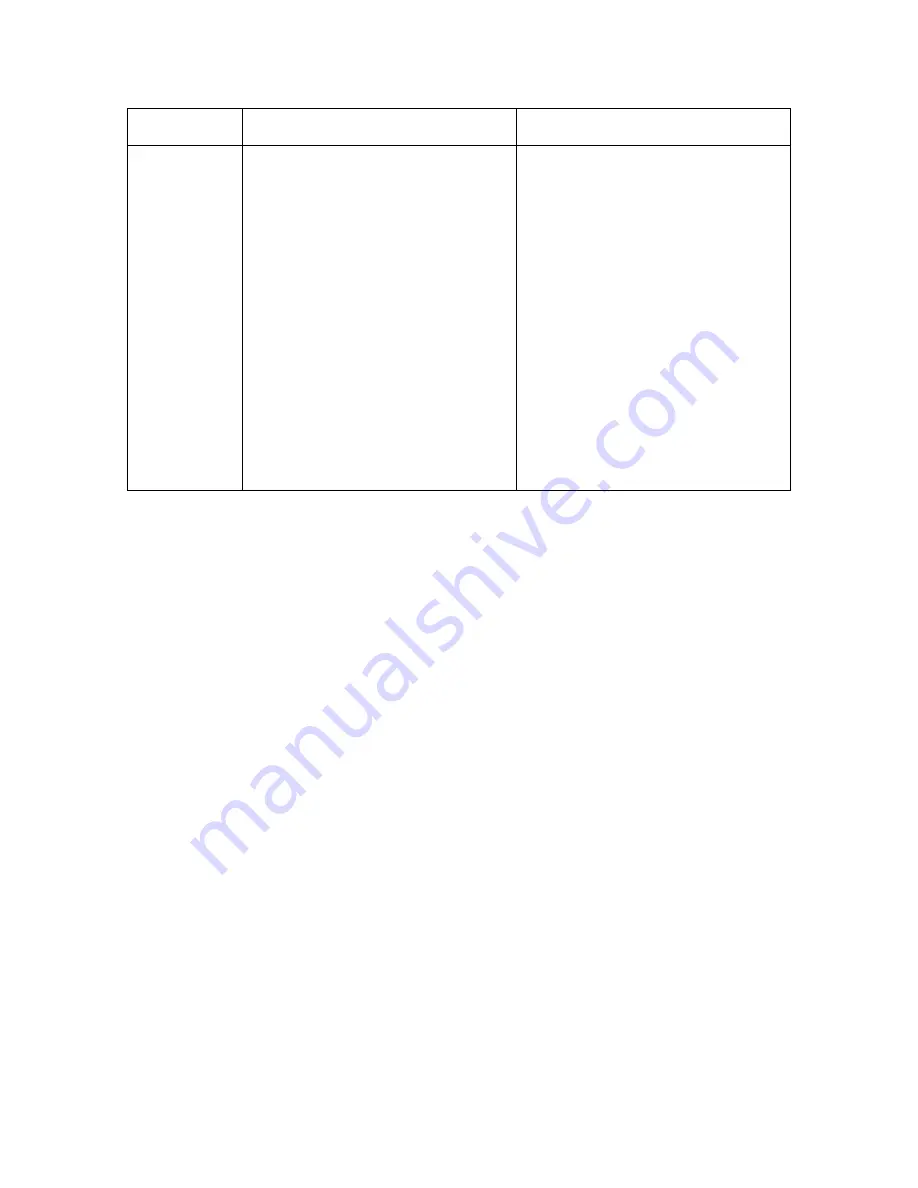
121
YX-ring seal and O-ring seal in the pilot
sleeve.
Heavy Steering
1) Insufficient oil supply of oil pump,
the slow-steering hand wheel feels
relatively light and the fast-steering
hand wheel heavy.
2) Air in the steering system, foam in
oil, making irregular noise, the hand
wheel can rotate while the oil cylinder
can not keep continuous motion.
3) Failure of the steel ball one-way
valve in the valve body, both the fast and
slow steering hand wheels are heavy,
also no pressure at steering.
