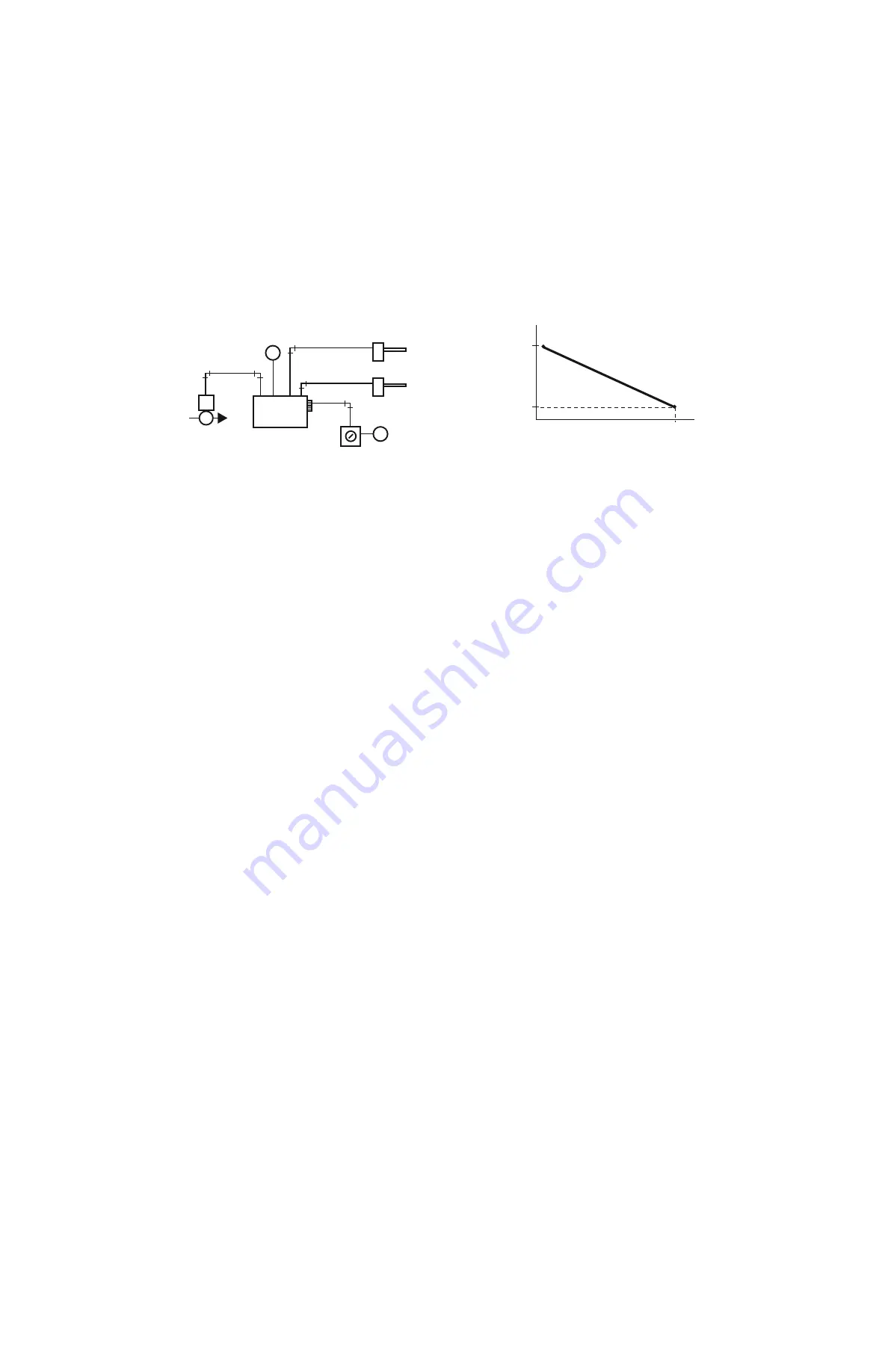
Sensor-Controller Systems
136
customer.honeywell.com
70-6925
Fig. 22. Dual-Input Controller with
Manual Remote Setpoint.
