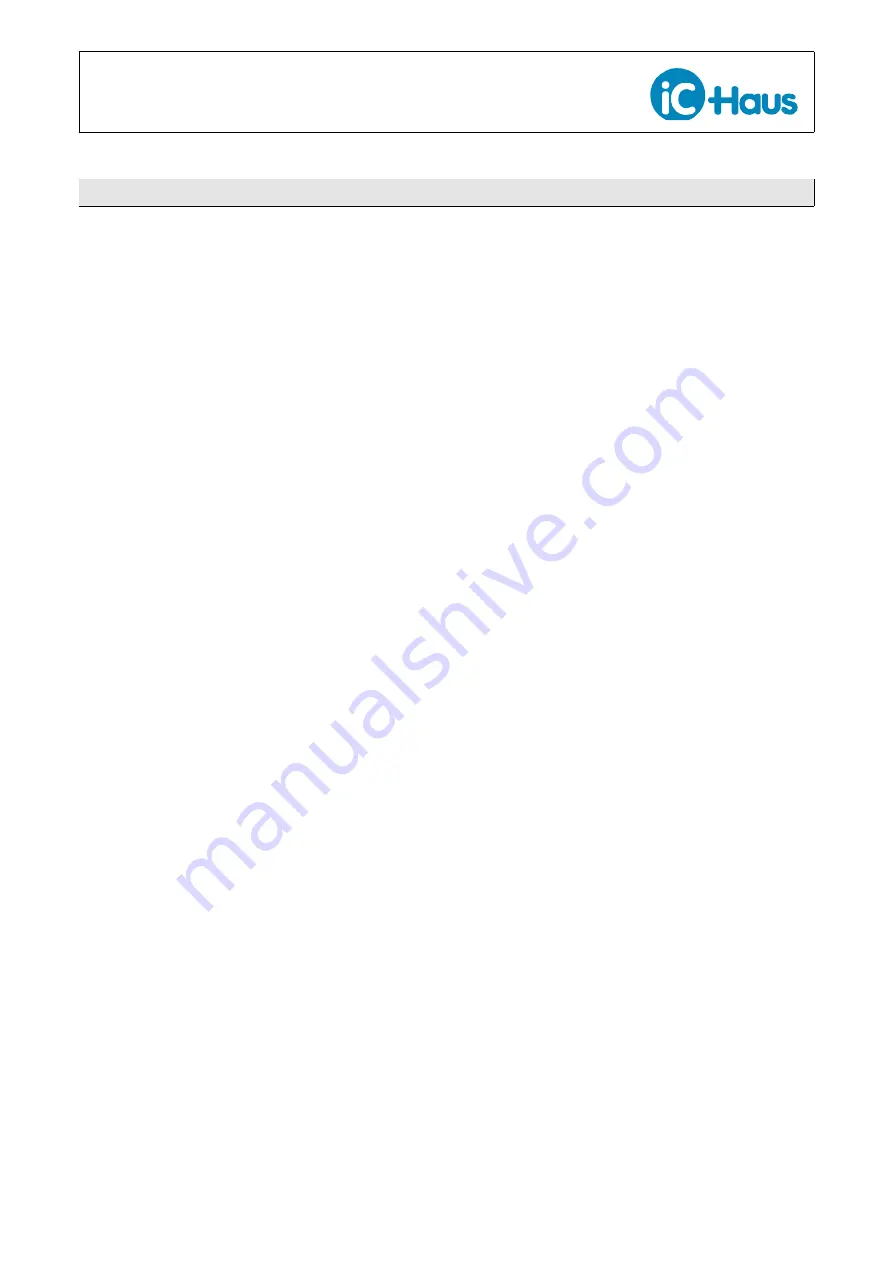
prel
imin
ary
prel
imin
ary
iC-TW29
26-BIT ENCODER PROCESSOR
WITH INTERPOLATION AND BiSS INTERFACE
Rev C1, Page 26/28
CONFIGURATION AND CALIBRATION
Introduction
The iC-TW29 uses a modular architecture. This means
that only the enabled modules and required features
need to be configured. For example, if ABZ outputs are
not enabled, the ABZ output module does not need to
be configured.
