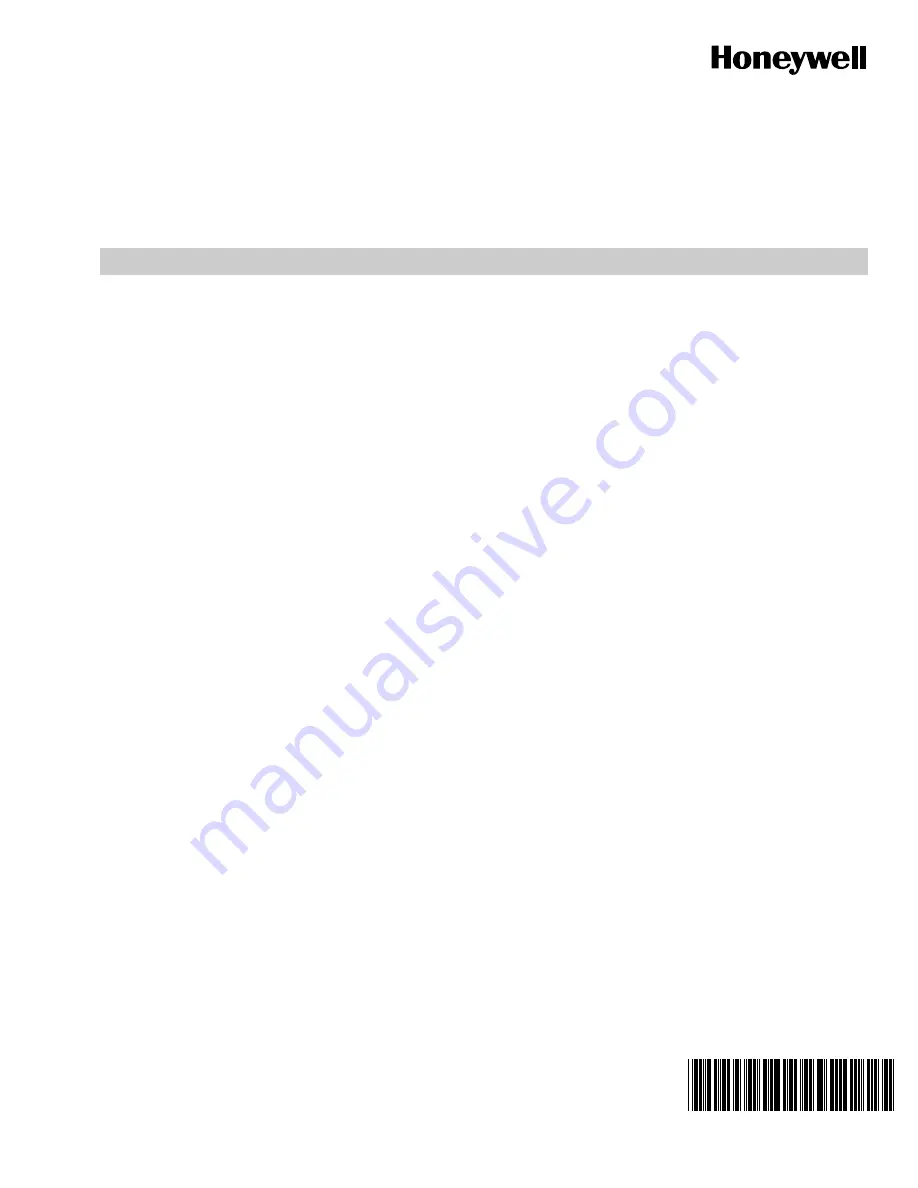
INSTALLATION INSTRUCTIONS
63-4528-04
Honeywell VFD CORE User and
Application Manual
CONTENTS
CHAPTER 1: Introduction ................................................................................................................ 2
CHAPTER 2: Installation................................................................................................................ 11
CHAPTER 3: Unpacking ................................................................................................................ 15
CHAPTER 4: Wiring ........................................................................................................................ 19
CHAPTER 5: Main Circuit Terminal .............................................................................................. 23
CHAPTER 6: Control Circuit Terminal .......................................................................................... 29
CHAPTER 7: Optional Components ............................................................................................. 35
CHAPTER 8: Installing the Option Cards ..................................................................................... 67
CHAPTER 9: Specifications .......................................................................................................... 87
CHAPTER 10: Digital Keypad........................................................................................................ 91
CHAPTER 11: Summaries of Parameter Settings ....................................................................... 97
CHAPTER 12: Description of Parameter Settings..................................................................... 123
CHAPTER 13: Warning Codes .................................................................................................... 243
CHAPTER 14: Fault Codes .......................................................................................................... 249
Summary of Contents for VFD CORE
Page 10: ...CHAPTER 1 INTRODUCTION 63 4528 04 10 ...
Page 14: ...CHAPTER 2 INSTALLATION 63 4528 04 14 ...
Page 22: ...CHAPTER 4 WIRING 63 4528 04 22 ...
Page 28: ...CHAPTER 5 MAIN CIRCUIT TERMINAL 63 4528 04 28 ...
Page 34: ...CHAPTER 6 CONTROL CIRCUIT TERMINAL 63 4528 04 34 ...
Page 84: ...ETHERNET IP COMMUNICATION CARD 63 4528 04 84 Figure 6 Figure 7 Figure 8 M33575 M33576 M33577 ...
Page 86: ...ETHERNET IP COMMUNICATION CARD 63 4528 04 86 ...
Page 122: ...CHAPTER 11 SUMMARIES OF PARAMETER SETTINGS 63 4528 04 122 ...
Page 242: ...CHAPTER 12 DESCRIPTION OF PARAMETER SETTINGS 63 4528 04 242 ...