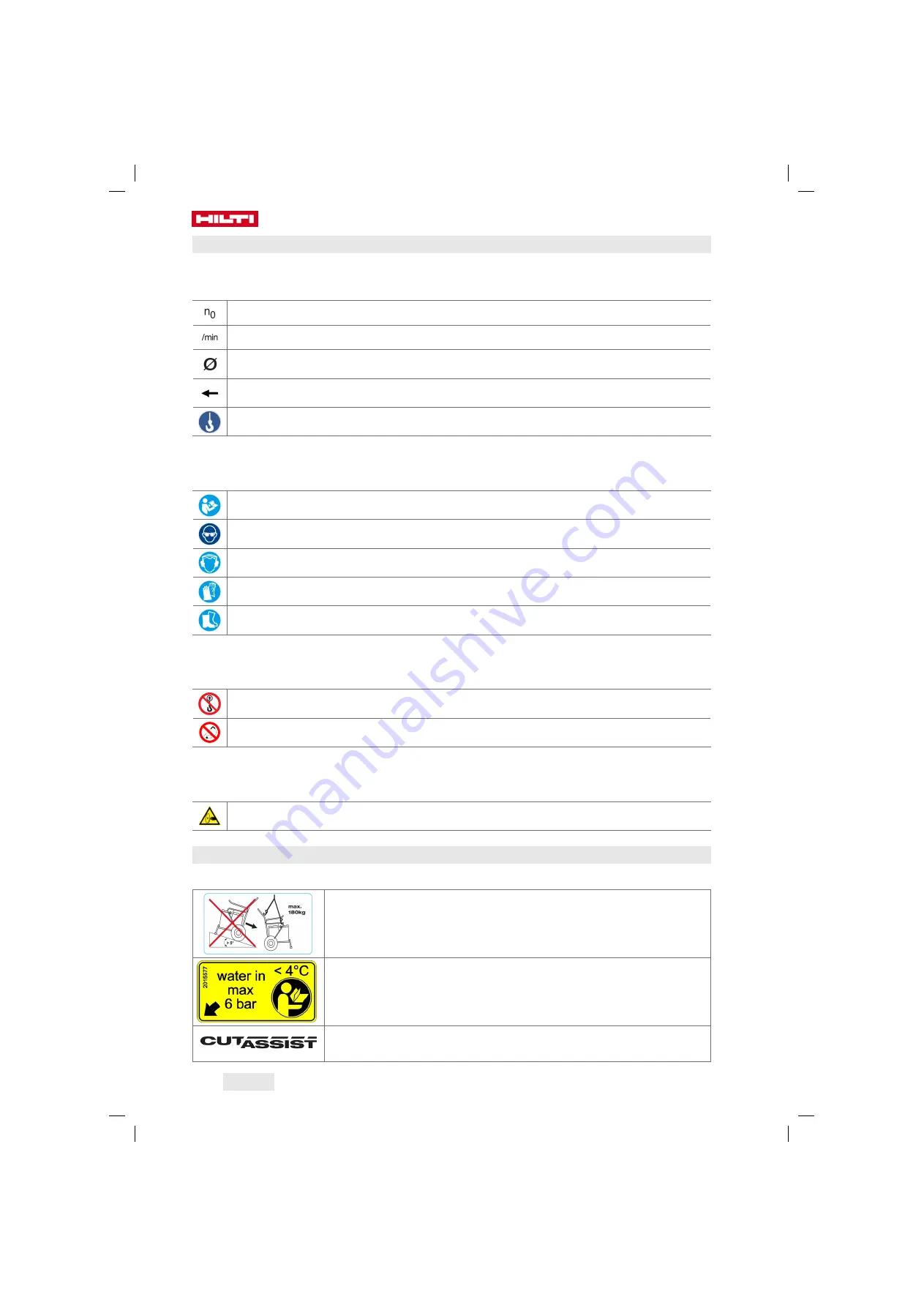
4
English
2328430
*2328430*
1.3 Product-dependent symbols
1.3.1 General symbols
The following symbols are used on the product:
Rated speed under no load
Revolutions per minute
Diameter
Saw blade direction of rotation (arrow on the blade guard holder)
Suspension point provided for lifting by crane
1.3.2 Obligation symbols
The following obligation symbols are used on the product:
Read the operating instructions
Wear eye protection
Wear ear protection
Wear protective gloves
Wear safety shoes
1.3.3 Prohibition symbols
The following prohibition symbols are used on the product:
Lifting by crane prohibited
Use of high-pressure cleaning equipment prohibited
1.3.4 Hazard symbols
The following hazard symbols are used on the product:
Warning: risk of cutting injury
1.4 Stickers
Stickers on the product
On the transport trolley
Using the transport trolley
On the saw head
Maximum water pressure and action to be taken in the event of
risk of frost
On the saw head
The machine is equipped with the
Cut Assist
function.
Summary of Contents for DST 20-CA
Page 1: ...DST 20 CA English...
Page 2: ......
Page 3: ...DST 20 CA Original operating instructions...
Page 4: ......
Page 52: ...Hilti registered trademark of Hilti Corp Schaan 20220523 2328430 2328430...