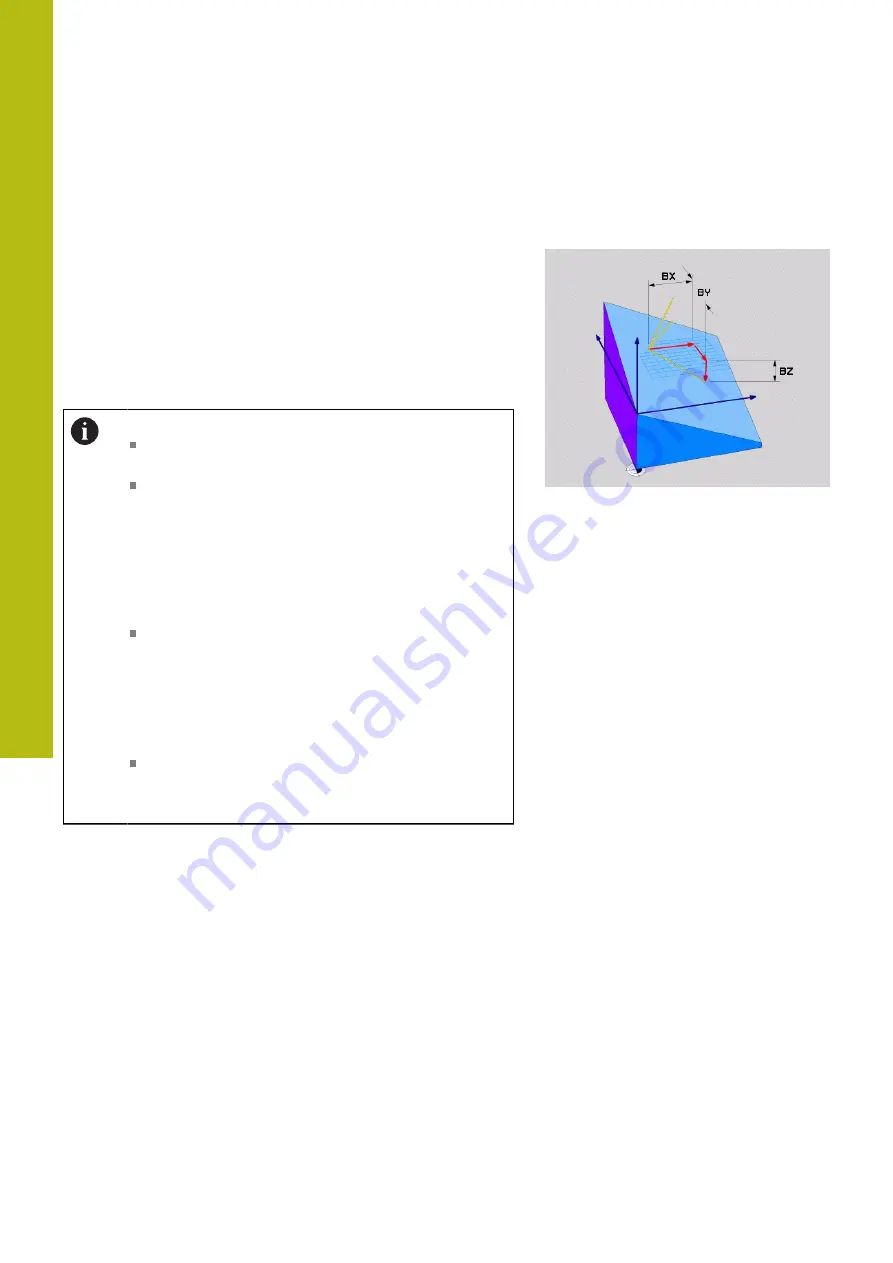
Multiple-Axis Machining | The PLANE function: Tilting the working plane (option 8)
13
598
HEIDENHAIN | TNC 640 | Conversational Programming User's Manual | 10/2017
Defining the working plane with two vectors:
PLANE VECTOR
Application
You can use the definition of a working plane via
two vectors
if
your CAD system can calculate the base vector and normal vector
of the tilted machining plane. A normalized input is not necessary.
The control internally calculates the normal, so you can enter
values between -9.999999 and +9.999999.
The base vector required for the definition of the machining plane
is defined by the components
BX,
BY
and
BZ.
The normal vector is
defined by the components
NX
,
NY
and
NZ
.
Programming notes:
The control calculates standardized vectors from the
values you enter.
The normal vector defines the slope and the
orientation of the working plane. The base vector
defines the orientation of the main axis X in the
defined working plane. To ensure that the definition
of the working plane is unambiguous, you must
program the vectors perpendicular to each other.
The machine tool builder defines how the control will
behave for vectors that are not perpendicular.
The programmed normal vector must not be too
short, e.g. all directional components having a length
of 0 or 0.0000001. In this case, the control would not
be able to determine the slope. Machining is aborted
and an error message is displayed. This behavior
is independent of the configuration of the machine
parameters.
You can select the desired positioning behavior.
Summary of Contents for TNC 640
Page 4: ......
Page 5: ...Fundamentals ...
Page 36: ...Contents 36 HEIDENHAIN TNC 640 Conversational Programming User s Manual 10 2017 ...
Page 67: ...1 First Steps with the TNC 640 ...
Page 90: ......
Page 91: ...2 Introduction ...
Page 130: ......
Page 131: ...3 Operating the Touchscreen ...
Page 144: ......
Page 145: ...4 Fundamentals File Management ...
Page 206: ......
Page 207: ...5 Programming Aids ...
Page 236: ......
Page 237: ...6 Tools ...
Page 281: ...7 Programming Contours ...
Page 333: ...8 Data Transfer from CAD Files ...
Page 355: ...9 Subprograms and Program Section Repeats ...
Page 374: ......
Page 375: ...10 Programming Q Parameters ...
Page 478: ......
Page 479: ...11 Miscellaneous Functions ...
Page 501: ...12 Special Functions ...
Page 584: ......
Page 585: ...13 Multiple Axis Machining ...
Page 650: ......
Page 651: ...14 Pallet Management ...
Page 664: ......
Page 665: ...15 Batch Process Manager ...
Page 673: ...16 Turning ...
Page 713: ...17 Manual Operation and Setup ...
Page 797: ...18 Positioning with Manual Data Input ...
Page 803: ...19 Test Run and Program Run ...
Page 843: ...20 MOD Functions ...
Page 881: ...21 Tables and Overviews ...