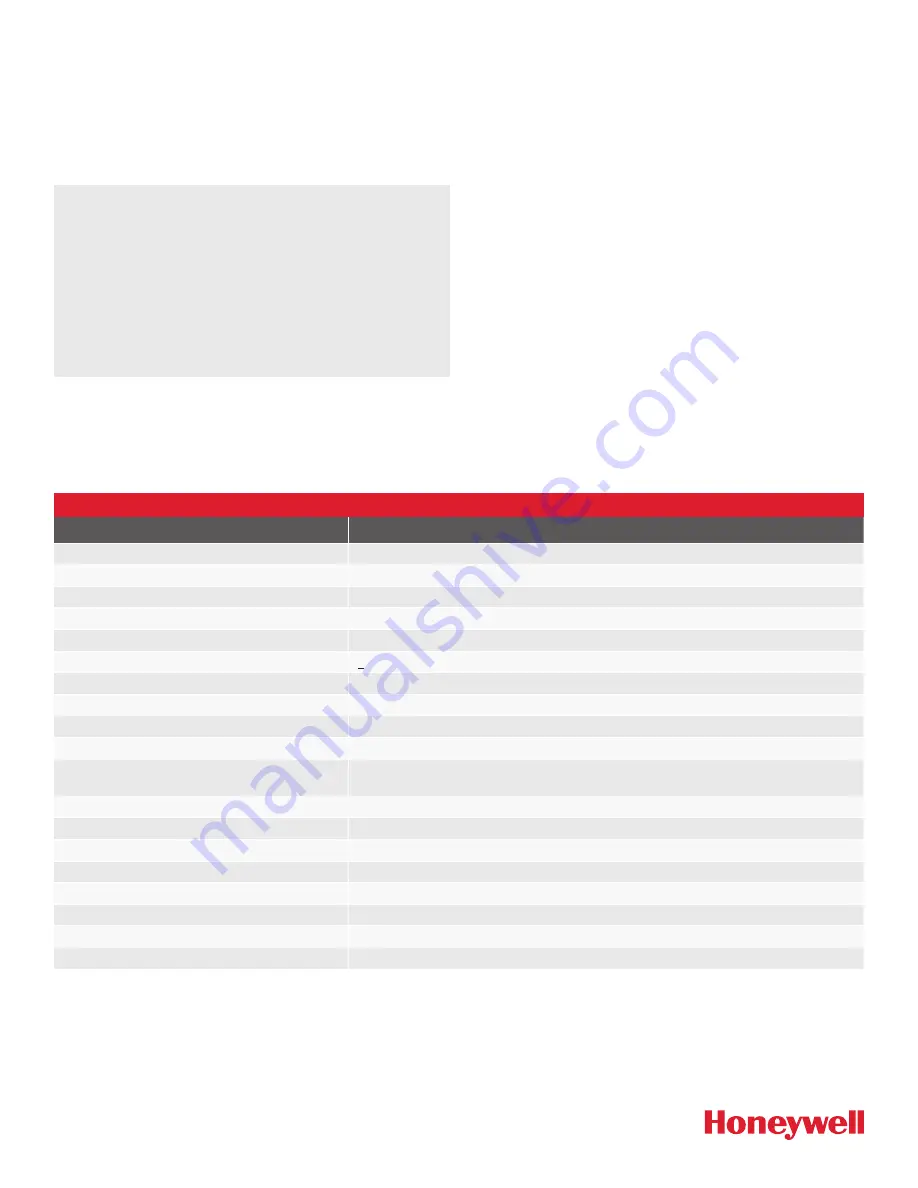
USER GUIDE FOR THE
COMMERCIAL CARBON DIOXIDE SENSOR,
400 PPM TO 2000 PPM (UP TO 5000 PPM
EXTENDED RANGE),
CRIR E1
000841
Issue 1
TABLE OF CONTENTS
1.0 GENERAL INFORMATION .............................................. 1
2.0 SENSOR HANDLING ........................................................ 3
3.0 AUTOMATIC BASELINE CORRECTION ....................... 3
4.0 TERMINATION ................................................................... 3
5.0 CALIBRATION..................................................................... 6
6.0 SELF-DIAGNOSTICS............................................. ............6
7.0 MODBUS REGISTER DEFINITION............................... ..6
8.0 MODBUS FUNCTION DESCRIPTION........................ ....9
1.0
GENERAL INFORMATION
The CRIR E1 Commercial Carbon Dioxide (CO
2
) sensor is a
single channel, non-dispersive infrared (NDIR) sensor. Within
the CRIR E1 is a sensing chamber with an infrared source at
TABLE 1. SPECIFICATIONS
CHARACTERISTIC
PARAMETER
Target gas
carbon dioxide (CO
2
)
Operating principle
non-dispersive infrared (NDIR)
Standard range
1, 2
400 ppm to 2000 ppm, up to 5000 ppm extended range
Measurement interval
4 s
Accuracy
3
±5
0 ppm
±5
% of reading
Typical response time (T
90
)
<120 s
Sensor warm-up time
3 minimum typical
Repeatability
>97%
Operating voltage
4.5 V to 5.5 V unprotected against surges and reverse connection
Power consumption
300 mA peak, 30 mA average
Alarm output, open collector
1000 ppm/800 ppm normal state is conducting maximum 100 mA.
Transistor open at CO
2
high or at sensor failure (see Figure 1).
Serial communication
5
UART, Modbus protocol
Operating temperature range
0°C to 50°C
Storage temperature range
-40°C to 70°C
Operating humidity
0 %RH to 90 %RH non-condensed
Expected operating life
10 years
Maintenance
6
maintenance-free for normal indoor applications
Weight
<8 g
Dimensions
33 mm x 22 mm X 11,2 mm (tolerance ±0,5 mm)
1
The CRIR E1 is designed to measure CO
2
in the range of 400 ppm to 2000 ppm with the accuracy specified in Table 1; however, exposure to
concentrations below 400 ppm may result in incorrect operation of the ABC algorithm and should be avoided when the ABC is ON.
2
The CRIR E1 provides readings via UART in the extended range; however, the accuracy is reduced.
3
In normal IAQ applications, the sensor accuracy is defined after a minimum of three ABC periods of continuous operation.
4
The sensor accuracy is specified over the operating temperature range and referenced to certified calibration mixtures. Uncertainty of calibration
gas mixtures (±1% currently) is to be added to the specified accuracy for absolute measurements.
5
See Sections 7.0 and 8.0 for Modbus address and parameter definitions.
6
The CRIR E1 normally does not require maintenance in IAQ applications; however, for some industrial applications, maintenance may be required.
one end and a detector fitted with an optical filter at the other
end. The source emits radiation at wavelengths which include
the absorption band of CO
2
. The filter blocks wavelengths which
are not sensitive to the presence of CO
2
, thereby increasing
selectivity and sensitivity. As the light passes through the
sensing chamber, a fraction is absorbed if CO
2
is present. The
difference between the light emitted by the source and received
by the detector can then be converted to a CO
2
concentration
reading. The Automatic Baseline Correction (ABC) function can
automatically calibrate the sensor’s lowest reading over a pre-
configured interval to 400 ppm CO
2
. This enhances long term
stability and may eliminate the need for calibration.
See Tables 1 and 2, and Figures 1 and 2 for specifications and
mounting and dimensional diagrams.