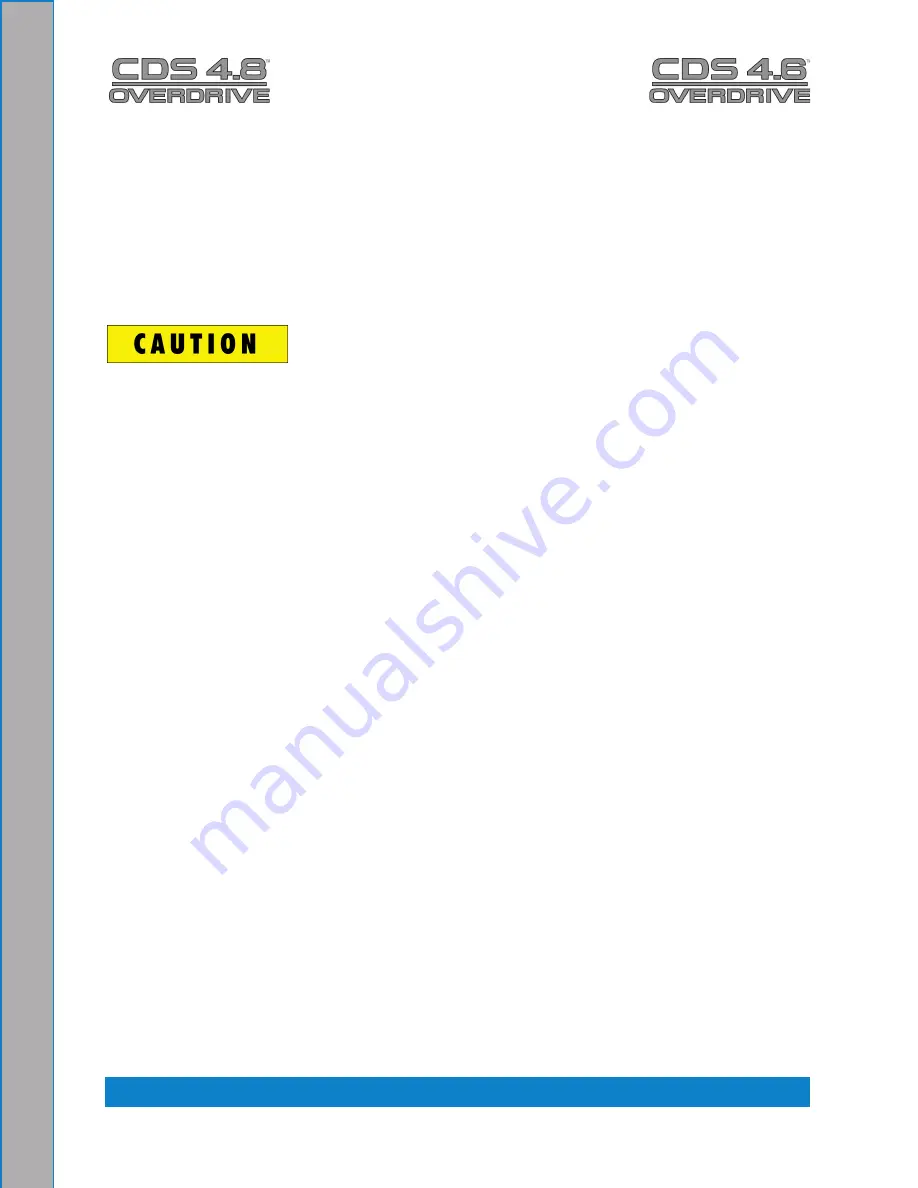
Chemicals and Cleaning: 2-2
CLEANINg PRECAUTIONS
There are no short cuts to good carpet cleaning. It requires time, cleaning knowledge and
the use of good chemicals. Therefore, the manufacturer recommends the use of spotting
agents and traffic lane cleaners, as required, prior to the actual cleaning of carpeting.
HydraMaster also recommends only the use of chemicals containing rust and corrosion
inhibitors, and water softening agents to prevent chemical build-up which may lead to
component failure and warranty invalidation.
Some acid rinse products can cause damage to internal machine components. failure
to take appropriate measures to prevent acidic corrosion can result in system failure and
loss of warranty on affected parts.
HydraMaster will not warranty parts that have been damaged from using acid products
that have obviously caused failures.
Avoid using detergents and chemicals which create foam when those products are
agitated because foam passing through the blower could lead to serious mechanical
failures. To ensure proper cleaning, use HydraMaster detergents and chemicals which
are formulated with built in anti-foaming agents. When cleaning surfaces with excessive
foaming residue, use HydraMaster de-foamer products as directed.
CLEANINg STROKE PROCEDURE
To eliminate excess moisture remaining in the carpet fiber and eliminate the sawtooth
appearance which results from diagonal movement of the cleaning tool, follow these
steps.
Always move the cleaning tool in smooth, forward and backward stroke
1.
Apply slight pressure to the forward stroke while the solution is injected into the
2.
carpet.
When extracting (drying), apply firm pressure on the forward stroke to ensure a
3.
positive “lock” for the vacuum and minimize the “hopping” effect resulting on carpet
that is not smooth.
During the forward and reverse strokes, movement to the right or left should only be
4.
done at the extreme rear of the stroke.
overlapping is also important to ensure even application of solution and prevent
5.
saturation when the cleaning tool is stopped twice at the same point at the rear of
the cleaning stroke figure 2-2.
Summary of Contents for CDS 4.6
Page 44: ...Assemblies and Parts Lists 7 2 CDS Machine Assembly Rear View Figure 7 2 7145 Rev C ...
Page 46: ...Assemblies and Parts Lists 7 4 CDS Recovery Tank Assembly Front View Figure 7 2 6977 Rev B ...
Page 47: ...7 5 Assemblies and Parts Lists CDS Recovery Tank Assembly Rear View Figure 7 3 6977 Rev B ...
Page 50: ...Assemblies and Parts Lists 7 8 CDS Instrument Panel Assembly Front View Figure 7 5 6988 Rev C ...
Page 51: ...7 9 Assemblies and Parts Lists CDS Instrument Panel Assembly Rear View Figure 7 6 6988 Rev C ...
Page 61: ...7 19 Assemblies and Parts Lists CDS Pump Assembly Overview Figure 7 13 7429 Rev A ...
Page 65: ...7 23 Assemblies and Parts Lists CDS Dash Box Assembly Overall View Figure 7 16 7428 Rev A ...
Page 66: ...Assemblies and Parts Lists 7 24 CDS Dash Box Assembly Figure 7 17 Rear View 7428 Rev A ...
Page 68: ...Assemblies and Parts Lists 7 26 CDS Dash Panel Assembly Overall View Figure 7 18 7427 ...
Page 70: ...Assemblies and Parts Lists 7 28 CDS Water Box Assembly Overview Figure 7 20 6990 Rev C ...
Page 71: ...7 29 Assemblies and Parts Lists CDS Water Box Assembly Figure 7 21 Parts View 6990 Rev C ...
Page 101: ...7 59 Assemblies and Parts Lists Hydra Hoe Wand Assembly Figure 7 46 2660 ...
Page 110: ...Electrical System 9 2 Figure 9 1 CDS Electrical Schematic 7425 Rev B ...
Page 111: ...9 3 Electrical System Figure 9 2 CDS Wiring Diagram 7426 Sht 2 Rev C ...
Page 112: ...Electrical System 9 4 Figure 9 3 CDS Wiring Diagram 7426 Sht 3 Rev C ...