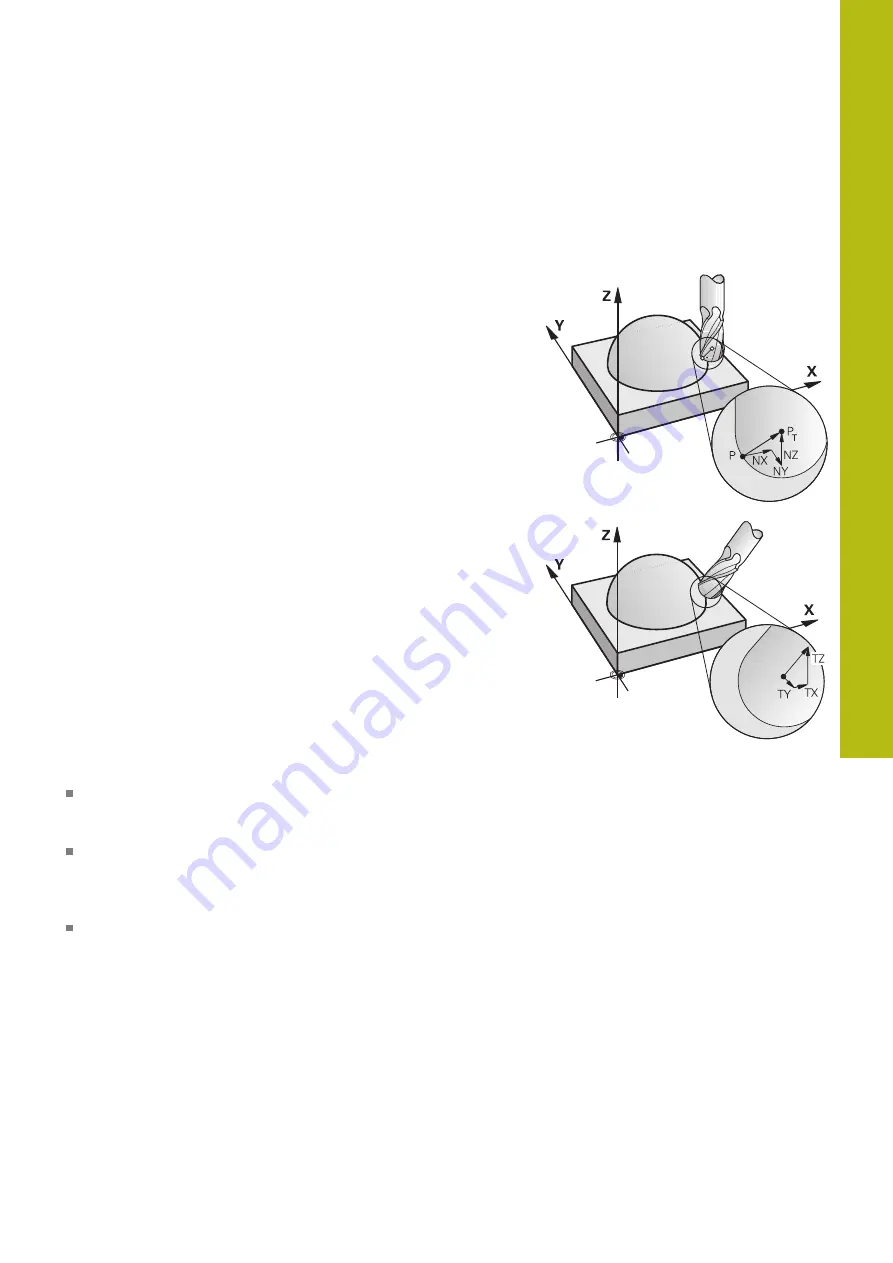
Multiple-Axis Machining | Three-dimensional tool compensation (option 9)
13
HEIDENHAIN | TNC 640 | Conversational Programming User's Manual | 10/2017
631
13.6 Three-dimensional tool compensation
(option 9)
Introduction
The control can perform a three-dimensional tool compensation
(3-D compensation) for straight line blocks. Apart from the X, Y
and Z coordinates of the straight-line end point, these blocks must
also contain the components NX, NY and NZ of the surface-normal
vector.
"Definition of a normalized vector",
If you want to carry out a tool orientation, these blocks also require
a normalized vector with the components TX, TY and TZ that
determines the tool orientation,
"Definition of a normalized vector",
The straight-line end point, the components for the surface normals
as well as those for the tool orientation must be calculated by a
CAM system.
Possible applications
Use of tools with dimensions that do not correspond with the
dimensions calculated by the CAM system (3-D compensation
without definition of the tool orientation).
Face milling: compensation of the cutter geometry in the
direction of the surface-normal vector (3-D compensation with
and without definition of the tool orientation). Cutting is usually
with the end face of the tool.
Peripheral milling: compensation of the cutter radius
perpendicular to the direction of movement and perpendicular to
the tool direction (3D radius compensation with definition of the
tool orientation). Cutting is usually with the lateral surface of the
tool.
Summary of Contents for TNC 640
Page 4: ......
Page 5: ...Fundamentals ...
Page 36: ...Contents 36 HEIDENHAIN TNC 640 Conversational Programming User s Manual 10 2017 ...
Page 67: ...1 First Steps with the TNC 640 ...
Page 90: ......
Page 91: ...2 Introduction ...
Page 130: ......
Page 131: ...3 Operating the Touchscreen ...
Page 144: ......
Page 145: ...4 Fundamentals File Management ...
Page 206: ......
Page 207: ...5 Programming Aids ...
Page 236: ......
Page 237: ...6 Tools ...
Page 281: ...7 Programming Contours ...
Page 333: ...8 Data Transfer from CAD Files ...
Page 355: ...9 Subprograms and Program Section Repeats ...
Page 374: ......
Page 375: ...10 Programming Q Parameters ...
Page 478: ......
Page 479: ...11 Miscellaneous Functions ...
Page 501: ...12 Special Functions ...
Page 584: ......
Page 585: ...13 Multiple Axis Machining ...
Page 650: ......
Page 651: ...14 Pallet Management ...
Page 664: ......
Page 665: ...15 Batch Process Manager ...
Page 673: ...16 Turning ...
Page 713: ...17 Manual Operation and Setup ...
Page 797: ...18 Positioning with Manual Data Input ...
Page 803: ...19 Test Run and Program Run ...
Page 843: ...20 MOD Functions ...
Page 881: ...21 Tables and Overviews ...