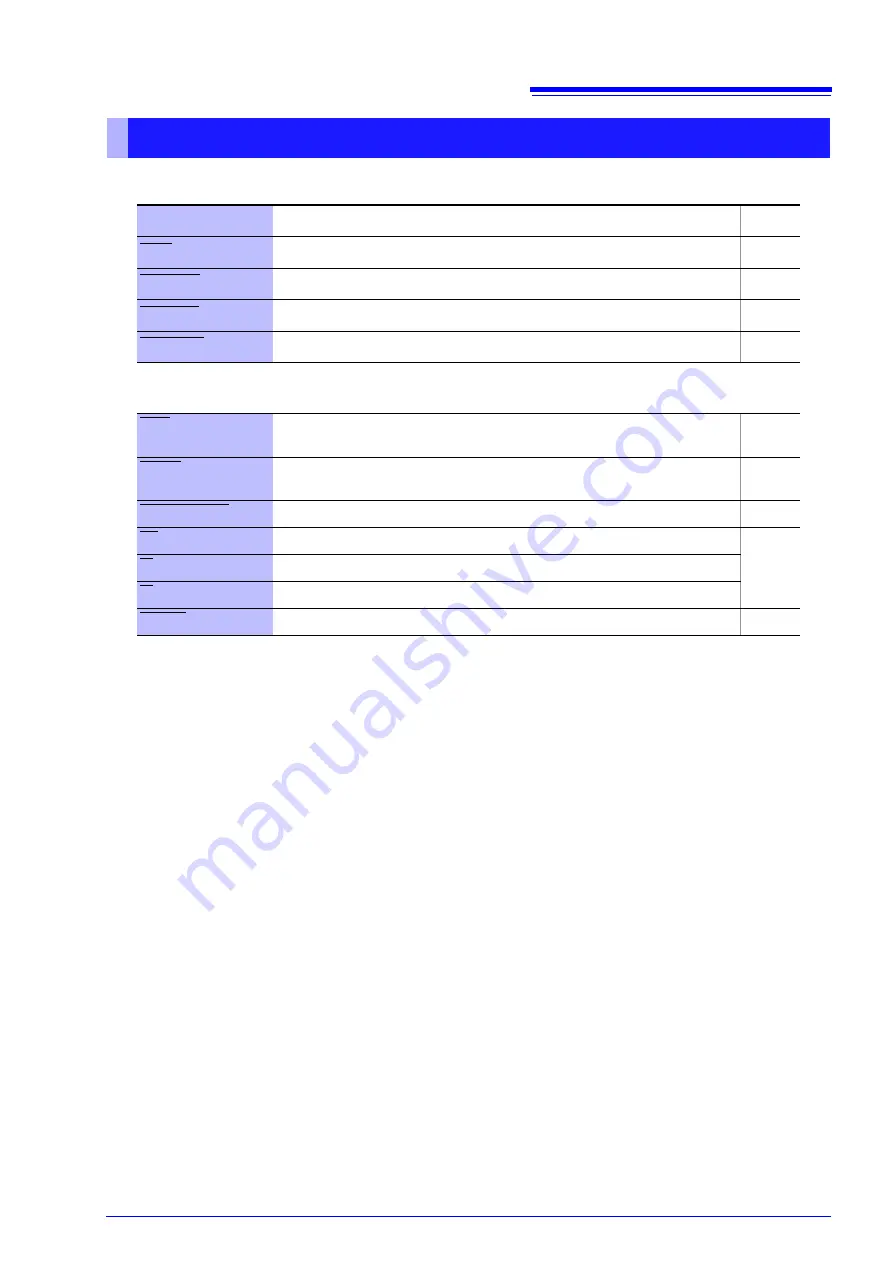
5.1 External Input/Output Connector and Signals
43
Input Signals
Output Signals
Signal Descriptions
EX24V)
External power source input
TRIG
External trigger input signal
C.CHECK
Contact check input signal
OPEN_IR
Fixture resistance open correction execution signal
OPEN_CX
Fixture capacitance open correction execution signal
EOM
This signal indicates the end of a measurement.
Output data is acquired when this signal changes to low.
INDEX
This signal indicates that A/D conversion in the measurement circuit is com-
plete. Sample switching is performed when this signal changes to low.
NO CONTACT
Contact check judgment results
LO
Comparative measurement results (LOW)
IN
Comparative measurement results (IN)
HI
Comparative measurement results (HIGH)
ALARM
Instrument malfunction
Summary of Contents for SM7810
Page 19: ...2 5 Turning the Power On and Off 16 ...
Page 51: ...5 3 Internal Circuitry 48 ...
Page 65: ...7 4 Cleaning 62 ...