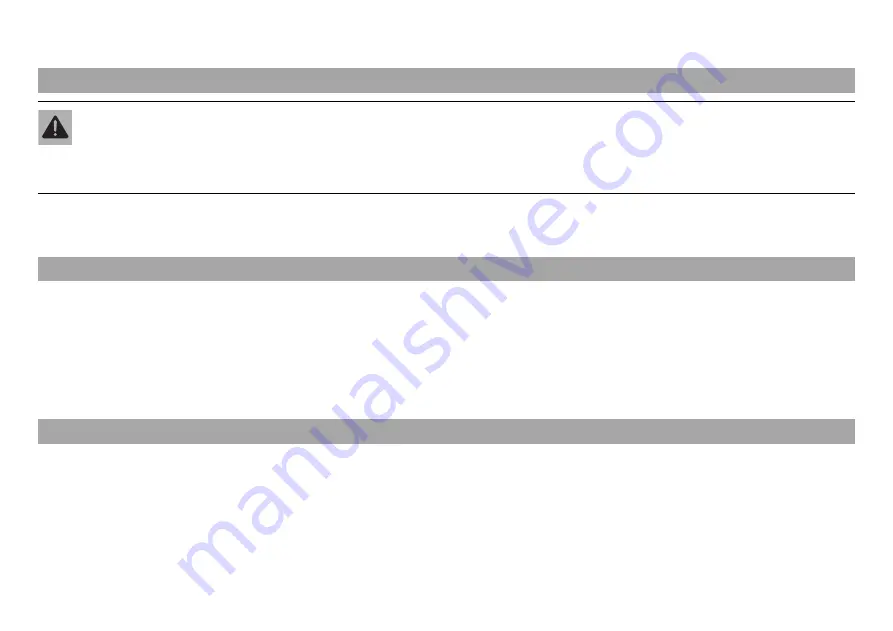
2
SAFETY ADVICE
19
2.11
Protective clothing
Warning
Risk of injury
Missing or poor protective clothing presents an increased safety risk.
–
Wear protective clothing (helmet, boots, gloves, pants and jacket with protectors) every time you ride the vehicle. Always
wear protective clothing that is in good condition and meets the legal requirements.
In the interest of your own safety, Husqvarna Motorcycles recommends that you only operate the vehicle while wearing protective
clothing.
2.12
Work rules
Special tools are necessary for certain tasks. The tools are not contained in the vehicle but can be ordered under the number in paren-
theses. E.g.: bearing puller (15112017000)
During assembly, non-reusable parts (e.g. self-locking screws and nuts, seals and seal rings, O-rings, pins, lock washers) must be
replaced by new parts.
In some instances, a thread locker (e.g.
Loctite
®
) is required. The manufacturer instructions for use must be followed.
After disassembly, clean the parts that are to be reused and check them for damage and wear. Change damaged or worn parts.
After you complete the repair or service work, check the operating safety of the vehicle.
2.13
Environment
If you use your motorcycle responsibly, you can ensure that problems and conflicts do not occur. To protect the future of the motorcy-
cle sport, make sure that you use your motorcycle legally, display environmental consciousness, and respect the rights of others.
When disposing of used oil, other operating and auxiliary fluids, and used components, comply with the laws and regulations of the
respective country.
Because motorcycles are not subject to the EU regulations governing the disposal of used vehicles, there are no legal regulations that
pertain to the disposal of an end-of-life motorcycle. Your authorized Husqvarna Motorcycles dealer will be glad to advise you.
Summary of Contents for 701 Supermoto 2016
Page 1: ...OWNER S MANUAL 2016 701 Supermoto Art no 3402073en ...
Page 2: ......
Page 13: ...11 ...
Page 14: ...2 SAFETY ADVICE 12 2 4 Overview of labels H00430 10 ...
Page 16: ...2 SAFETY ADVICE 14 M01408 01 Information noise emission M01406 01 Type label USA ...
Page 17: ...2 SAFETY ADVICE 15 M01405 01 Type label Canada M01407 01 Information emission control ...
Page 25: ...23 ...
Page 26: ...4 VIEW OF VEHICLE 24 4 1 View of vehicle front left side S01031 01 ...
Page 28: ...4 VIEW OF VEHICLE 26 4 2 View of vehicle rear right side S01032 01 ...