Proportional-Integral (PI) Controllers
Variations of single-input and dual-input controllers can provide
proportional-integral (PI) control. PI controllers are used in
critical applications that require closer control than a
proportional controller. A PI controller provides close control by
eliminating the deviation from setpoint (offset) that occurs in a
proportional controller system. PI controllers are similar to the
controllers in Figures 21 and 22 and have an additional knob for
adjusting the integral reset time.
Controller Adjustments
Controller operation is adjusted in the following ways:
— Adjusting the setpoint
— Changing between direct and reverse control action
— Adjusting the proportional band (throttling range)
— Adjusting the reset authority
— Adjusting the integral control reset time
The setpoint can be manually adjusted with a dial on the
controller. Remote setpoint adjustment is available for all
controllers. Control action may be direct or reverse, and is field
adjustable. The proportional band setting is typically adjustable
from 2.5 to 50 percent of the primary sensor span and is usually
set for the minimum value that results in stable control. In a
sensor with a span of 200 degrees F, for example, the minimum
setting of 2.5 percent results in a throttling range of 5 degrees F
(0.025 x 200 = 5 degrees F). A change of 5 degrees F is then
required at the sensor to proportionally vary the controller
branchline pressure from 3 to 13 psi. A maximum setting of 50
percent provides a throttling range of 100 degrees F (0.50 x 200
= 100 degrees F).
Reset authority, also called “reset ratio”, is the ratio of the effect
of the reset sensor compared to the primary sensor. Figure 23
shows the effect of authority on a typical reset schedule. The
authority can be set from 10 to 300 percent.
Fig. 23. Typical Reset Schedule for
Discharge Air Control.
The integral control reset time determines how quickly the PI
controller responds to a change in the controlled variable.
Proportional correction occurs as soon as the controlled
variable changes. The integral function is timed with the reset
time adjustment. The reset time adjustment is calibrated from
30 seconds to 20 minutes. The proper setting depends on
system response time characteristics.
Pneumatic Sensors
Pneumatic sensors typically provide a direct acting 3 to 15 psi
pneumatic output signal that is proportional to the measured
variable. Any change in the measured variable is reflected as a
change in the sensor output. Commonly sensed variables are
temperature, humidity, and differential pressure. The sensors
use the same sensing elements and principles as the sensors
in the controllers described earlier, but do not include setpoint
and throttling range adjustments. Their throttling range is the
same as their span.
A gage connected to the sensor output can be used to indicate
the temperature, humidity, or pressure being sensed. The gage
scale is calibrated to the sensor span.
Temperature sensors may be vapor-filled, liquid-filled,
averaging capillary, or rod-and-tube. The controller usually
provides restricted air to the sensor.
Humidity sensors measure the relative humidity of the air in a
room (wall-mounted element) or a duct (insertion element).
Nylon is typically used as the sensing element. Humidity
sensors include temperature compensation and operate on a
force-balance principle similar to a wall thermostat.
The low-pressure sensor measures duct static pressure and
differential pressure. When the duct static pressure or the
pressure differential increases, branchline pressure increases.
Velocity Sensor-Controller
The velocity sensor-controller combines a highly sensitive air
velocity sensor with a pneumatic controller to detect and control
airflow regardless of system static pressure. It is used in air
terminal units and other air handling systems. Reverse and
direct-acting models are available for normally closed and
normally open dampers.
M
MANUAL REMOTE
SETPOINT CONTROL
HOT WATER
VALVE
MAIN AIR
(18 PSI)
RESET SENSOR
PRIMARY
SENSOR
M10294
M
DA
TEMPERA
TURE
CONTROL
POINT
(F)
OUTDOOR AIR TEMPERATURE (F)
COMPENSATION
START POINT
60
0
30
130
C1094
Summary of Contents for VP525C
Page 58: ...50 customer honeywell com 70 6925 ...
Page 120: ...112 customer honeywell com 70 6925 ...