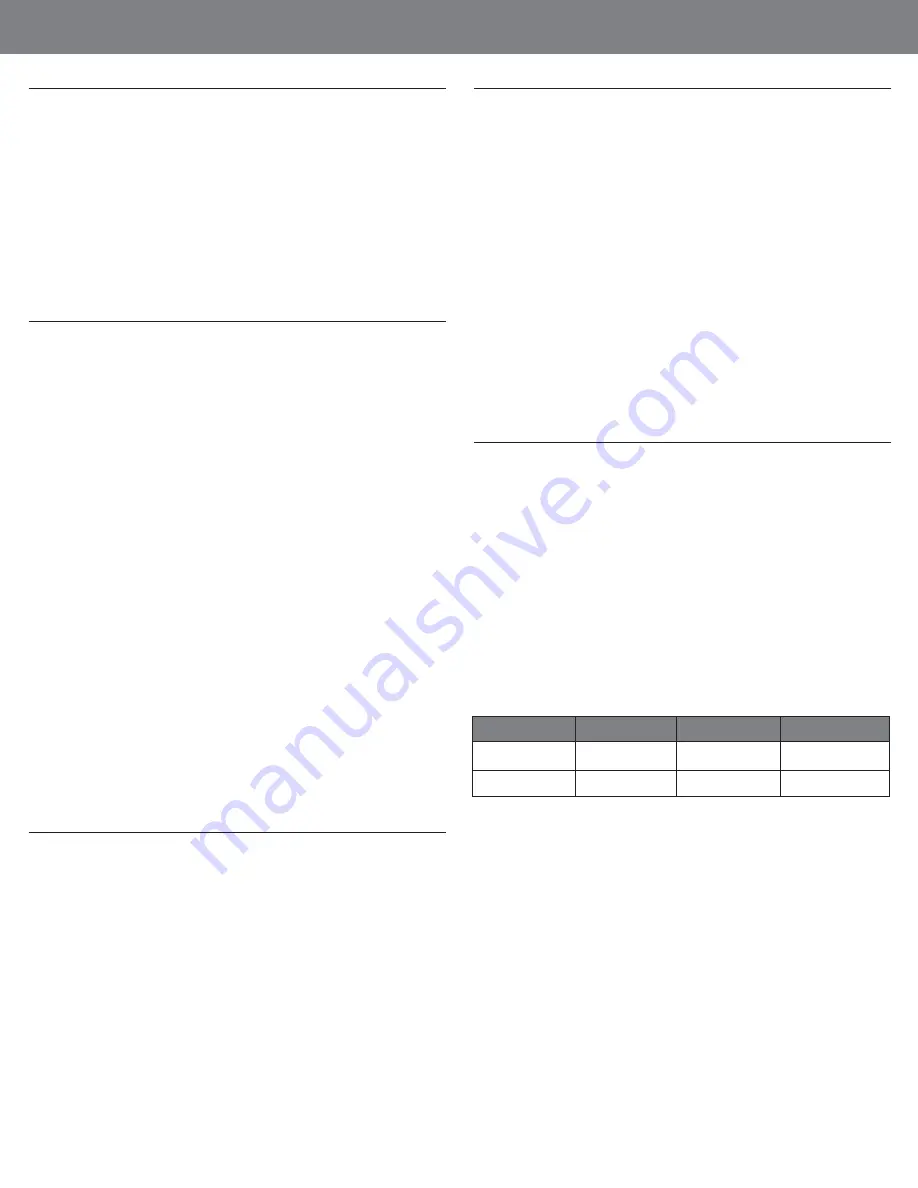
1.
Loosen the two 1˝ long Allen Cap screws from the NC housing cap.
2.
Remove the NC housing cap from over the piston.
3.
Remove the bias spring from the face of the NC piston.
4.
Remove the NC piston from the hole in the retaining nut.
5.
Remove the two .75˝ long Allen cap screws from the NO housing cap.
6.
Remove the NO housing cap and piston from the end of the body
assembly.
7.
Remove the NO piston from the bore of the NO housing cap.
8.
Remove diaphragm retaining nut.
9.
Remove the thrust plug from the cavity.
10. Remove the four diaphragms from the cavity.
11. Flip valve over and repeat steps 8 through 10.
DISASSEMBLY
1.
Place body assembly in vise or fixture with Normally Open side facing
up. The Normally Open side is the one without an o-Ring groove.
2.
Spread a small amount of Krytox® around the bore of the NO housing
cap.
3.
Remove the o-ring from the NO piston and replace with the same size
o-ring from the repair kit.
4.
Carefully insert the NO piston into the bore of the NO housing cap.
Push the piston all the way down in the bore.
5.
Place a small amount of Krytox® into the counter bored hole on the
edge of the housing. Remove the small o-ring from this counter bore
and replace with the same size o-ring from the repair kit.
6.
Place the NO housing cap and piston over the end of the body
assembly. Make sure the spring pin lines up with the small hole in the
housing and that the small o-ring does not fall out.
7.
