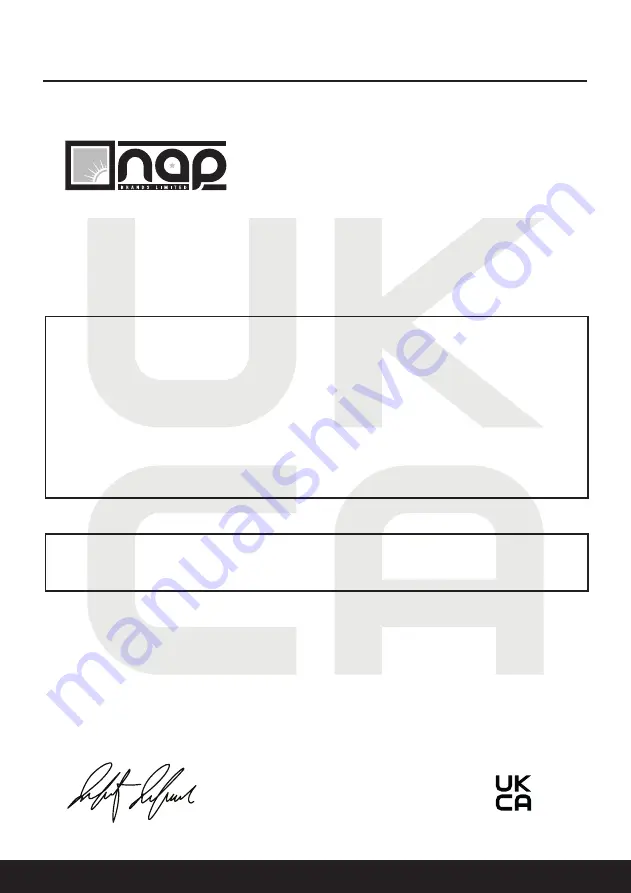
DECLARATION OF CONFORMITY
After sales support: Tel:
0344 264 2485
Website:
www.impaxpowertools.com
1.
Product model:
IM-MULT160-K
2.
Name and address of the manufacturer or his authorised representative:
NAP BRANDS LTD. Office 20, Fleming Court Business Centre,
Leigh Road, Eastleigh, Hampshire SO50 9YN
Tel: +44 (0)23 8064 9650. Email: [email protected]
3.
This declaration of conformity is issued under the sole responsibility of the manufacturer.
4.
Object of the declaration:
Equipment: 160A MIG/TIG/MMA Welder
Brand name: IMPAX
Model/type: IM-MULT160-K
5.
The object of the declaration described above is in conformity with the relevant statutory requirements:
6.
References to the relevant designated standards used or references to the other technical
specifications in relation to which conformity is declared:
7.
The person authorized to compile the technical file:
Name:
Robert Redfern
Address:
Nap Brands Ltd. Office 20, Fleming Court Business Centre, Leigh Road, Eastleigh,
Hampshire SO50 9YN
Signed for and on behalf of:
Authorised Representative
Robert Redfern, Technical Manager
03/03/2022
Supply of Machinery (Safety) Regulations 2008
Electrical Equipment (Safety) Regulations 2016
Electromagnetic Compatibility Regulations 2016
The Restriction of the Use of Certain Hazardous Substances in Electrical and Electronic Equipment
Regulations 2012
BS EN IEC 60974-1
BS EN IEC 60974-10
EN IEC 60974-1
EN IEC 60974-10
22
Summary of Contents for IM-MULT160-K
Page 11: ...SAFETY INFORMATION 10...
Page 56: ...WIRING DIAGRAM 55...
Page 57: ...NOTES 56...
Page 58: ...NOTES 57...
Page 59: ...NOTES 58...