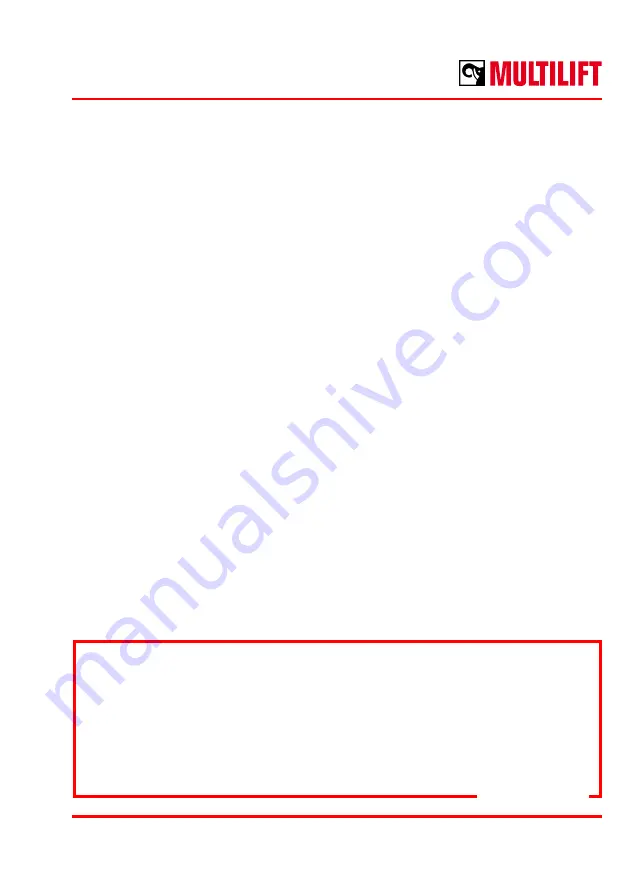
45
4/2018
Hooklift Multilift XR S
User Manual
113175421
XR14S/16S/18S/21S/26S/30S
Unloading a container
1.
See the safety instructions before unloading.
2.
Drive the truck to the place where the container has to be unloaded.
3.
Check the working area
- ensure that there is enough space in front, rear and above the truck.
4.
Engage the parking brake.
5.
Press the clutch pedal and engage the PTO.
6.
If the truck is equipped with any of the following equipment:
- retract the adjustable under-run bar (mechanical or manual hydraulic)
- deflate the air suspension
- activate the bogie blocking cylinders or stabilising roller.
7.
Open the hydraulic body locks
- press the “body lock” button
- “locks not closed” signal light is lit on the control unit when the locks are open.
Open the mechanical or hydraulic front locks (optional).
8.
Move the hook arm fully rearward position
- move the control lever to left and backward.
- start at idle speed and then increase the engine speed gradually.
NOTE! If there is a safety code CXXX and/or dXXX in the display,
then see the chapter ”Safety codes” after the chapter ”Unloading a container”.
The unloading will start in most cases but the reason to the code must be
checked and repaired as soon as possible to avoid any risk to injuries or
damages.
Safety codes >>>
Summary of Contents for Hooklift Multilift XR S Series
Page 157: ......