Start the two .75˝ long Allen cap screws into the holes in the housing
by hand. Continue tightening until hand tight.
8.
Finish tightening the screws to 30-40 lb/in.
9.
Remove the body assembly from the fixture.
10. The next operation requires the use of an arbor press or similar device
11. Place the body assembly in the fixture.
ACTUATION ASSEMBLY
12. Remove the body o-ring, which is located in a groove on the outside
diameter of the body, and replace it with the equivalent size o-ring
from the repair kit.
13. Lubricate the hole on the NC diaphragm retaining nut with Krytox®.
14. Replace the “smaller˝ and “larger˝ size o-rings on the NC piston with
the equivalent size o-rings from the repair kit.
15. Insert the NC piston into the hole in the retaining nut.
16. Place the bias spring onto the face of the NC piston.
17. Spread a small amount of Krytox® around the bore of the NC housing
cap.
18. Carefully lower the housing cap over the piston.
19. Continue pushing down housing until it will go no further by hand.
20. Use the ram on the arbor press to continue pushing down the housing.
Make sure that the spring pin is lined up with the correct hole in the
housing.
21. Start the two 1˝ long Allen Cap screws into the holes in the housing by
hand. Continue tightening until hand tight.
22. Finish tightening the screws to 30-40 lb/in.
23. Remove the assembled DV-3 from the fixture.
ACTUATION ASSEMBLY (CONT’D)
1.
Securely clamp the valve body in a vise.
2.
Connect a source of pressure to the process inlet using suitable fittings.
3.
Connect a supply of low-pressure air to the actuation inlet using
suitable fittings.
4.
Connect quarter turn valves to the NC and NO outlets using suitable
fittings. Make sure the valves are in the closed position.
5.
Apply inlet pressure up to a value that is 110% of the rated pressure for
this unit.
6.
Open the quarter turn valve on the NC outlet port.
7.
Agitate the leak detecting fluid to form foam. Apply to the outlet of the
quarter turn valve. There should be no evidence of leakage.
8.
If no leakage is present, you may proceed to the next step.
9.
Briefly open and close the quarter turn valve on the NO outlet. There
should be ample flow coming from the valve.
10. Close the quarter turn valve on the NC outlet.
11. Apply pressure to the actuation port according to the following chart:
12. Open the quarter turn valve attached to the NO outlet.
13. Agitate the leak detecting fluid to form foam. Apply to the outlet of the
quarter turn valve. There should be no evidence of leakage.
14. If no leakage is present, you may proceed to the next step.
15. Briefly open and close the quarter turn valve on the NC outlet. There
should be ample flow coming from the valve.
16. Close the quarter turn valve on the NO outlet.
17. Put an adequate amount of leak detecting fluid, such as “Leak
Detective˝ or soapy water, around the 1/32˝ diameter inspection hole
on both housing caps.
18. There should be no evidence of leakage from either 1/32˝ diameter
inspection holes. Any leakage indicates that the o-rings are faulty and
should be replaced.
19. Remove all pressure from the valve and vent the remaining pressure.
20. Disconnect all lines to the valve and remove it from the vise or fixture.
PRESSURE TESTING
1.
Securely clamp the valve body in a vise or fixture with the Normally
Closed side facing up. The Normally Closed side is the side with the
o-ring
groove.
2.
Clean the diaphragm sealing surface with a cotton swab moistened with
alcohol.
3.
Correctly orient all four diaphragms and hold them in your hand. Clean
the bottom surface of the bottom diaphragm with a Q-Tip® moistened
with alcohol.
4.
Place the four diaphragms in the cavity, being careful to insure they
remain oriented correctly.
5.
Place the thrust plug in the cavity. Make sure the thrust plug is
correctly oriented. Use a small amount of Krytox® on the face of the
thrust plug to keep it centered on the diaphragms.
6.
Place a small amount of lubricant on the threads of the NC diaphragm
retaining nut and start it into the body. Continue tightening until hand
tight.
7.
Finish tightening the diaphragm retaining nut with a torque wrench to a
value of 35 lb/ft.
8.
Flip the body over in the fixture and repeat the above steps for
assembling the diaphragms, thrust plug and NO diaphragm retaining nut
on the other side.
9.
Connect a source of pressure to the inlet using suitable fittings.
10. Plug both NO and NC outlet ports using suitable pipe plugs.
11. Put an adequate amount of leak detecting fluid, such as “Leak
Detective˝ or soapy water, around the hexagonal portion of the
diaphragm retaining nut.
12. Apply 110% of maximum rated process pressure to the inlet.
13. There should be no evidence of leakage around the nut.
14. Flip body over and repeat procedure for the other side.
BODY ASSEMBLY & TEST
Single Piston
45 psiG
90 psiG
Not Available
Double Piston
25 psiG
50 psiG
75 psiG
0 - 250 Range
0 - 500 Range
0 - 800 Range
*NOTE: PLEASE REVIEW ILLUSTRATION BEFORE DISASSEMBLY AND REASSEMBLY OF VALVE.