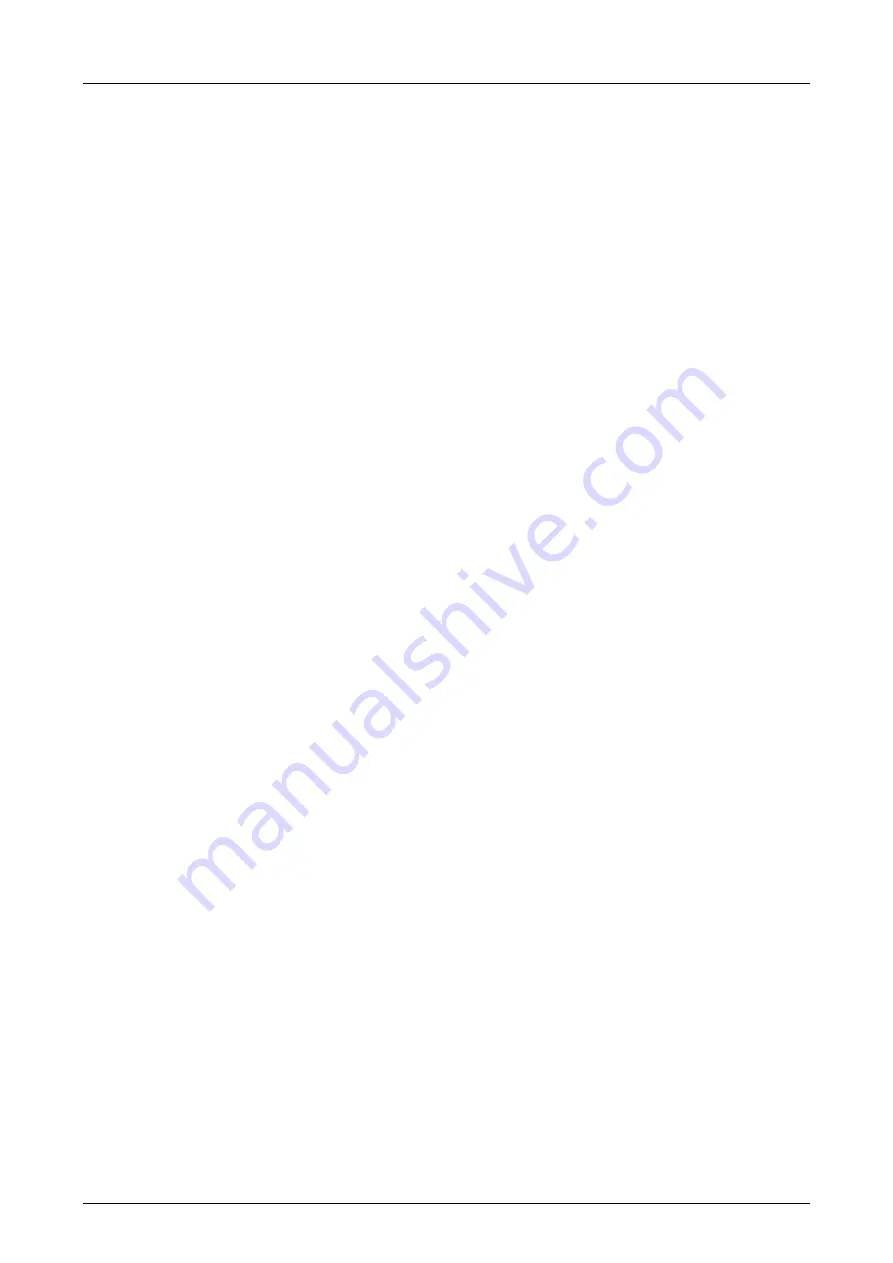
4 Start-up
X-MIO 7/6 01
Page 44 of 72
HI 801 305 E Rev. 5.00
4.5
Configuring the Overspeed Trip Module in SILworX
The module is configured in the Hardware Editor of the SILworX programming tool.
Observe the following points when configuring the module:
To diagnose the module and channels, both the system parameters and the measured value
can be evaluated within the user program. For more information on the system parameters,
refer to the tables starting with Chapter 4.5.1.
A global variable must be assigned to each input and output in use.
The supplies for the measured inputs are monitored for undervoltage.
If the
Supply used
parameter is activated, a supply error results in a channel fault (
Channel
OK
= FALSE). The values of faulty channels are not used for the 2oo3 evaluation, the
reactions described in Chapter 4.4.1 are prformed. If the supplies are not used, the
Supply
used
parameter must be deactivated. This ensures that a supply error does not lead to a
channel fault (
-> Channel OK =
TRUE). To diagnose the supply, evaluate the
Supply X OK
parameter in the user program. Refer to Table 32 for more details about the
Supply X OK
parameter.
The supplies for the digital inputs are monitored for undervoltage.
If the
Sup. used
parameter is activated, a supply error results in a channel fault (
Channel OK
= FALSE). The faulty channel is not used for the 2oo3 evaluation. If the supplies are not
used, the
Sup. used
parameter must be deactivated. This ensures that a supply error does
not lead to a channel fault (
-> Channel OK =
TRUE). To diagnose the supply, evaluate the
Supply X OK
parameter in the user program. Refer to Table 30 for more details about the
Supply X OK
parameter.
The supply for the measuring inputs is monitored for the permissible load current (SC/OC),
see Chapter 4.3.
To increase availability through module redundancy, a redundancy group created in SILworX
is always initially composed of two modules. Additionally, the redundancy group can be
extended with a third module as follows:
-
Right-click to open the context menu of the redundancy group. Select
Extend
Redundancy Group
and choose an available slot in the
Create Redundancy Group
dialog
box. Click
OK
to confirm. A third module is created.
The redundancy behavior of the modules must be defined through the user program.
The
Redundancy
tab specifies all the existing redundancy groups and the modules of which
they are composed.
The detail view for the redundancy group displays the configurable settings. These settings
apply for all modules within the redundancy group.
The detail view for the modules displays the parameters for the individual modules. Global
variables can be assigned to these parameters.