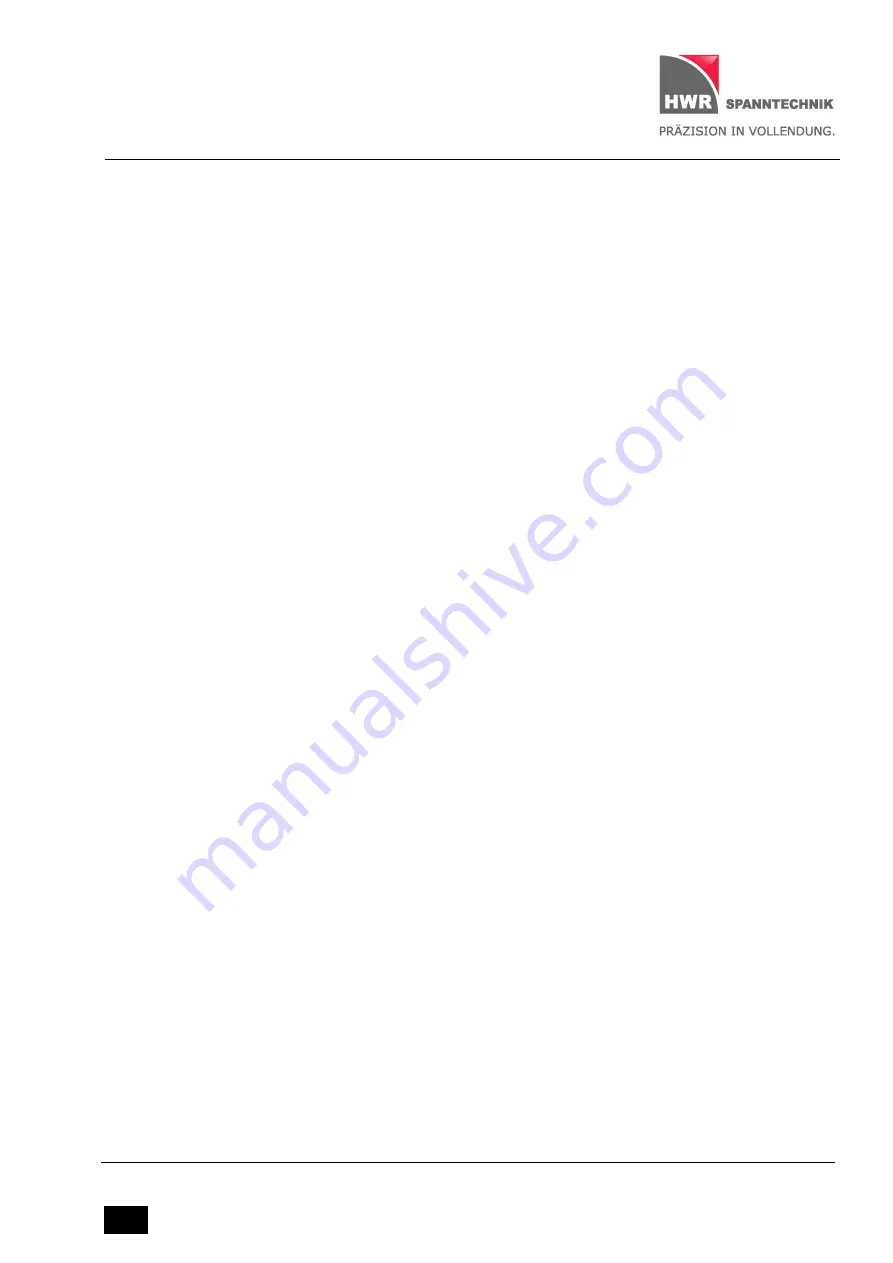
7
Technicl Data
Page 7-34
InoFlex
®
VF016 - VF026
© Copyright
Edition C
HWR Spanntechnik GmbH
EN
7
T
ECHNICAL
D
ATA
7.1
G
ENERAL INFORMATION
All important technical data for the InoFlex
®
manual centering vice is in-
cluded in this chapter. The data is listed in tables and structured according
to individual sizes.
Summary of Contents for InoFlex VF016
Page 8: ......