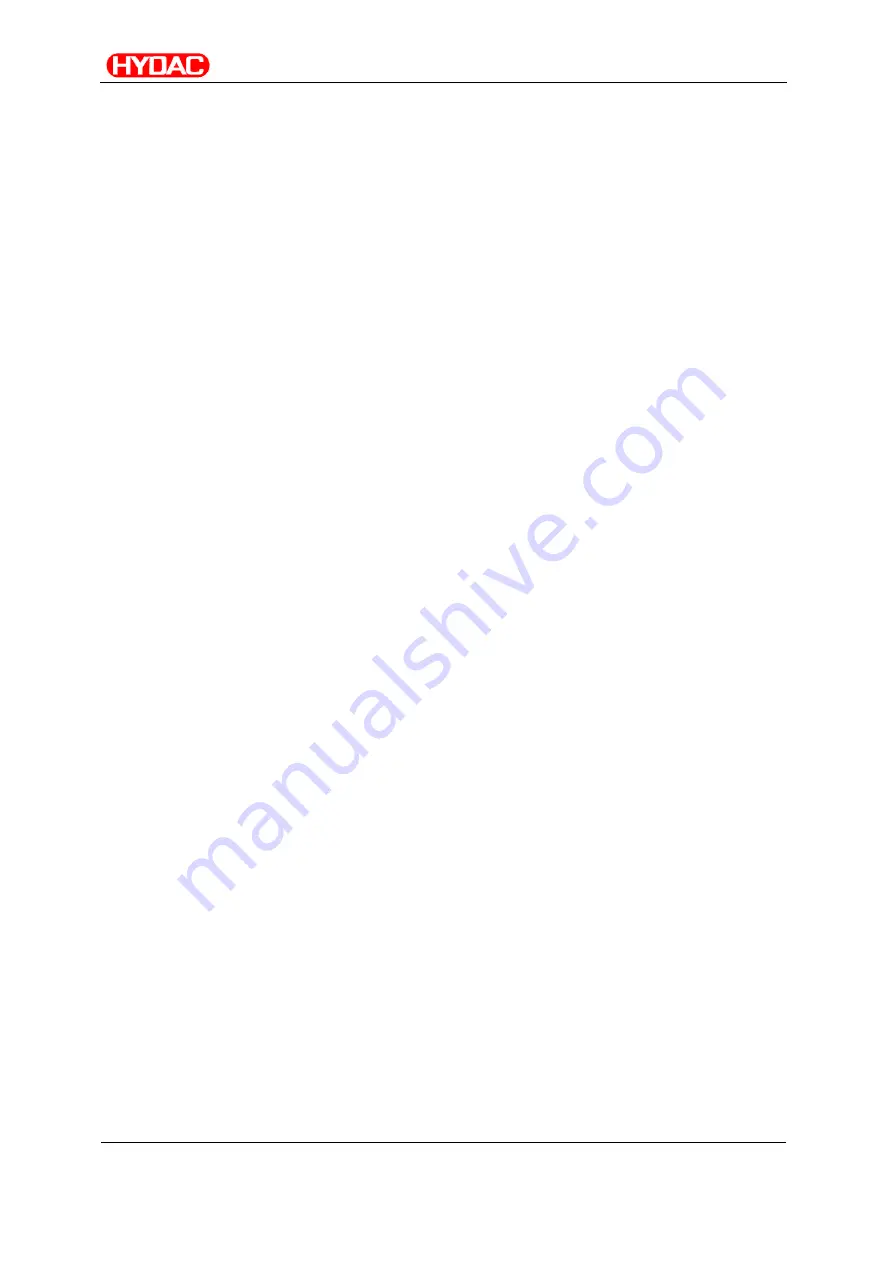
Safety information and instructions
Filtromat – OF5 C with FCU
en(us)
Page 13 / 44
BeWa OF5C 3160333b en-us 2014-07-28.doc
2014-07-28
Wear suitable clothing
Loosely worn clothing increases the danger of getting caught or wound up in
rotating parts and the danger of getting snagged on projecting parts. You can
be severely injured or killed.
Wear close-fitting clothing.
Do not wear any rings, chains or any other jewelry.
Wear work safety shoes.
Structural modifications
Do not make any modifications to the product without the prior consent of the
manufacturer.
Any modifications require written permission from HYDAC Filter Systems
GmbH
Use only original spare parts (OEM).
Summary of Contents for Filtromat OF5 C with FCU
Page 43: ......