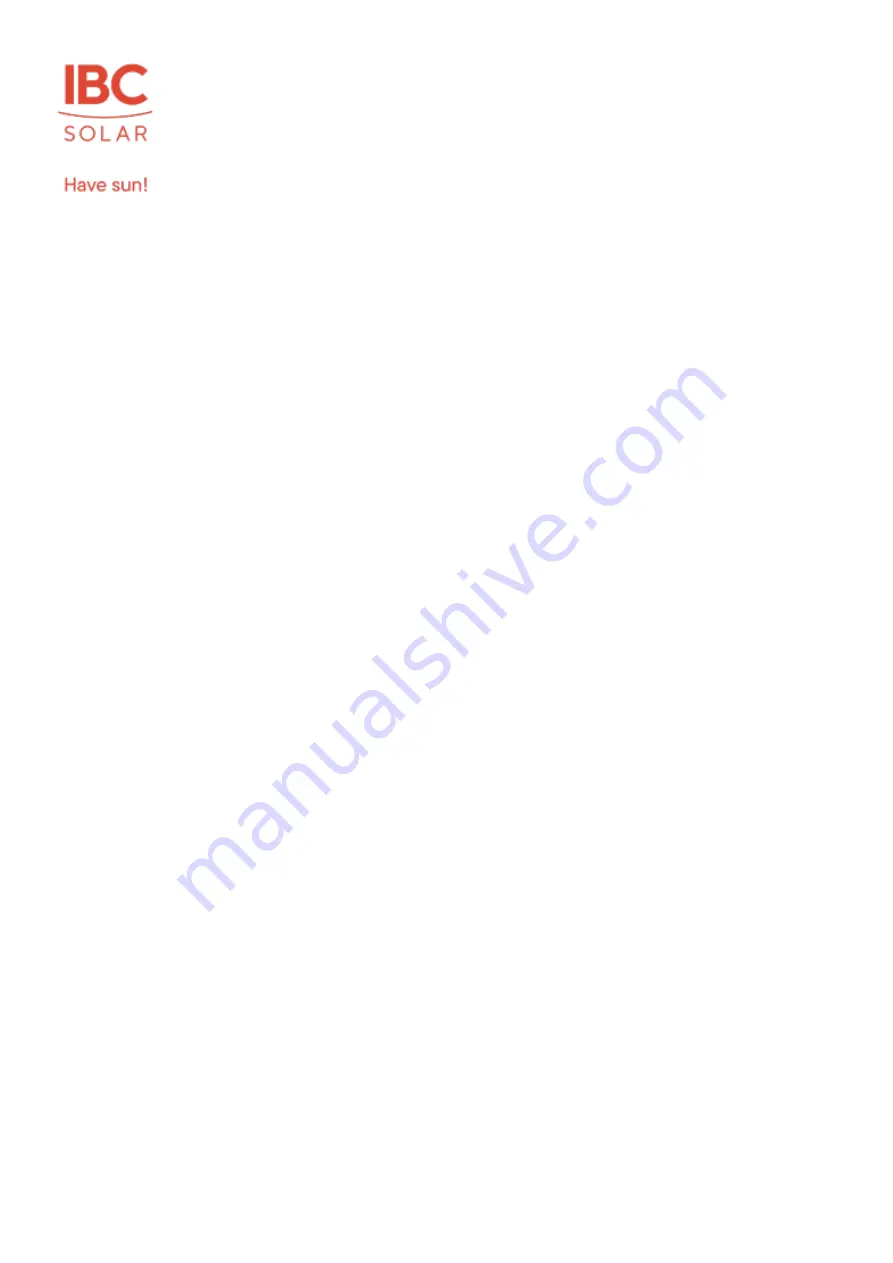
Version: 23.01
As of: 01/2023
Page
17
from
119
5. Fitting the various mounting systems
5.1 General dimensioning information
The PV system on your roof is subject to considerable forces caused by snow and, most of all, wind. Improper fastening of the PV
system, particularly the modules, may cause significant damage to objects as well as personal injury. For this purpose, it is crucial
you observe the following section.
The number of fixing points on the roof is always dependent on the particular design of the roof, building height, roof pitch, the
wind and snow load zone and a large number of other factors.
The compatibility of the material pairings between the roof and the PV system must be checked before the installation.
Edges and corner areas must be particularly taken into account as per EN 1991-1-4 (Euro code 1) as increased loads may apply
due to wind dynamics, depending on the building type. For more detailed information, please see the graphical indications of
fixing points in our PV Manager software. Calculate and verify any specific details according to the applicable standards. In this
process, we recommend you consult a civil engineer.
Before starting installation, the existing substructure of the building must be checked for sufficient stability. The wooden
substructure must have a service life of more than 20 years. In case of doubt, consult a roofer or joiner and a civil engineer.
As a rule, verify on-site static conditions and whether or not the outer roofing in conjunction with the substructure (steel
beams/purlins, rafters, roof battens,etc.) is able to bear the additional pressure and dynamic loads of the PV plant.
We shall not assume any system liability for the integrity of the roof as this mainly depends on the quality of mounting or
subsequent sealing procedures. The rules of the building trade as well as guidelines and instructions of the roofing manufacturer
are to be observed. Mounting system parts must not be treated with additional anti-corrosion protection in normal, atmospheric
conditions (corrosivity categories C1-C3 according to EN ISO 12944-2 and surrounding temperatures of -30°C to +50°C). Take
additional, suitable anti-corrosion protection measures in the event of other assembly locations (e.g. contact with grit, direct
vicinity to the coast, acidic or alkaline environments).
The maximum allowed roof inclination for the mounting system is 75°. It is limited by the permissible inclination of the modules.
Modifications that are not permitted and improper use of our components during assembly and construction shall render and
liability and guarantee claims void.
Summary of Contents for TopFix 200
Page 1: ...Instalation manual TopFix 200 IBC SOLAR AG Version 23 01 As of 01 2023...
Page 114: ...Version 23 01 As of 01 2023 Page 114 from 119...
Page 115: ...Version 23 01 As of 01 2023 Page 115 from 119...
Page 116: ...Version 23 01 As of 01 2023 Page 116 from 119...
Page 117: ...Version 23 01 As of 01 2023 Page 117 from 119...
Page 118: ...Version 23 01 As of 01 2023 Page 118 from 119...
Page 119: ......