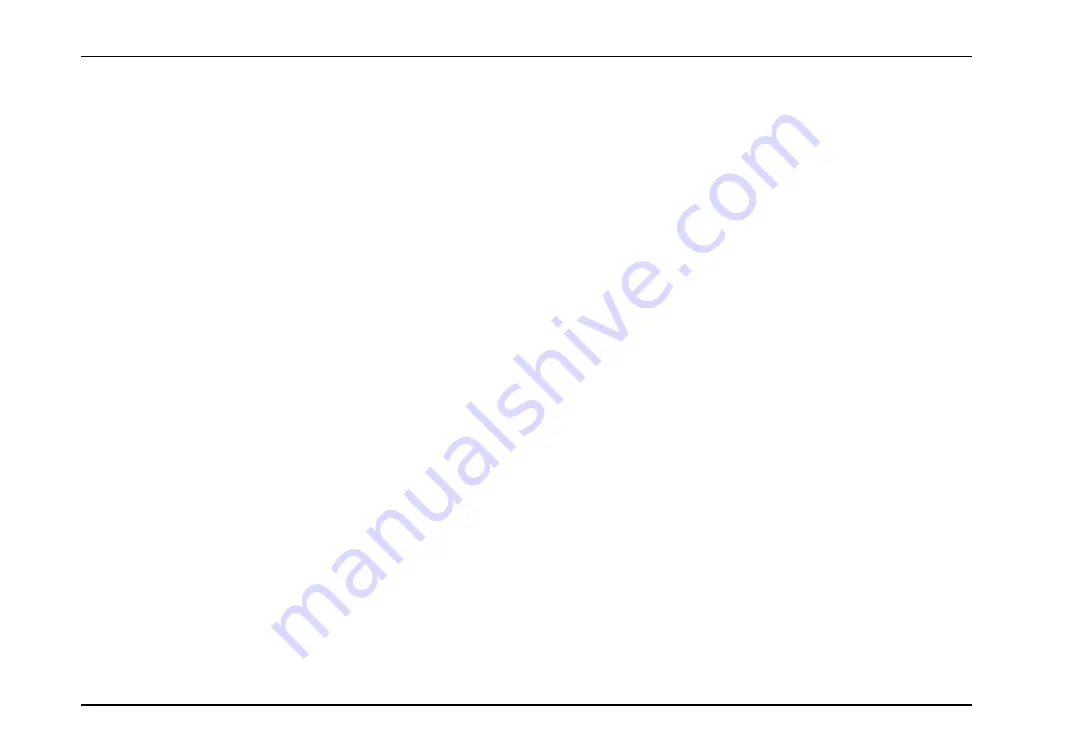
Operation
•
Attempt to steer clear of traffic, pedestrians or other
obstacles while you are in an emergency braking situation.
The antilock brake system will allow you to steer the vehicle
during braking while it comes to a full stop. ABS is not an
excuse to take unnecessary risks. Always drive carefully
and stay a safe distance away from the vehicle in front of
you.
•
Do not pump the brake pedal during a skid unless the ABS
system is not functioning.
ABS Self-Check
NOTE: If an antilock fault develops, standard brake
system operation is maintained. The brake system is still
operational, but the antilock system does not operate to
prevent wheel lockup if you over apply the brakes for
existing conditions.
NOTE: If the ABS indicator stays illuminated or continues
to flash, have the system serviced immediately.
A yellow warning indicator on the instrument panel indicates
the status of the ABS. Each time the ignition is turned on the
indicator comes on and the system goes through an ABS
self-check sequence. If the system is working normally when
the ignition is turned ON, the ABS indicator comes on then
flashes twice, and finally the ABS indicator remains on for
several seconds before going out.
124
Summary of Contents for BE Series
Page 4: ......
Page 11: ...Table of Contents Section 14 Index Index 215 vii ...
Page 12: ...Table of Contents viii ...
Page 52: ...Instrumentation Declination Zone Map 40 ...
Page 67: ...Driver Controls 55 ...
Page 68: ...Driver Controls 56 ...
Page 71: ...Driver Controls 59 ...
Page 144: ...Operation 132 ...
Page 151: ...Roadside Emergencies Body Fuse Circuit Breaker Panel 139 ...