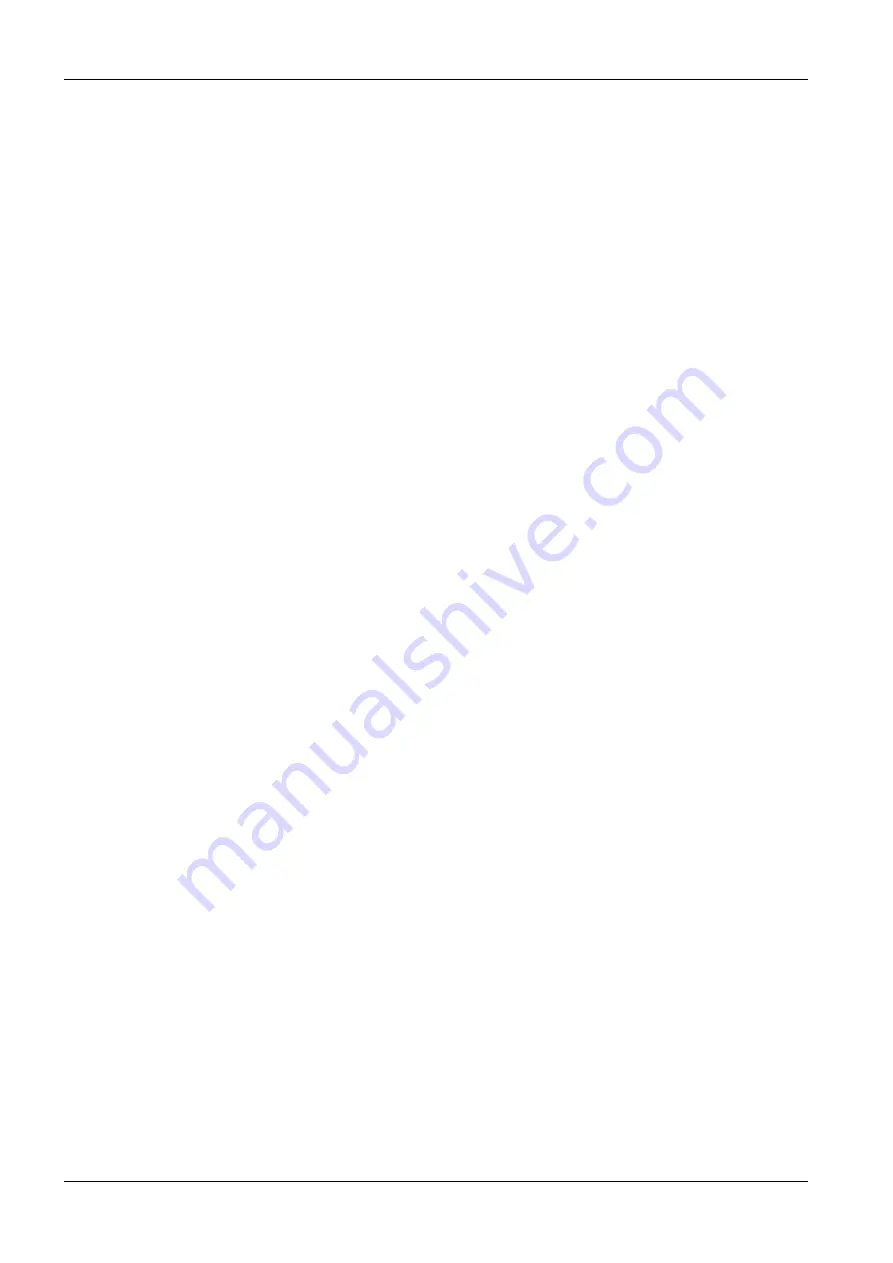
54
Patch Pipettes
9.3
Coating
The capacitance between the pipette interior and the bath, and also the noise from dielectric loss in the glass, can
be reduced by coating the pipette with an insulating agent such as Sylgard
(Dow Corning Corp., Midland, MI,
U.S.A.). Sylgard
is pre-cured by mixing the resin and catalyst oil and allowing it to sit at room temperature for
several hours (or in an oven at 50
◦
C for 20 min) until it begins to thicken. It can then be stored at -18
◦
C for
many weeks until use. The Sylgard
is applied around the lower few mm of the electrode to within 10
−
20
µm
of
the tip and then rapidly cured by a hot-air jet or coil. Coating should be done before the final heat-polishing of
the pipette, so that the heat can evaporate or burn off any residue left from the coating process.
