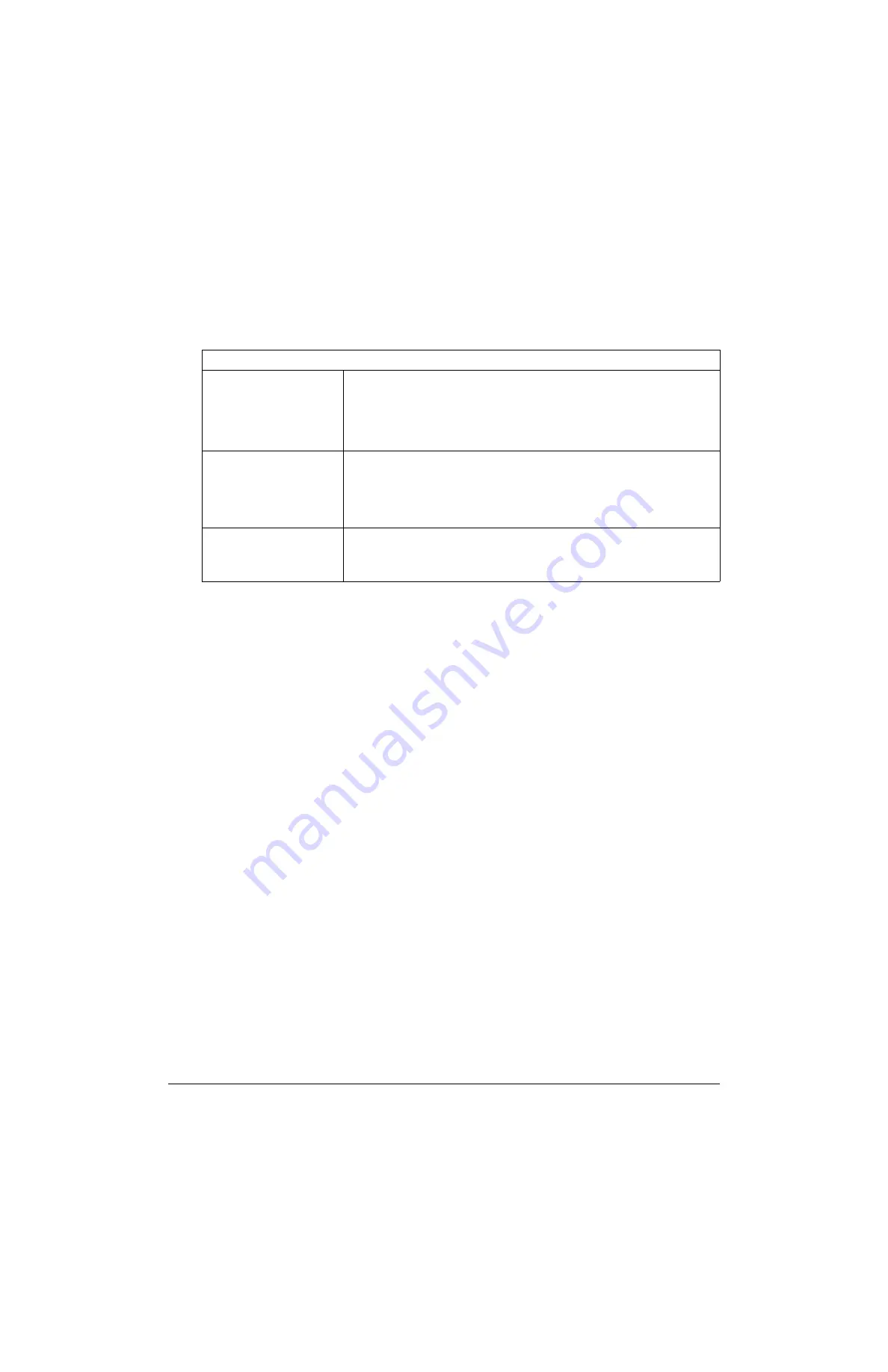
Operation
6
XPR300
Instruction Manual
809480
233
Hypertherm’s pierce control and assist technology can minimize timing and torch height issues that
can have a negative effect on piercing processes.
