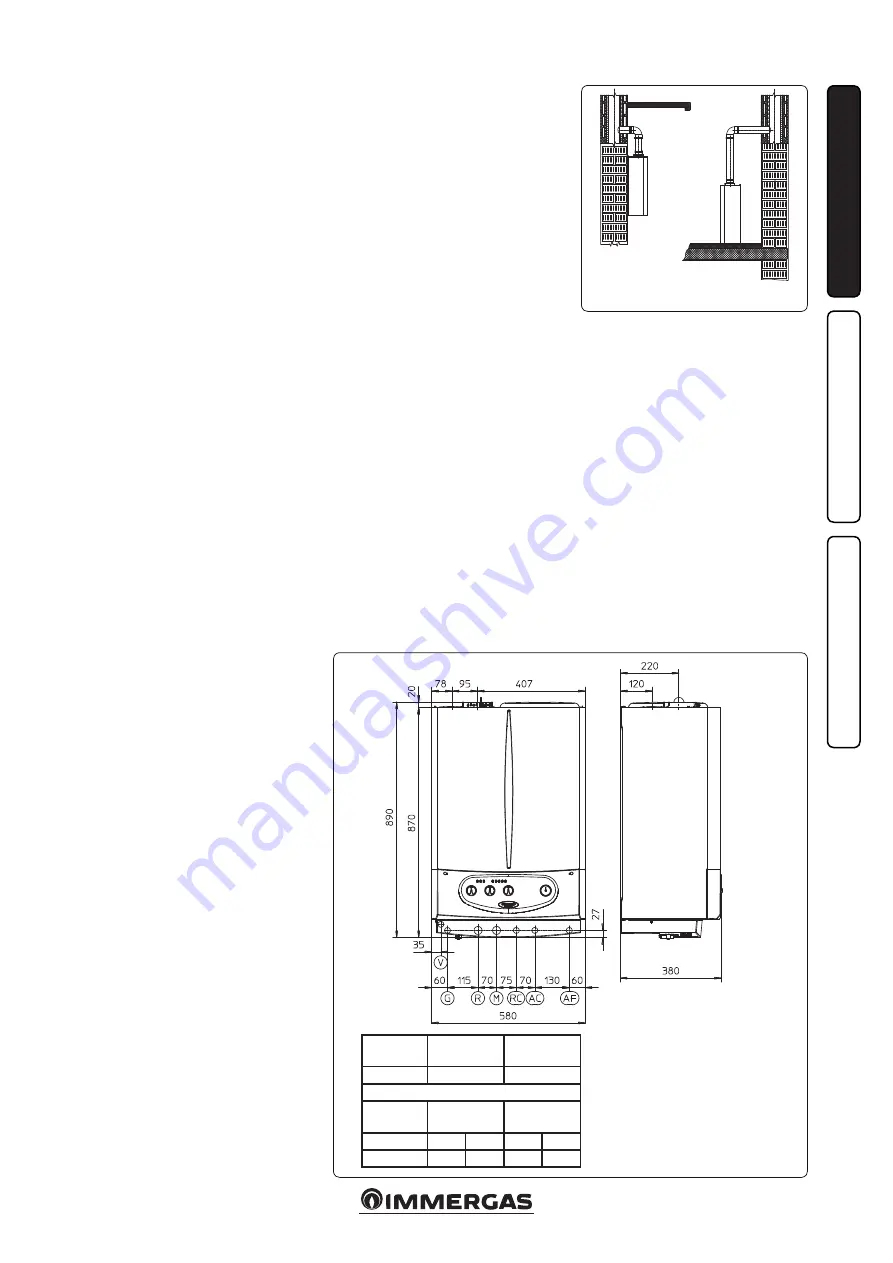
3
1-1
1-2
INS
TALL
AT
O
R
US
ER
MAINTEN
AN
CE
YES
NO
Height
(mm)
Width
(mm)
Depth
(mm)
890
580
380
ATTACHMENTS
GAS
PLANT
DOMESTIC
HOT WATER
G
R
M
AC
AF
1/2”
3/4”
3/4”
1/2”
1/2”
1.2 MAIN DIMENSIONS.
Key:
G - Gas supply
R - System return
M - System delivery
RC - Domestic hot water re-circ.
AC - Domestic hot water outlet
AF - Domestic hot water inlet
V - Electric attachment
1
INSTALLATION
OF THE BOILER
1.1 INSTALLATION
RECOMMENDATION.
