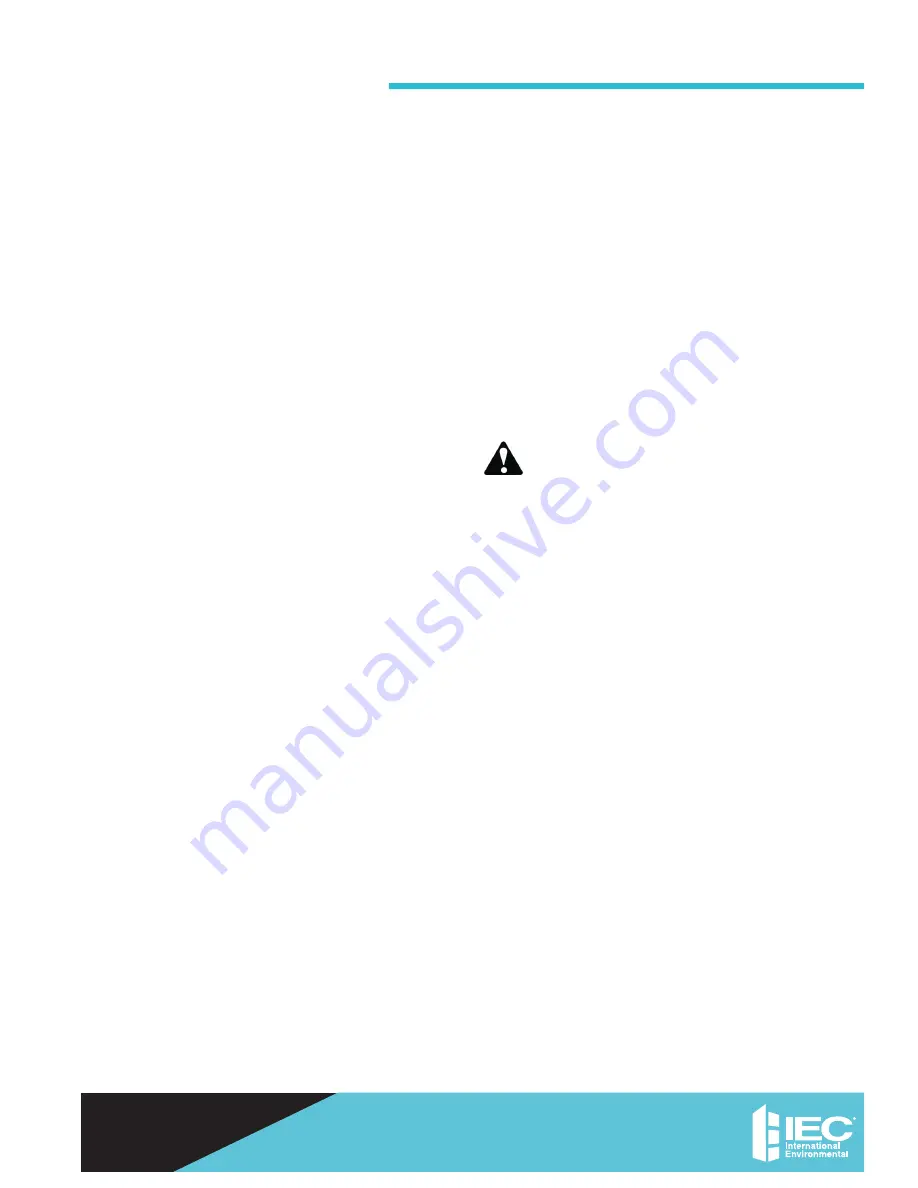
Cabinet Heater G*Y/D*Y Series
INSTALLATION, OPERATION, & MAINTENANCE MANUAL
17
SECTION TWO — Start-Up
General Start Up
Before beginning any start-up operation, the start-up
personnel should familiarize themselves with the unit,
options and accessories, and control sequence to
understand the proper system operation. All personnel
should have a good working knowledge of general
start-up procedures and have the appropriate start-up
and balancing guides available for consultation.
The building must be completely finished including doors,
windows, and insulation. All internal walls and doors
should be in place and in the normal position. In some
cases the interior decorations and furniture may influence
overall system performance. The entire building should
be as complete as possible before beginning any system
balancing.
The initial step in any start-up operation should be a final
visual inspection. All equipment, plenums, duct-work, and
piping should be inspected to verify that all systems are
complete and properly installed and mounted, and that no
debris or foreign articles such as paper or drink cans are
left in the units or other areas.
Each unit should be checked for:
1. free blower wheel operation
2. loose wires
3. loose or missing access panels or doors
4. clean filter of the proper size and type
Except as required during start-up and balancing operations,
no fan coil units should be operated without all the proper
ductwork attached, supply and return grilles in place, and all
access doors and panels in place and secure. Failure to do
so could result in damage to the equipment or building and
furnishings, and/or void all manufacturer’s warranties.
Hydronic Heating System
Prior to the water system start-up and balancing, the hot
water systems should be flushed to clean out dirt and
debris which may have collected in the piping during
con struction. During this procedure, all unit service valves
must be in the closed position. This prevents foreign
matter from entering the unit and clogging the valves
and metering devices. Strainers should be installed in the
piping mains to prevent this material from entering the
units during normal operation.
During system filling, air venting from the unit is
accomplished by the use of the standard, manual air vent
fitting, or the optional, automatic air vent fitting installed.
To vent the air from the coil, depress the valve until the air
has vented the coil. When water begins to escape through
the valve, release the valve. Automatic air vents may be
unscrewed one turn counterclockwise to speed initial
venting, but should be screwed in for automatic venting
after start-up operations.
CAUTION! The air vent provided on the unit is
not intended to replace the main system air vents
and may not release air trapped in other parts of the
system. Inspect the entire system for potential air traps
and vent those areas as required, independently. In
addition, some systems may require repeated venting over
a period of time to properly eliminate air from the system.
Air System Balancing
All ductwork must be complete and connected. All grilles,
filters, and access doors and panels must be properly
installed to establish actual system operating conditions
BEFORE
beginning air balancing operations.
Each individual unit and the attached ductwork is a
unique system with its own operating characteristics. For
this reason, air balancing is normally done by balance
specialists who are familiar with all procedures required
to properly establish air distribution and fan-system
operating conditions. These procedures should not be
attempted by unqualified personnel.
Exposed units without ductwork do not require air
balancing other than selecting the desired fan speed.
After proper system operation is established, the actual
unit air delivery and the actual fan motor amperage draw
for each unit should be recorded in a convenient place for
future reference.