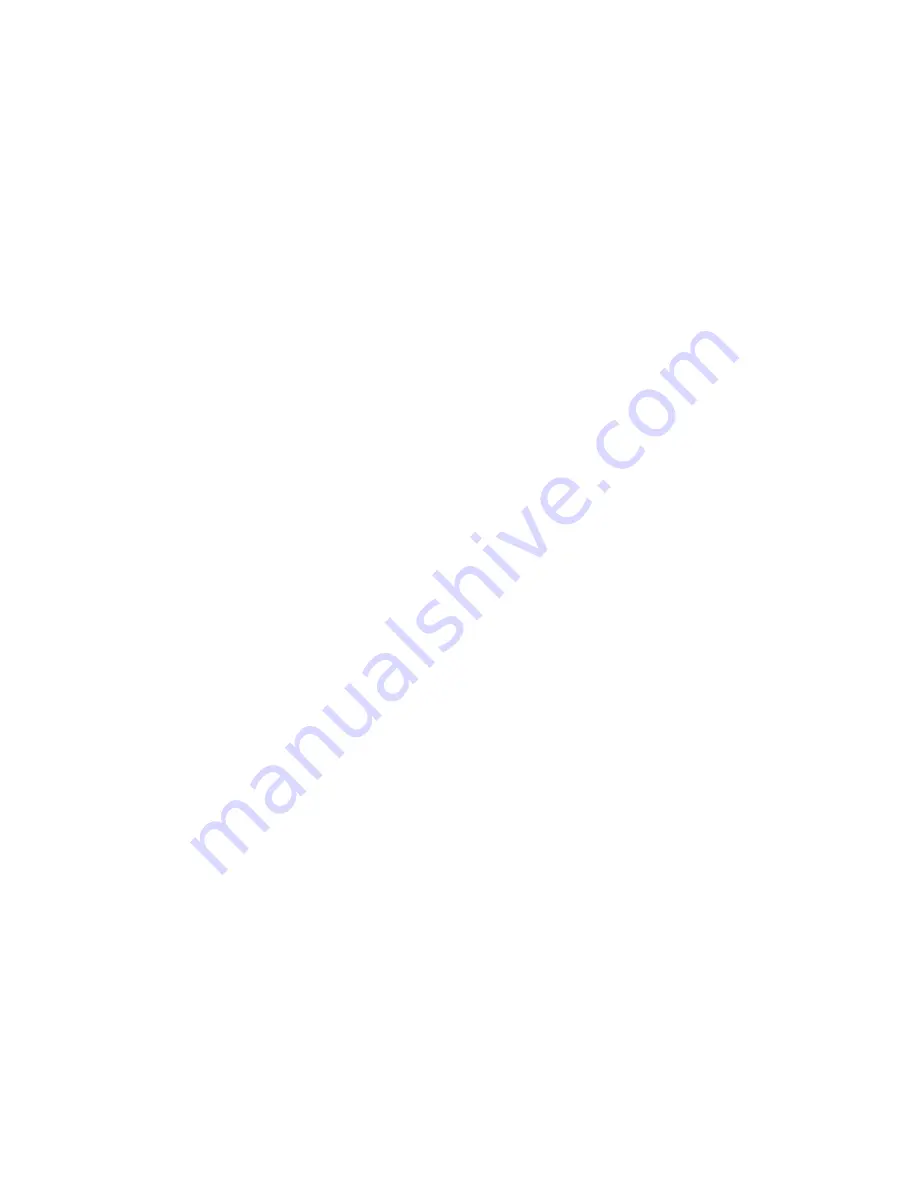
Program Codes
438
Serial Messaging
The Serial Messaging feature may be used to pass commands embedded within a part program
through a selected serial port to an external device. Both RS-232 and RS-422 are supported. TCP/
IP protocol is not supported at this time.
Overview
Serial Messaging has a fairly basic communication protocol that has three simple formats to send
ASCII codes as command strings. During the messaging function, a status indicator for “Message
Transmit”, “Message Delay” or “Message Verify” will be displayed in the Watch window.
Options
1)
While the selected message is sent to the external device, the part program will be temporarily
suspended. After completion of the transmission, the part program will then automatically
resume. No acknowledgement from the external device is required. An additional Time Delay
may also be added.
2)
A message is sent concurrent to execution of the part program and no delay is encountered.
No acknowledge is required. No Delay Time is allowed.
3)
The message is sent with a suspension of the program during transmission as in option one,
but an Acknowledge from the external device (ACK) is required before the part program can
continue. A Non-Acknowledge (NAK) response from the external device will prompt a
retransmit of the message from the control. An optional Time Out value may be added to the
program code. If no Time Out code is used in the program code the Default time out value at
the Ports setup screen will be used. Additionally, an optional automatic retry feature may be
enabled at the Ports setup screen.
To enable use of this feature, assign Messaging to the select port at the Ports setup screen.
Summary of Contents for Edge TI
Page 24: ...Table of Contents XXII...
Page 41: ...Overview 17 Alpha Numeric Keypad Numeric Keypad...
Page 54: ...Overview 30...
Page 83: ...Setups 59 Water Jet Press the Timing Diagram soft key to view the timing diagram from setups...
Page 88: ...Setups 64...
Page 116: ...Shape Manager 92...
Page 128: ...Files 104...
Page 280: ...Part Options 256...
Page 317: ...Diagnostics 293 DriveTop from Indramat...
Page 402: ...Phoenix Link 378...
Page 420: ...Sensor THC 396...
Page 428: ...Command THC 404...
Page 436: ...Motion Overview 412 Motion Tuning Watch Windows Position and Following Error may be displayed...
Page 470: ...Program Codes 446...
Page 478: ...Automated Plasma Interface 454 Inputs...
Page 479: ...Automated Plasma Interface 455 Inputs...
Page 480: ...Automated Plasma Interface 456 Outputs...
Page 496: ...Automated Plasma Interface 472...
Page 520: ...MicroEdge 496...
Page 532: ...Edge Ti 508 Optional Motor Information...
Page 540: ...Edge Ti 516...
Page 546: ...Voyager III 522 Examples of possible circuits Output Input 24 VDC Com...
Page 557: ...Networking 533 7 Double Click on the network interface connected to your LAN...
Page 558: ...Networking 534...
Page 561: ...Networking 537...
Page 562: ...Networking 538 13 Double click on the System 14 Select the Computer Name tab...
Page 572: ...Networking 548...
Page 573: ......