4) Pressure of the overflow valve is
lower than working pressure or the
overflow valve is blocked by dirty stuff,
light steering in case of light or no load,
heavy steering when adding load.
5) Excessive viscosity of the oil liquid
1) Select appropriate oil pump or check
to see if the oil pump is normal.
2) Discharge air in the system and check
the oil suction pipe-work.
3) Check if the steel ball exists and if
there is dirty stuff blocking the steel
balls.
4) Adjust pressure of the overflow valve
or clean it.
5) Use oil liquid with recommend-
ded viscosity.
6. Lifting System
6.1 General Description
The lifting system is of the two-stage roller type with veritical up and down. It
consists of the inner mast, the outer mast and the lift bracket.
6.2 Inner and Outer Masts
The inner and outer masts both are welded parts. The bottom of outer mast is
connected with the drive axle and the weight mainly support on the axle housing. The
outside middle of outer mast is connected with the frame by tilt cylinders. The mast
assembly can be tilted forward and backward by operating tilt cylinders. The outer mast
has C-shaped cross section. The outer mast fixed with main rollers and side rollers on the
top of it. And the inner mast has L-shaped cross section. It fixed with main rollers at the
bottom of it. The main rollers bear both radial force and lateral force by adjusting it’s
clearance. The inner mast moves up and down smoothly with the main and side rollers
rolling.
Summary of Contents for CPD10
Page 1: ......
Page 8: ...5 ...
Page 9: ...6 Ⅱ Main Specifications of Forklift Truck Enternal view of forklift trucks ...
Page 20: ...17 Fig 1 4 Gearbox axle assembly 1 1 8t 2t 2 5t Figure 1 5 reducer and differential 3 3 5t ...
Page 46: ...43 Fig 4 1 Circuit diagrams of electric system CPD10 18 GC1Li ...
Page 47: ...44 Fig 4 2 Circuit diagrams of electric system CPD10 18 GD1Li ...
Page 48: ...45 Figure 4 3 Circuit diagrams of electric system CPD10 18 GD3Li ...
Page 49: ...46 Fig 4 4 Circuit diagrams of electric system CPD20 25 GC1Li ...
Page 50: ...47 Fig 4 5 Circuit diagrams of electric system CPD20 25 GD1Li ...
Page 51: ...48 Figure 4 6 Circuit diagrams of electric system CPD20 25 GD3Li ...
Page 52: ...49 Fig 4 7 Circuit diagrams of electric system CPD30 35 GC1Li ...
Page 53: ...50 Fig 4 8 Circuit diagrams of electric system CPD30 35 GD1Li ...
Page 54: ...51 Figure 4 9 Circuit diagrams of electric system CPD30 35 GD3Li ...
Page 55: ...52 Figure 4 10 Circuit diagrams of electric system CPD30 35 GB7Li ...
Page 56: ...53 Figure 4 11 Circuit diagrams of electric system CPD30 35 GB3Li ...
Page 68: ...65 4 3 2 CURTIS control device Fig 4 21 The controller of CPD10 18 GC1Li ...
Page 69: ...66 Fig 4 22 The controller of CPD10 18 GD1Li ...
Page 70: ...67 Fig 4 23 The controller of CPD10 18 G31Li ...
Page 71: ...68 Fig 4 24 The controller of CPD20 25 GC1Li ...
Page 72: ...69 Fig 4 25 The controller of CPD20 25 GD1Li ...
Page 73: ...70 Fig 4 26 The controller of CPD20 25 GD3Li ...
Page 74: ...71 Fig 4 27 The controller of CPD30 35 GC1Li ...
Page 75: ...72 Fig 4 28 The controller of CPD30 35 GD1Li ...
Page 76: ...73 Fig 4 29 The controller of CPD30 35 GD3Li ...
Page 77: ...74 Fig 4 30 The controller of CPD30 35 GB7Li ...
Page 78: ...75 Fig 4 31 The controller of CPD30 35 GB3Li ...
Page 131: ......