* Also known as “pierce complete.”
Recommendations for marking processes
Alternate between marking and cutting processes. Marking without intermittent cutting can
shorten the life of consumables.
Recommendations for bevel-cutting processes
When possible, pierce with the torch perpendicular to the workpiece and then tilt the torch.
Limit tilt rotation speed if necessary.
Maintain 2 mm – 3 mm (0.08 inch – 0.12 inch) of clearance between the torch and the
workpiece.
Use the effective thickness of the workpiece you are cutting to select cut speed.
With True Bevel™ technology, Hypertherm provides you with flexible and
adjustable bevel compensation cut charts, or process parameter tables,
that automatically compensate key settings such as torch height and cut
speed.
Pierce control* and assist technology
Pierce delay settings
• The operator selects the time (in seconds) necessary to pierce through
the full thickness of the metal.
• The operator enters this setting from the CNC or XPR web interface.
• For recommendations on how to choose the best pierce-delay setting,
see the cut charts. the
XPR Cut Charts Instruction Manual
(809830).
Shield pierce gas signal
• This signal enables the shield pierce flow function.
• This signal must be activated with the Plasma Start command. Refer to
on page 210. For information about commands
and signals, refer to the
CNC Communication Protocol for the XPR
Cutting System
(809810).
Shield pierce flow setting
• The shield pierce gas setting is used during pierce operation.
• The shield pierce gas setting is active until pierce delay expires.
• The shield pierce gas setting can be offset or overridden.
Summary of Contents for XPR170
Page 1: ...XPR300 Instruction Manual 809480 REVISION 6 ENGLISH ...
Page 8: ......
Page 38: ...Specifications 1 38 809480 Instruction Manual XPR300 ...
Page 72: ...Qualifications and Requirements 2 72 809480 Instruction Manual XPR300 ...
Page 146: ...Installation 3 146 809480 Instruction Manual XPR300 ...
Page 202: ...Coolant Installation 5 202 809480 Instruction Manual XPR300 ...
Page 236: ...Operation 6 236 809480 Instruction Manual XPR300 ...
Page 360: ...Diagnostics and Troubleshooting 8 360 809480 Instruction Manual XPR300 ...
Page 406: ...Parts List 9 406 809480 Instruction Manual XPR300 ...
Page 417: ...417 Overview Sheet 1 of 22 013403 013403 ...
Page 418: ...418 Plasma power supply 1 Sheet 2 of 22 013403 ...
Page 419: ...419 Plasma power supply 2 Sheet 3 of 22 013403 ...
Page 420: ...420 Plasma power supply 3 Sheet 4 of 22 013403 ...
Page 421: ...421 Plasma power supply 4 Sheet 5 of 22 013403 ...
Page 422: ...422 Plasma power supply 5 Sheet 6 of 22 013403 ...
Page 423: ...423 Plasma power supply 6 Sheet 7 of 22 013403 ...
Page 424: ...424 Plasma power supply 7 Sheet 8 of 22 013403 ...
Page 425: ...425 Gas connect console 1 Sheet 9 of 22 013403 ...
Page 426: ...426 Gas connect console 2 Sheet 10 of 22 013403 ...
Page 427: ...427 Torch connect console Sheet 11 of 22 013403 ...
Page 428: ...428 Coolant system Sheet 12 of 22 013408 ...
Page 429: ...429 Gas system 1 Sheet 13 of 22 013403 ...
Page 430: ...430 Gas system 2 Sheet 14 of 22 013403 ...
Page 431: ...431 Gas system 3 Sheet 15 of 22 013403 ...
Page 438: ...438 Wireless subsystem block diagram Sheet 22 of 22 013403 ...