9.4
Heat Polishing
Heat polishing is used to smooth the edges of the pipette tip and remove any contaminants left on the tip from
coating. It is done in a microforge or similar setup in which the pipette tip can be observed at a magnification
of 400-800x. The heat source is typically a platinum or platinum-iridium wire; to avoid metal evaporation onto
the pipette, the filament is coated with glass at the point where the pipette will approach it. To produce a steep
temperature gradient near the filament (which helps make the pipette tip sharply convergent), an airstream can
be directed at the filament. The amount of current to pass through the filament must be determined empirically
for each type of glass, but a good place to start is with sufficient current to get the filament barely glowing. The
typical practice is to turn on the filament current and move the filament toward the pipette (which, being stationary,
should remain in focus). Since the opening in the pipette tip is usually at the limit of resolution of viewing, you
might not see the change in shape at the tip, but instead only a darkening of the tip. You can tell whether you
have melted the tip closed, and also get an idea of the tip diameter, by blowing air bubbles in methanol with air
pressure supplied by a small syringe.
9.5
Use of Pipettes
Pipettes should be used within 2-3 hours after fabrication, even if stored in a covered container; small dust particles
from the air stick readily to the glass and can prevent sealing. However, with some easy-sealing cells we have made
the experience that pipettes may even be used the next day. It is very important to filter the filling solutions (e.g.,
using a 0
.
2
µm
syringe filter). Pipettes can be filled by sucking up a small amount of solution through the tip.
This can be done by capillary force (simply dipping the tip for a few seconds in a beaker containing the pipette
solution), or by applying negative pressure at the back of the pipette (e.g., using a 5 ml syringe). Thereafter, the
pipette is back-filled; the pipette should only be partially filled, just far enough to make reasonable contact with the
electrode wire (the pipette holder is not filled with solution, but is left dry). Overfilling the pipette has disastrous
consequences for background noise because the solution can spill into the holder, wetting its internal surfaces with
films that introduce thermal noise. Bubbles left in the pipette from filling can be removed by tapping the side of
the pipette.
For low noise recording, the electrode holder should be cleaned before each experiment with a methanol flush,
followed by drying with a nitrogen jet. Before you insert a pipette into the holder, it is a good idea to touch a hand
to a metal surface of the setup to discharge any static electricity that you may have picked up. Be sure to tighten
the holder firmly enough that the pipette does not move (on a scale of 1
µm
) when you give suction. Then, when
you change pipettes during an experiment, check the noise level of the empty holder using the
Noise
test function.
If it increases, solution has probably spilled inside the holder; in this case the holder should be cleaned again and
dried thoroughly.
http://www.heka.com
Summary of Contents for EPC 10 USB
Page 1: ...Hardware Manual Version 2 8 EPC 10 USB Computer controlled Patch Clamp Amplifier...
Page 6: ......
Page 10: ...4 Introduction http www heka com...
Page 16: ...10 Description of the Hardware http www heka com...
Page 22: ...16 Installation http www heka com...
Page 32: ...26 Verifying and Testing the EPC 10 USB http www heka com...
Page 44: ...38 The control software http www heka com...
Page 48: ...42 Operating Modes http www heka com...
Page 54: ...48 Compensation Procedures http www heka com...
Page 58: ...52 Patch Clamp Setup http www heka com...
Page 64: ...58 Using the Patch Clamp http www heka com...
Page 74: ...68 Appendix II Probe Adapters http www heka com...
Page 76: ...70 Appendix III S Probe http www heka com...
Page 81: ......