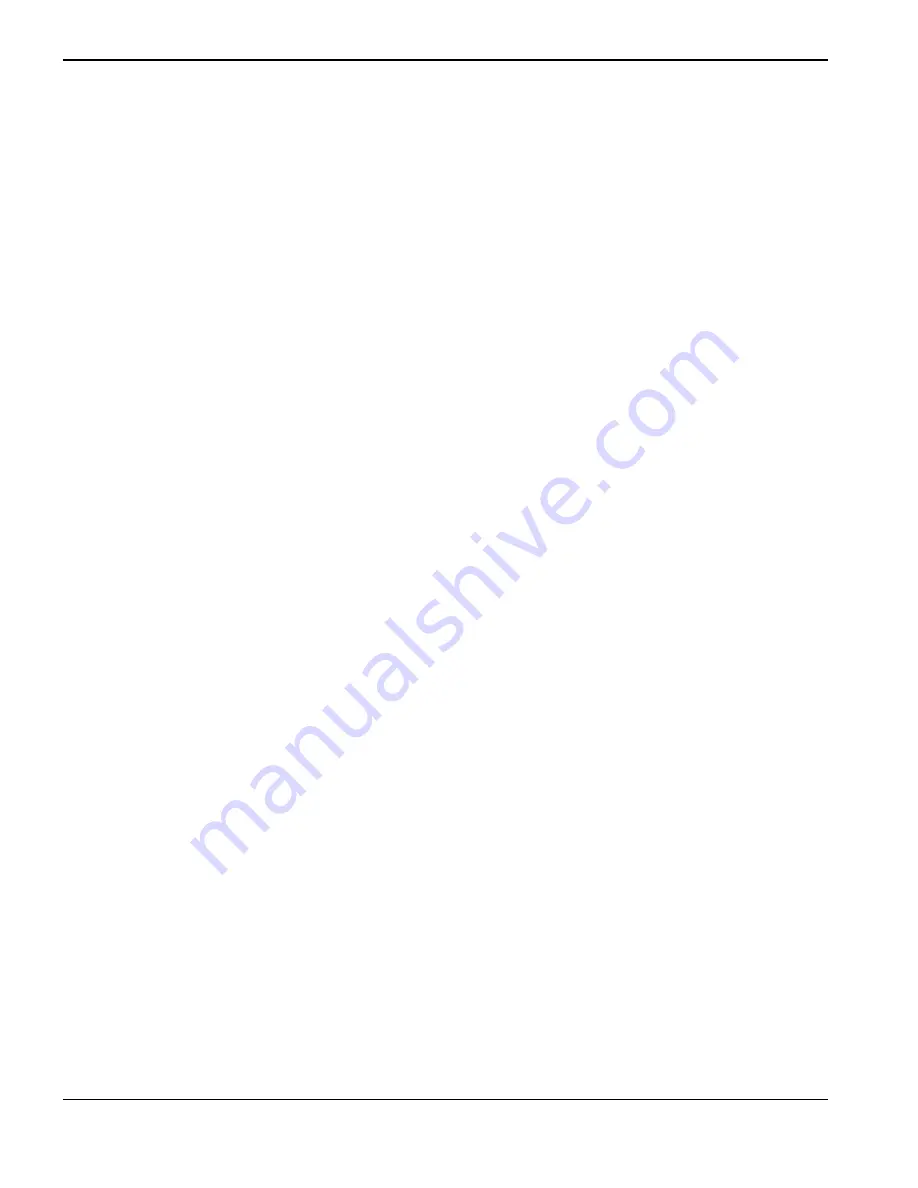
74
Duramax/Duramax Hyamp Robotic Torches
Service Manual 807460
5 – Maintenance and Parts
Accessory parts
Part Number
Description
024548
Brown leather torch sheathing, 7.6 m (25 feet)
024877
Black leather torch sheathing with Hypertherm logo, 7.6 m (25 feet)
228806
Kit: Robotic clamp torch assembly
229456
Duramax robotic torch teach assembly
Summary of Contents for Duramax
Page 1: ...Duramax and Duramax Hyamp Robotic Torches 45 90 180 Service Manual 807460 Revision 2 English ...
Page 6: ......
Page 10: ...10 Duramax Duramax Hyamp Robotic Torches Service Manual 807460 Contents ...
Page 20: ...20 Duramax Duramax Hyamp Robotic Torches Service Manual 807460 1 Specifications ...
Page 46: ...46 Duramax Duramax Hyamp Robotic Torches Service Manual 807460 2 Torch Setup ...