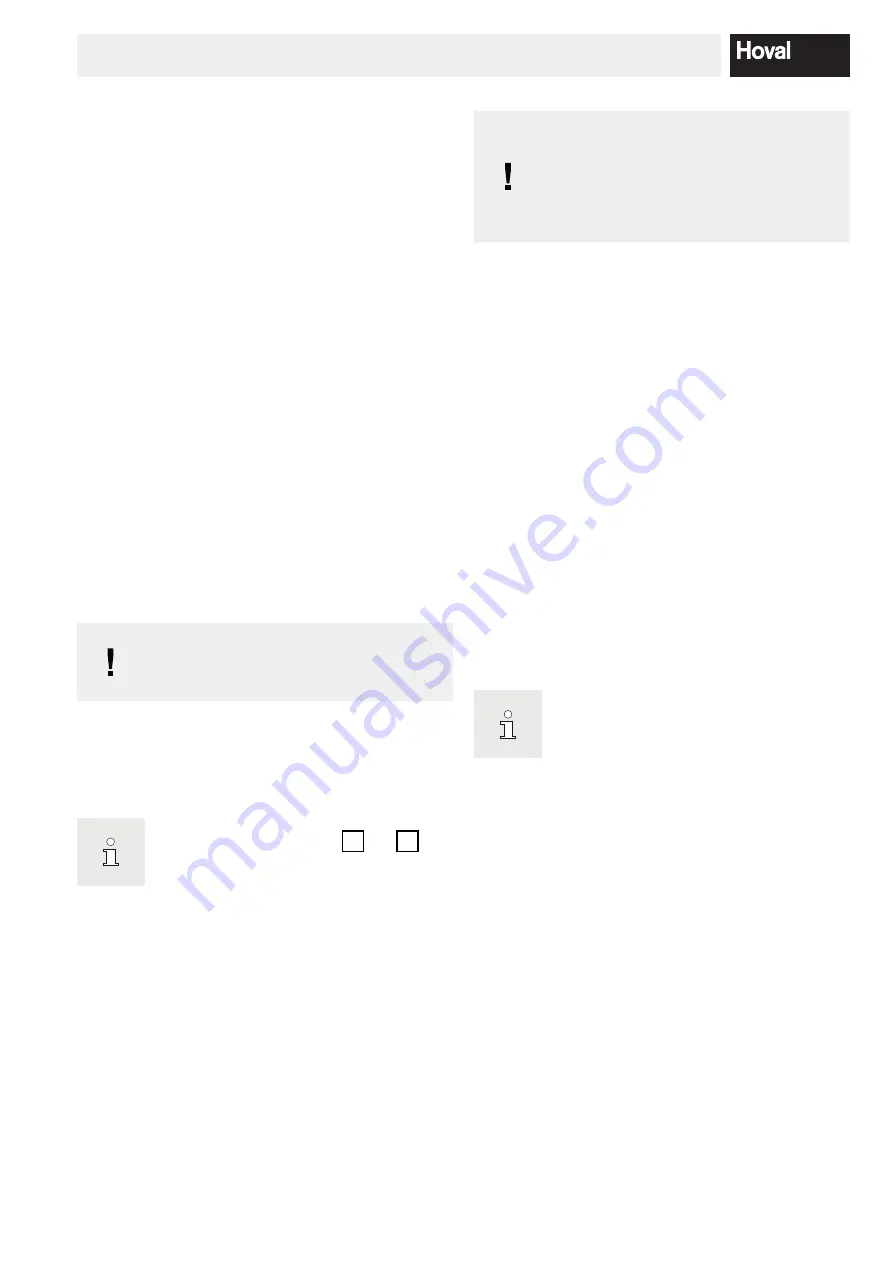
19
4 219 316 / 00
InSTaLLaTIOn
3.
Installation
3.1
Boiler installation room
Hoval condensing boilers in the series TopGas
®
classic
can be combined with flue gas con duits which
a) draw in combustion air from the installation room
(room-air dependent gas firing system)
b) draw in combustion air from outside via a closed
system (room-air-independent gas firing system)
The boiler installation rooms must comply with the rele-
vant local regulations (firing ordinance, regulations of the
fire prevention authority). In particular, the stipulations of:
- DVGW-TRGI
must be observed and complied with.
In the case of room air dependent operation, it must be
ensured that the combustion air is free of contamination
(dust, building materials,...) and aggressive substances
(halogens such as chloride, fluoride etc.). Gas boilers
should not be connected to the mains gas supply or put
into operation until all construction work in the installation
room is completed.
3.1.1 Installing the boiler
The Hoval TopGas
®
classic is delivered as follows.
Box: Boiler; casing parts; installation
and operating instructions.
NOTE
The boiler must not be placed on its connec-
tor elements.
The boiler is mounted in the desired position on the wall.
Side clearance: at least 5 cm; distance from the ceiling:
the required clearance for the type and dimensions of the
lines for combustion air and flue gas must be observed.
Please note dimensions and instructions in
the drawings in the chapters 2.4 and 2.5.
3.2
Hydraulic switching
The Hoval TopGas
®
classic is designed for continuously
controlled operation (room tem pe rature control/weath-
er-controlled boiler and heating cir cuit con trol) without
lower temperature limit.
Please observe the notes in the configuration documents
of the responsible Hoval companies with respect to the
ap propriate hydraulic switching.
NOTE
When modernising an old heating system
with an open expansion tank, this is to be
con
ver
ted to a «closed» heating system
with a diaphragm expansion tank and safety
valve.
3.2.1 Engineering guidelines for the hydraulic
switching
• Installation of a sludge collector in the boiler return is
recommended (observe the correct dimensioning).
• An adequately dimensioned expansion tank must be
pro vi ded.
• The minimum pre-pressure in the expansion tank must
be 1,2 bar and the working pressure in the boiler must
be 1,5 bar.
• The pump is to be connected in the boiler return and the
expansion tank in the suction side of the pump.
• If the system pressure cannot to be reached (e.g. roof
central heating plants), the expansion tank must be in-
stalled in the boiler flow. (Note: starting from 70 °C an
additional in-line vessel is necessary).
• Plants with
-
continuous
oxygen intake (e.g. underfloor heating
systems without diffusion-proof plastic piping) or
-
intermittent
oxygen intake (e.g. requiring frequent
topping-up)
must be equipped with separate circuits.
We also recommend the conclusion of a main-
tenance contract!
3.2.2 Water pressure guard for water shortage
protection
To protect the boiler against excessively low water pres-
sure/water level, a water pressure switch is mounted on
the return distributor as standard (AMP connectors at po
-
sitions 1 and 3). The boiler is switched off if the water
pres sure falls below 1 bar ("P27" is shown on the dis
-
play). Please check the system pressure and top up with
wa ter if necessary.
Summary of Contents for TopGas classic 100
Page 46: ...46 4 219 316 00...
Page 47: ...47 4 219 316 00...