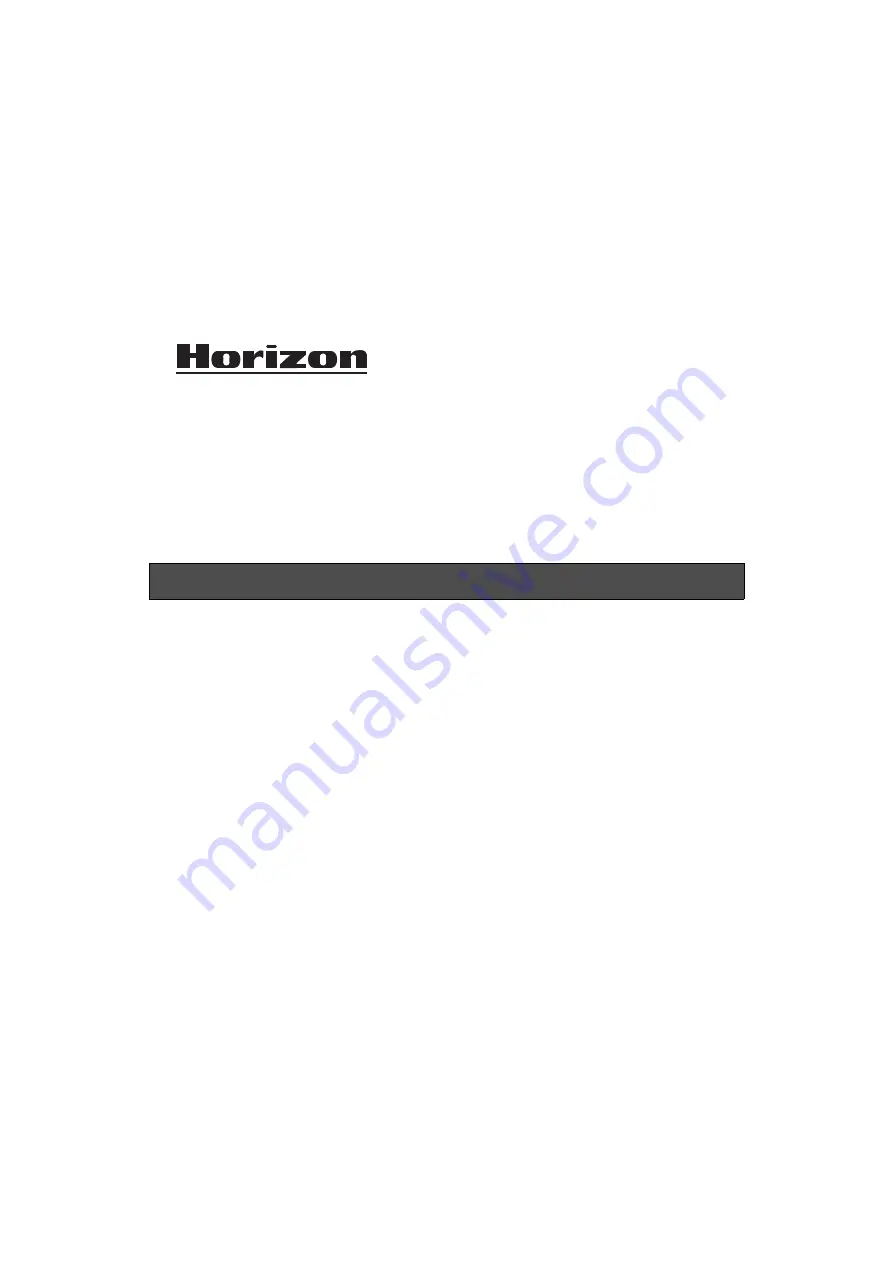
I
• This manual is designed to help you to install, operate and maintain the AFC-
566F Cross Folder. Please read and understand this manual, and keep it in a
safe and convenient place.
• Do not operate the AFC-566F until you read and understand the instructions in
this manual.
• Horizon International Inc. shall not be liable for incidental consequential
damages resulting from: improper or inadequate maintenance by the customer,
unauthorized modification or misuse, or operation outside of the environmental
specifications for the product.
• Horizon International Inc. pursues a policy of continuing improvement in design
and performance of the product. Therefore, the product design and
specifications are subject to change without prior notice and without our legal
obligation.
• All rights are reserved. No part of this manual may be photocopied, reproduced
or translated to another language without the prior written consent of Horizon
International Inc.
Important Information
CROSS FOLDER
CROSS FOLDER
AFC-566F
170228/566F/32E/TI,TM,AT/F7/ICS5.5/PXI
UM203051-32(000)
*UM203051*