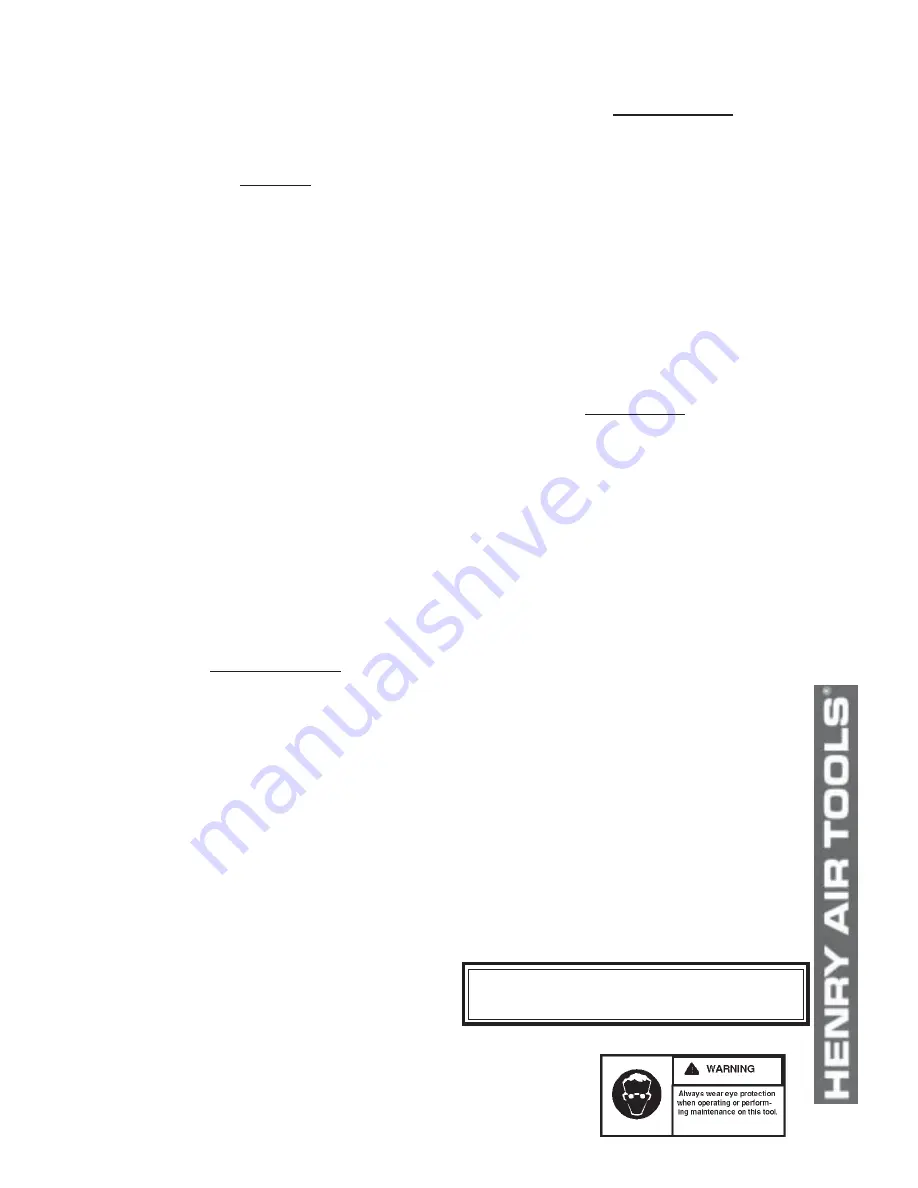
Updated 1/30/2004
7 4
13. Remove screw (591028) . Remove snap ring (404-8) .Support bearing
(404-7) and press spindle through with 1/4" punch. This will remove spacer
(404-12), gear (404-10) and bearing(404-7). 15. Remove key (404-4).
ASSEMBLY
Support front bearing(400-G-11) on drill block. Press spindle(404-14)through
bearing until it bottoms on shoulder.
2.Slide front thrust(400-7)over the spindle and onto front bearing. Place
key(400-10) into keyway in spindle. Slide rotor down over shaft. 3. Grasp rotor
in vise snugly and replace pinion gear(404-10) and wrench firmly. 4. Support
bearing and pinion gear in downward position. Place five blades(400-6) in slots.
Slip cylinder(400-2-G) over rotor. Install rear thrust(404-19) locating cylinder
pin in small hole of rear thrust plate (404-19). 5. Place bearing (404-9) in rear
thrust and tap into place with suitable bearing driver. Using pliers place snap
ring(592016) in spindle groove of (404-19).[
(May be a snap ring in (404-19)]
6.Support bearing(404-7) on inner race. Press spindle (404-5) through bearing
until it bottoms on shoulder. 7. Install key (404-4) and line up with keyway of ring
gear(404-10). Support gear on inner diameter and press spindle through. Slide
spacer(404-12) on spindle. Replace snap ring (404-8) on spindle groove. 8.