Configuration values for enabled modules and required
features must be written to the TW29’s internal EEP-
ROM using the BiSS or SPI ports or the Encoder Link in-
terface before the device can be used. For stand-alone
applications, the easiest way to accomplish this is to
use one of the iC-TW29 demo boards and the free
Graphical User Interface (GUI) software.
The iC-TW29 EVAL TW29_1D evaluation board im-
plements the iC-TW29 and a USB interface for direct
communication with the GUI software for ABZ and UVW
applications. The iC-TW29 EVAL TW29_3D evaluation
board implements the iC-TW29 and a USB interface for
direct communication with the GUI software for BiSS
and SSI applications. Using one of these boards, a
functional prototype encoder can be quickly assembled
and configured. See the
for more information.
The TW29_1D evaluation board includes a break-away
programmer that can be used for prototype develop-
ment to configure an external iC-TW29 via the SPI or
Encoder Link interfaces using the free GUI software. In
series production, this programmer can be employed to
download pre-engineered configurations to iC-TW29s
embedded in products.
In hosted applications (where the SPI port is used to
communicate with the host processor), the iC-TW29
must be configured via the host, or through the BiSS or
Encoder Link interfaces.
The remainder of this section assumes use of a
TW29_1D (ABZ) or TW29_3D (BiSS) demo board in
a rotary application with or without a zero sensor. The
GUI software is used for configuration and calibration
via SPI communication.
Default Configuration
To ensure known starting conditions, load the default
configuration file using the File menu in the GUI. This
sets all parameters to their default or recommended
values and disables the monitors to avoid nuisance
faults during configuration and calibration. Once the
iC-TW29 is configured and calibrated, the monitors and
other advanced features can be enabled as needed.
Click on the EEPROM block in the block diagram on the
main GUI window to open the EEPROM tab and save
the default configuration to EEPROM. Finally, restart
the iC-TW29 by clicking the play button (
▷
) on the main
GUI window.
Input Configuration and Calibration
Click on the AFE-IPO (Analog Front End and Interpo-
lator) tab. Select the signal range that corresponds to
the attached sin/cos and zero sensors. In general, use
low range for passive sensors (like AMR and un-ampli-
fied Hall) and high range for powered (amplified Hall or
photo diode) sensors. See Figures 2 and 3 for more
information on signal ranges. The other parameters
can be left at their default values.
In the Calibration tab, check "Auto calibrate sine/cosine
offsets, gains, and phase" and "Automatically store
calibrated values to EEPROM." If a zero sensor is con-
nected, also check "Auto calibrate zero analog offset
and gain" and "Auto calibrate IA phase shift."
With the sin/cos and zero (if used) sensors generating
signals, click the Auto-calibration "Start" button in the
GUI or the xCALIB button on the demo board to begin
auto calibration. When the values in the signal path
diagram on the Calibration tab have settled to non-zero
values, click the Auto-calibration "Stop" button. This
stops auto calibration and stores the calibrated values
to EEPROM.
With the sensors still generating signals, click the Adap-
tion tab. The Sine and Cosine Amplitude bar graphs
should show signal amplitudes of 2400
±
100. If not,
change the input range settings (AFE-IPO tab) as re-
quired and re-run auto calibration.
Once the signal path has been successfully calibrated,
enable auto adaption in the adaption tab for offset, bal-
ance, and phase as required. Save these configuration
values to EEPROM using the EEPROM tab. With auto
adaption enabled and the sensors generating signals,
the correction values on the signal path diagram in the
calibration tab should be changing by small amounts.
In the Gearbox tab, set the Revolution Counter Length
as required. The default is 16 bits. If revolution count-
ing is not needed, the counter can be left at the default
value or set to zero.
Set the Input Cycles per Revolution to match the num-
ber of sin/cos cycles generated by the sensor per output
revolution. Save these values to EEPROM. The other
parameters in this tab can be left at their default values.