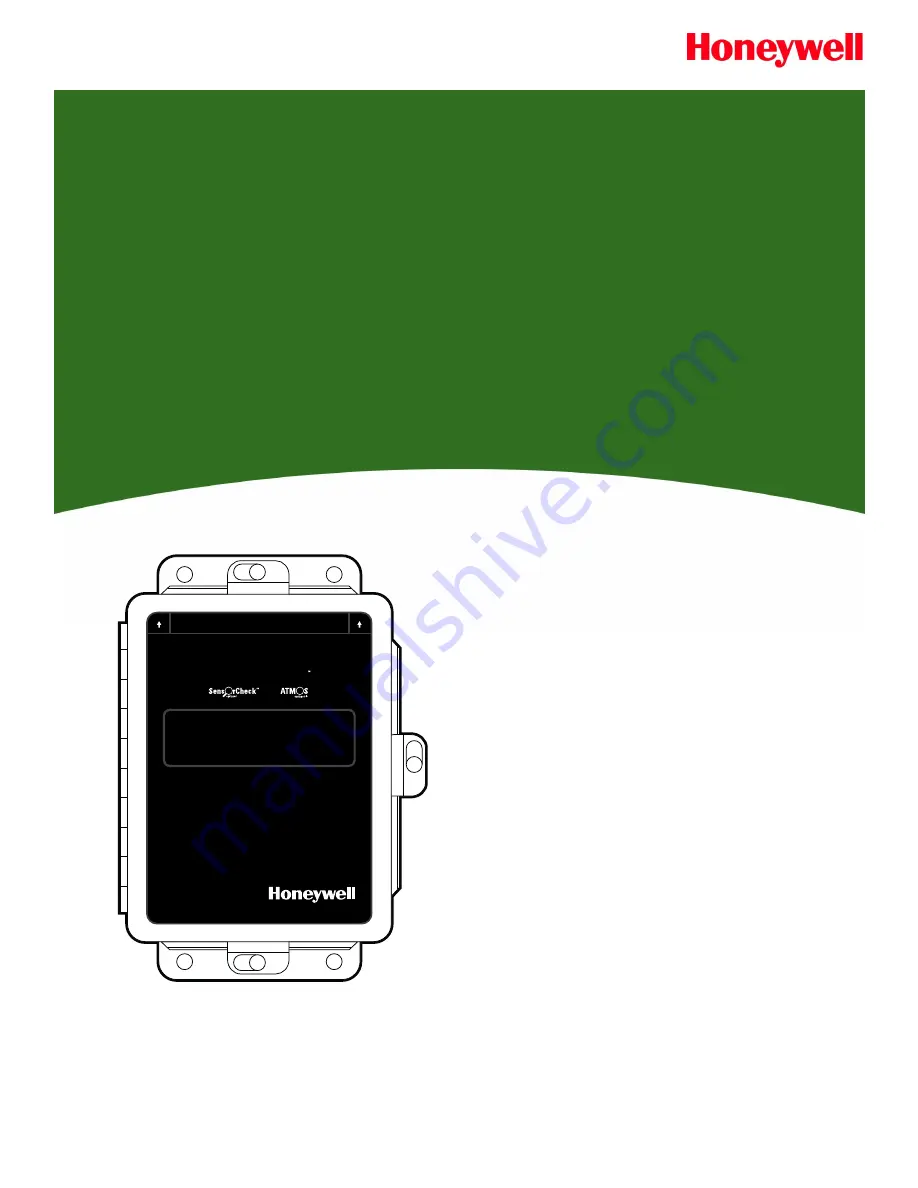
Manning AirScan-iR Refrigerant Sensor 19100 AirScan-iR-ind 05/2006 REVA Copyright © 2006 Manning Systems, Inc. All Rights Reserved. 1
AirScan
TM
i
R
Instruction and
Installation Manual
Rev A
Refrigerant Sensor for
Commercial Applications
Instruction and Installation Manual
Rev A
Manning
AirScan
TM
iR
Refrigerant Sensor for
Industrial Applications
Honeywell Analytics
11511 West 83
rd
Terrace
Lenexa, Kansas 66214
800.444.9935 or 913.894.1185
www.gasalarm.com
913.894.1296 fax
19100AirScan-iR-ind 5/2006 REVA
9138941296fax
19072 ECF9NH3 4/2006 REVE
Manning AirScan
MOUNT ENCLOSURE THIS END UP. DO NOT BLOCK PERFORATED VENT HOLES.