Support threaded end of spindle and press on bearing(404-3). Tighten screw
(591028) into end of spindle. Press spindle assembly into cap(404-2) Grease
gear. 9. Install spring washers(404-6) into angle head(404-1). 10. Install spindle
assembly into angle head housing, secure in vise and tighten cap (404-2).
11. Re-Locate angle head in vise-so that the motor can be installed vertically.
12.Replace shim(404-20) exactly as it was originally installed. 13. Jiggle greased
pinion assembly into angle head while turning spindle(404-5)-so that gears
mesh. Tap lightly on rear of motor to insure that is fully seated. 14. Install
exhaust deflector (410-G-17-S). Place O-ring(400-51) on motor case(402-132)
and screw onto angle head. The deflector should be snug, but can be turned.
Place a few drops of oil into motor inlet.
15. To check throttle valve, unscrew plug(869311) and lift out spring and valve.
Replace O-ring if worn.
16. Replace guard on tool.
1
7. CHECK RPM WITH TACHOMETER.TOOL MUST RUN AT
OR BELOW SPEED THAT IS STAMPED ON TOOL.
MODELS
4401 RA
4401 RAC
4401 RAS
4401 RASC
4401 RAK
4401 RASK
SERVICE INSTRUCTIONS
This tool is designed to operate on 90 psig (6.2 bar)
maximum air pressure with 1/4" (8 mm) hose. Do not use
a grinder without recommended wheel guard. Do not
use any wheel for which the operating speed listed is
lower than the actual free speed of the Grinder.
SAFETY
1.Before operation check spindle speed with a tachometer. If the RPM exceeds the
rated speed stamped on tool, servicing is required. 2. Inspect grinding wheels for
bends, chips, nicks, cracks or severe wear. If the wheel has any of these, or has been
soaked in liquids do not use. On brushes check for loose wires that may fly off in
operation. 3. Start new grinding wheels under a steel bench. Run at full throttle for
one minute.Defective wheels usually come apart immediately.When starting a cold
wheel apply to work slowly, allow wheel to warm gradually.
4. Model 4401RAC
grinders equipped with collets are intended for mounted
wheels,points and carbide burrs. They are not guarded
for type 1 wheels. If you have a type 1 wheel
application,please purchase a guard (4504,4505,etc.)
5.The
Model 4401RA Grinders are equipped with a guard from the manufacturer. A guard is
not needed for :a.) mounted wheels two inches (50 mm) or smaller; b.) grinders used
for internal work, while within the work being ground. 6. At least one-half of the
mandrel length (i.e. mounted wheel, burr, etc.) must be inserted into the collet.
Secure collet chuck tightly. 7.Safety levers are available from the manufacturer.(402-
26). 8. Before mounting or removing a wheel, disconnect grinder from air supply.
The wheel should fir properly on arbor, do not use bushings or wheel flanges to
adapt a wheel to any arbor unless recommended by the manufacturer. (Wheel
flanges should be at least 1/3 the diameter of the grinding wheel.) 9. Wear safety
goggles and other protective clothing. Continuous exposure to vibration may cause
injury to your hands and arms.(See regulations.) 10. Properly maintained air tools are
less likely to fail or cause accidents. If tool produces an unusual sound or vibrations
repair immediately.
DISASSEMBLY
PLEASE NOTE: The brass spacers that were installed by
the factory are necessary for this tool to operate effi-
ciently. When disassembling this tool examine how
spacers are arranged. They must be installed exactly the
same way. Failure to do this will cause improper gear
spacing, which causes pre-mature tool failure.
1.Disconnect air & remove all wheels and accessories. 2. Secure anglehead in vise on
dead handle boss. Unscrew and remove case(402-132)
Never squeeze
anglehead in vise.
This will distort bearings and ruin gear alignment. 3.
Remove deflector (410-G-17-S).
4. Pull motor from right angle head. Be careful to note location of shims. 5. Remove
snap ring (404-39),wafer(404-38),O-ring(594016), and snap ring (592016).(Some of
these may not be present).
6. Install brass or aluminum jaws in vise. Grasp the O.D. of cylinder(400-2-G)and end
plate(404-19). Using a 3/16" punch, tap spindle out rear bearing (404-9)
7.Remove cylinder, blades(400-6). 8. With rotor (400-5) still on spindle (404-14),
grasp the rotor in vise snugly and remove pinion gear(404-10).
8. Remove rotor(400-5) Remove key and front thrust plate(400-7). 9. Press bearing
(400-G-11) off of spindle.
10. Secure angle head in vise and unscrew cap (404-2). 11. Remove from vise and tap
on spindle with a plastic hammer The spindle assembly and spring washers (404-6)
will slide out.