The Zeus kW boiler has been designed for wall
mounted installation only; they must be used
to heat environments, to produce domestic hot
water and similar purposes.
The installation site and relative Immergas ac-
cessories must have suitable characteristics (both
technical and structural), in order to allow (al-
ways in safe, efficiency and easiness conditions):
- installation (according to the legislation and
technical standards in force);
- maintenance operations (including those
scheduled, periodical, ordinary and special);
- removal (to the outdoors in a place suitable
for loading and transporting appliances and
components) as well as any replacement with
equivalent appliances and/or components.
The wall surface must be smooth, without any
protrusions or recesses enabling access to the
rear part. They are NOT designed to be installed
on plinths or floors (Fig. 1-1).
By varying the type of installation the
classification of the boiler also varies, precisely:
- B
22
type boiler
if installed using the relevant
terminal for air intake directly from the room
in which the boiler has been installed.
- C type boiler
if installed using concentric pipes
or other types of pipes envisioned for the sealed
chamber boiler for intake of air and expulsion
of fumes.
Only professionally qualified heating/plumbing
technicians are authorised to install Immergas
gas appliances.
Installation must be carried out according to the
standards, current legislation and in compliance
with local technical regulations and the required
technical procedures.
Installation of the Zeus kW boiler when powered
by LPG must comply with the rules regarding
gases with a greater density than air (remember,
as an example, that it is prohibited to install plants
powered with the above-mentioned gas in rooms
where the floor is at a lower quota that the average
external country one).
Before installing the appliance, ensure that it
is delivered in perfect condition; if in doubt,
contact the supplier immediately. Packing
materials (staples, nails, plastic bags, polystyrene
foam, etc.) constitute a hazard and must be kept
out of the reach of children. If the appliance
is installed inside or between cabinets, ensure
sufficient space for normal servicing; therefore
it is advisable to leave a clearance of at least 3
cm between the boiler casing and the vertical
sides of the cabinet.
Leave adequate space above the boiler for
possible water and fume removal connections.
At least 60 cm must be left below the boiler
in order to guarantee replacement of the
magnesium anode. Keep all flammable objects
away from the appliance (paper, rags, plastic,
polystyrene, etc.).
Do not place household appliances underneath
the boiler as they could be damaged if the safety
valve intervenes (if not conveyed away by a
discharge funnel), or if there are leaks from the
connections; on the contrary, the manufacturer
cannot be held responsible for any damage
caused to the household appliances.
In the event of malfunctions, faults or incorrect
operation, turn the appliance
off immediately and contact a qualified technician
(e.g. the Immergas Technical Assistance centre,
which has specifically trained personnel and
original spare parts). Do not attempt to modify
or repair the appliance alone. Failure to comply
with the above implies personal responsibility
and invalidates the warranty.
• Installation regulations: this boiler can be
installed outside in a partially protected area.
A partially protected location is one in which
the appliance is not exposed to the direct action
of the weather (rain, snow, hail, etc..).
Important
: Wall mounting of the boiler must
guarantee stable and efficient support for the
generator.
The plugs supplied are to be used only in
conjunction with the mounting brackets or fixing
template to fix the appliance to the wall;
they only
ensure adequate support if inserted correctly
(according to technical standards) in walls made
of solid or semi-hollow brick or block. In the
case of walls made from hollow brick or block,
partitions with limited static properties, or in any
case walls other than those indicated, a static test
must be carried out to ensure adequate support.
N.B.: the hex head screws supplied in the blister
pack are to be used exclusively to fix the relative
mounting bracket to the wall.
These boilers are used to heat water to below
boiling temperature in atmospheric pressure.
They must be connected to a heating system and
hot water circuit suited to their performance
and capacity.
Anti-Legionella thermal treatment of the Im-
mergas storage tank (which can be activated
through the specific function present on the set
thermoregulation systems): during this phase,
the water temperature inside the storage tank ex-
ceeds 60 °C resulting in burns hazards. Keep this
DHW treatment under control (and inform the
users), to prevent unexpected damage to persons,
animals and objects. If required, a thermostatic
valve must be installed at the DHW outlet to
prevent burns.
Summary of Contents for ZEUS 24 Superior
Page 1: ...ZEUS 24 28 kW IE Instruction booklet and warning 1 038761ENG...
Page 26: ......
Page 27: ......