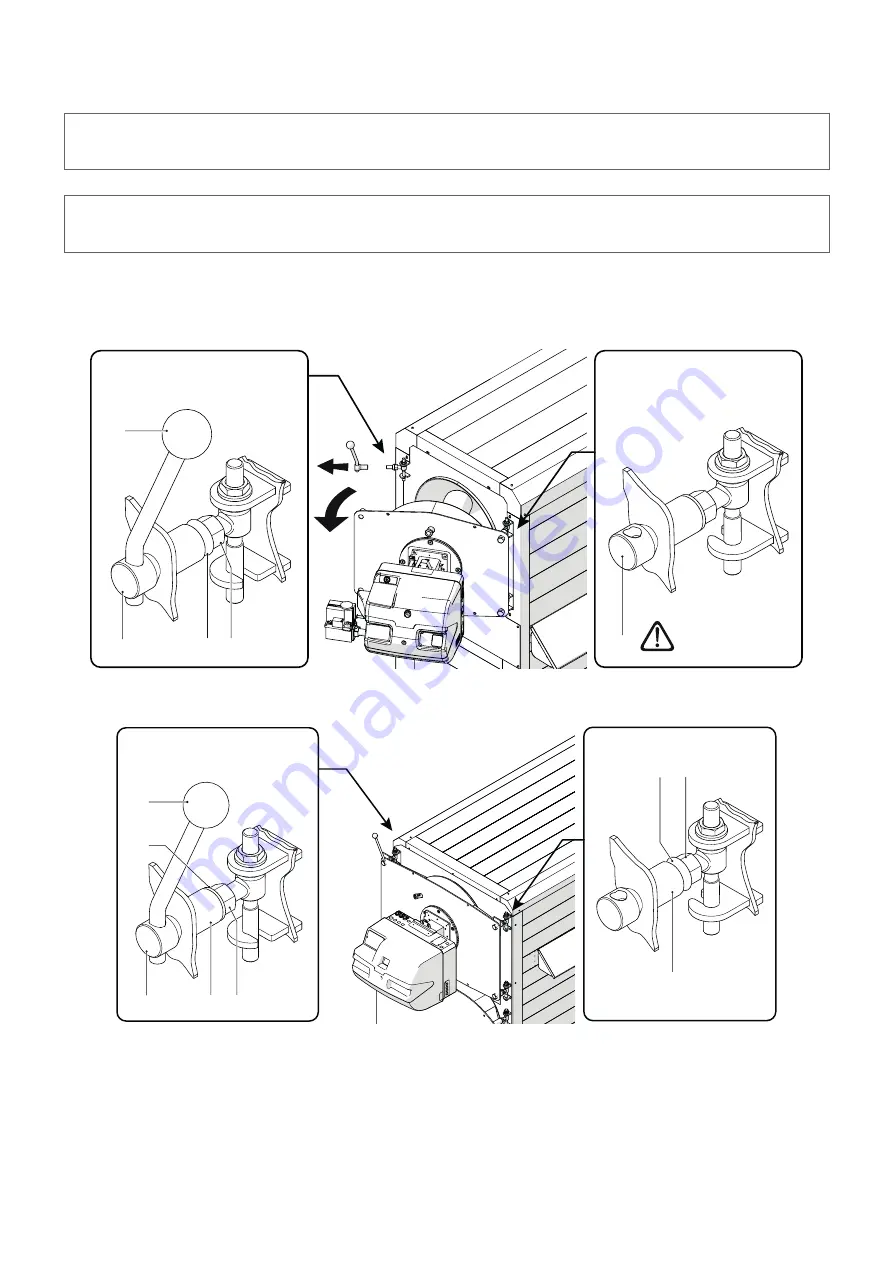
Installation
16
DOOR OPENING
The door is adjusted in the factory with standard opening to the left (Sx) and hinges on the right (Dx).
m
IMPORTANT
The hinges of the opening side must have the nut (1) loosened and the conical washer (2) positioned towards the
base of the adjustment tie-rod.
a
DANGER
IT IS DANGEROUS TO UNSCREW
the ring nuts (3) of the door rotation hinges. Unscrewing them could cause the
detachment of the door, with possible severe damages to persons and property.
Before opening the door:
–
close the gas line shut-off valves and disconnect the pipes
–
use the lever (4) to unscrew and extract the ring nuts (5) of the two hinges on the opening side of the door and pull it
carefully.
4
3
5
1
2
Hinge of rotation
door side
Hinge of opening
door side
DOOR OPENING INVERSION (FROM THE RIGHT TO THE LEFT)
Dx
Sx
2
4
1
5
3
7
6
8
Left hinge:
–
screw the ring nuts (1) of the left side with the lever (2) in such a way that the distance of the door from the appliance front
plate is the same and the sealing gasket is uniformly pressed.
–
screw the nuts (3), of the left tie-rods, until the conical washers (4) are inserted into the door mechanical tubes (5). Properly
tighten the nuts (3).
Right hinge:
–
loosen the nuts (6) and disengage the conical washers (7) from the door mechanical tubes (8).
Cooke Industries - Phone: +64 9 579 2185 Email: [email protected] Web: www.cookeindustries.co.nz