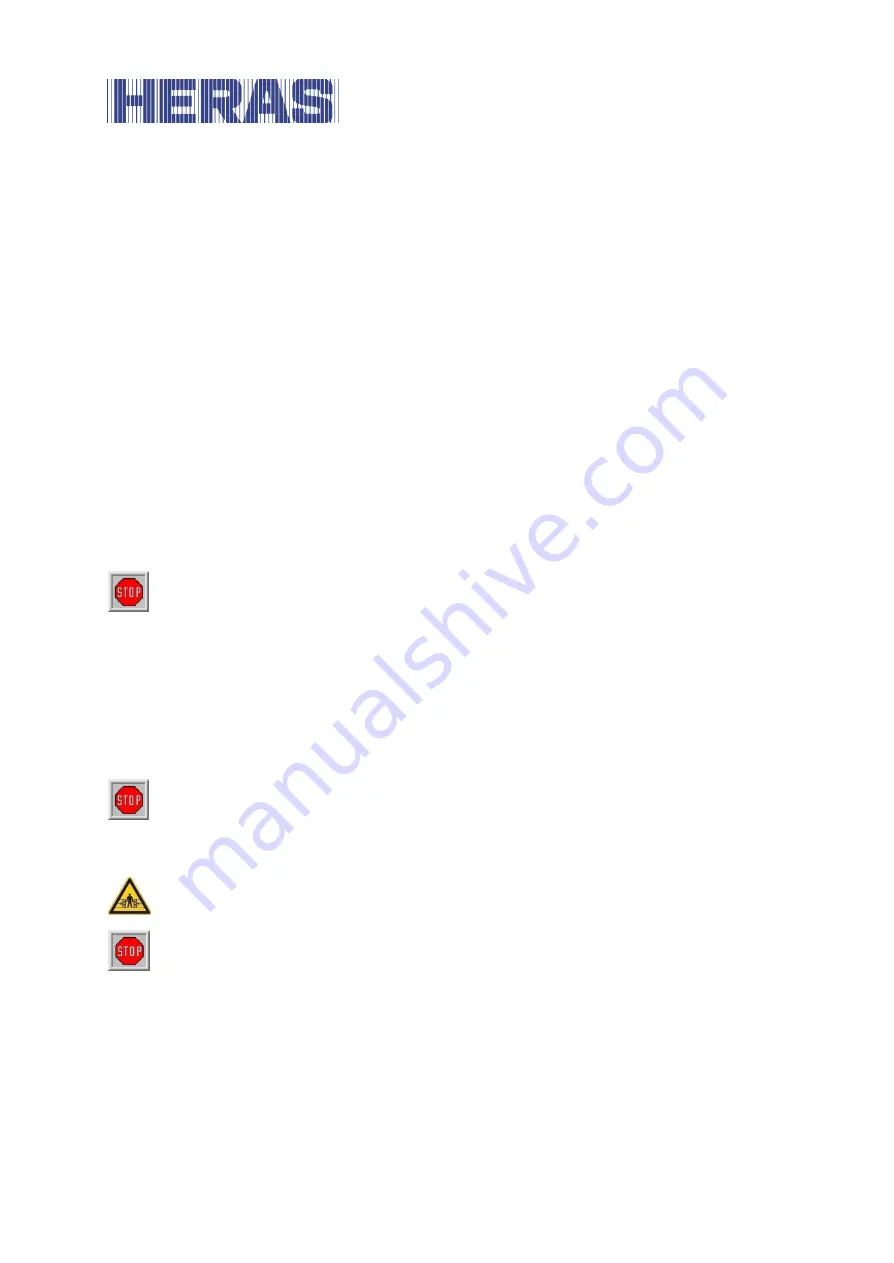
EN
– Translation of the original user manual - 2.0 | 2019
12
2.4
SAFETY PROVISIONS EMPLOYED
To protect people and goods from injury or damage, the gate is fitted with
safety provisions including safety edges and/or photocells.
These serve as emergency provisions that immediately stop and reverse the
movement of the gate. It is forbidden to use these provisions to stop the
gate normally.
For a gate with hold-to-run control, the above-mentioned safety provisions
are not necessary and will therefore not be standard provisions.
With this type of operation, the gate stops immediately as soon as the
switch is released.
2.5
INTENDED USE
The gate is intended to control access to a specific plot, premises or site. The gate
is intended for both industrial and private use.
The gate drive and control unit is adjusted to the options agreed with the
user. The relevant options are laid down during hand-over.
Carefully read this user manual before operating the gate. You must always be
familiar with the operating mode the gate is in.
2.6
SAFETY DURING USE
Children or people with a disability must not operate the gate. Parents must
supervise their children to prevent them playing with the gate.
PARENTS ARE RESPONSIBLE FOR THEIR CHILDREN
Keep a safe distance from the moving gate. Warning icons to this effect
have been installed in various locations
.
Only pass through the gate when it is completely open.
The gate must not be operated in windy conditions, wind force ≥9
Beaufort. The gate leaf can swing in a way that can result in damage to
the construction.
The safety edges serve as emergency facilities to immediately stop and
reverse the gate movement. Using them as a regular gate stop feature is
not allowed. Since the head stiles of the gate have safety edges that
cannot cover their full height, there is still some risk of people getting
trapped by the gate here.
Summary of Contents for HMD Basic
Page 2: ...EN Translation of the original user manual 2 0 2019 2...
Page 75: ...EN Translation of the original user manual 2 0 2019 75 Appendix A Declarations Dop DoC...
Page 76: ...EN Translation of the original user manual 2 0 2019 76...
Page 77: ...EN Translation of the original user manual 2 0 2019 77 Appendix B ELECTRIC DIAGRAM HMD24...
Page 78: ...EN Translation of the original user manual 2 0 2019 78...
Page 79: ...EN Translation of the original user manual 2 0 2019 79...
Page 80: ...EN Translation of the original user manual 2 0 2019 80...
Page 81: ...EN Translation of the original user manual 2 0 2019 81...
Page 82: ...EN Translation of the original user manual 2 0 2019 82...
Page 83: ...EN Translation of the original user manual 2 0 2019 83...
Page 84: ...EN Translation of the original user manual 2 0 2019 84...
Page 85: ...EN Translation of the original user manual 2 0 2019 85...
Page 86: ...EN Translation of the original user manual 2 0 2019 86...
Page 87: ...EN Translation of the original user manual 2 0 2019 87...
Page 88: ...Local supplier stamp Lokal terf rs ljare st mpel...