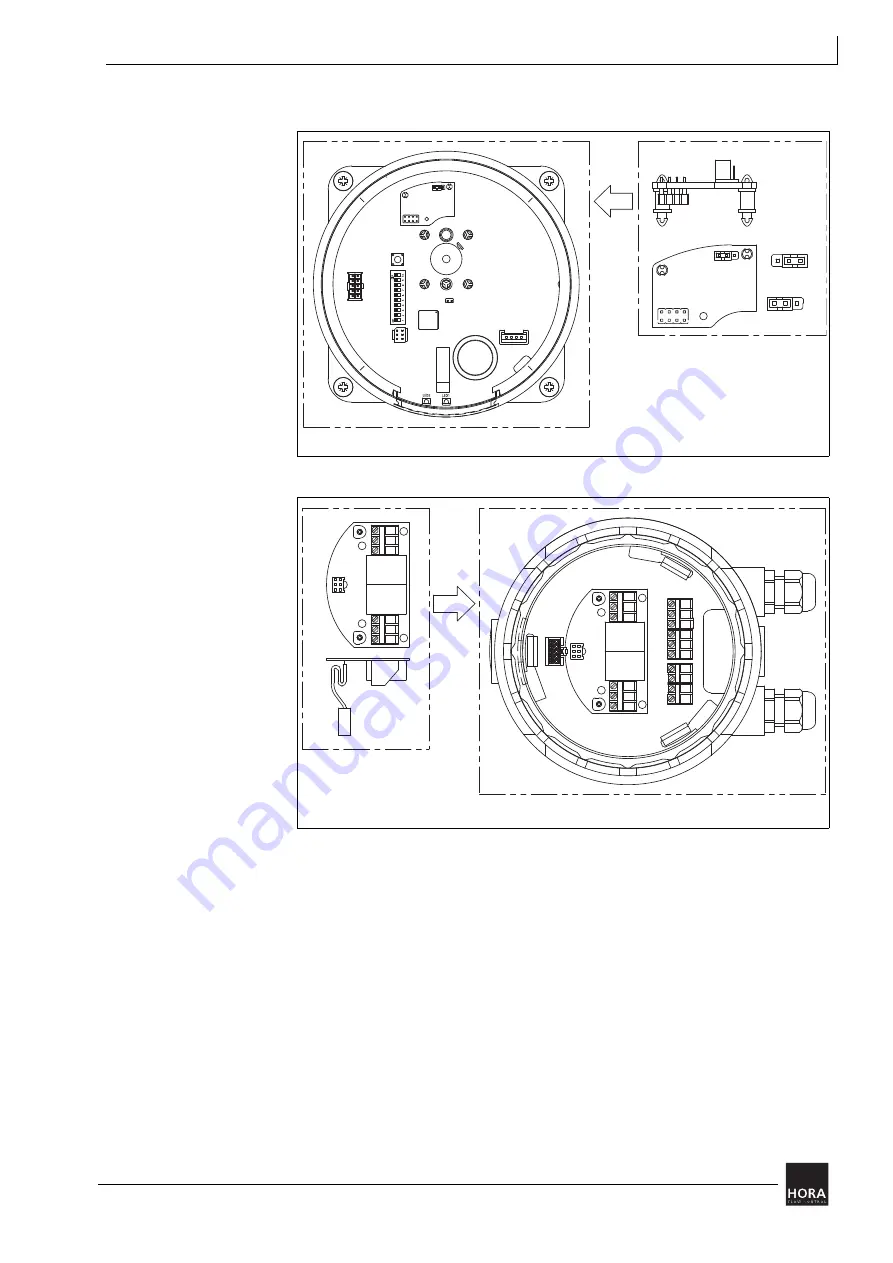
2 Product Specification
Linear actuators MC250 • MC253 • MC500 • MC503
Operating Manual
Version 2.1 - March 2011
7
2.2
Accessories
2.3
Operating modes
The linear actuator can be operated in Manual or Automatic mode.
•
The lift is adjusted via the handwheel in Manual mode.
•
The lift is electrically controlled in Automatic mode.
2.3.1
Continuous mode
In Continuous mode the position of the linear actuator is specified by the system
control. The input signal (Y) from the system control in the linear actuator is
continually compared with the output signal (X) from the linear actuator for this
purpose. The output signal is dependent on the position of the linear actuator
(travel) in this instance.
The linear actuator moves until the input signal and the output signal correspond.
111
Printed circuit board for output signal X=0/4 … 20 mA
Diagram 2
Printed circuit board for mA output signal on the motherboard
106
Way-switch printed circuit board
Diagram 3
Way-switch printed circuit board in cover
0...20 mA
4...20 mA
111
LED1
LED2
LED2
LED1
106