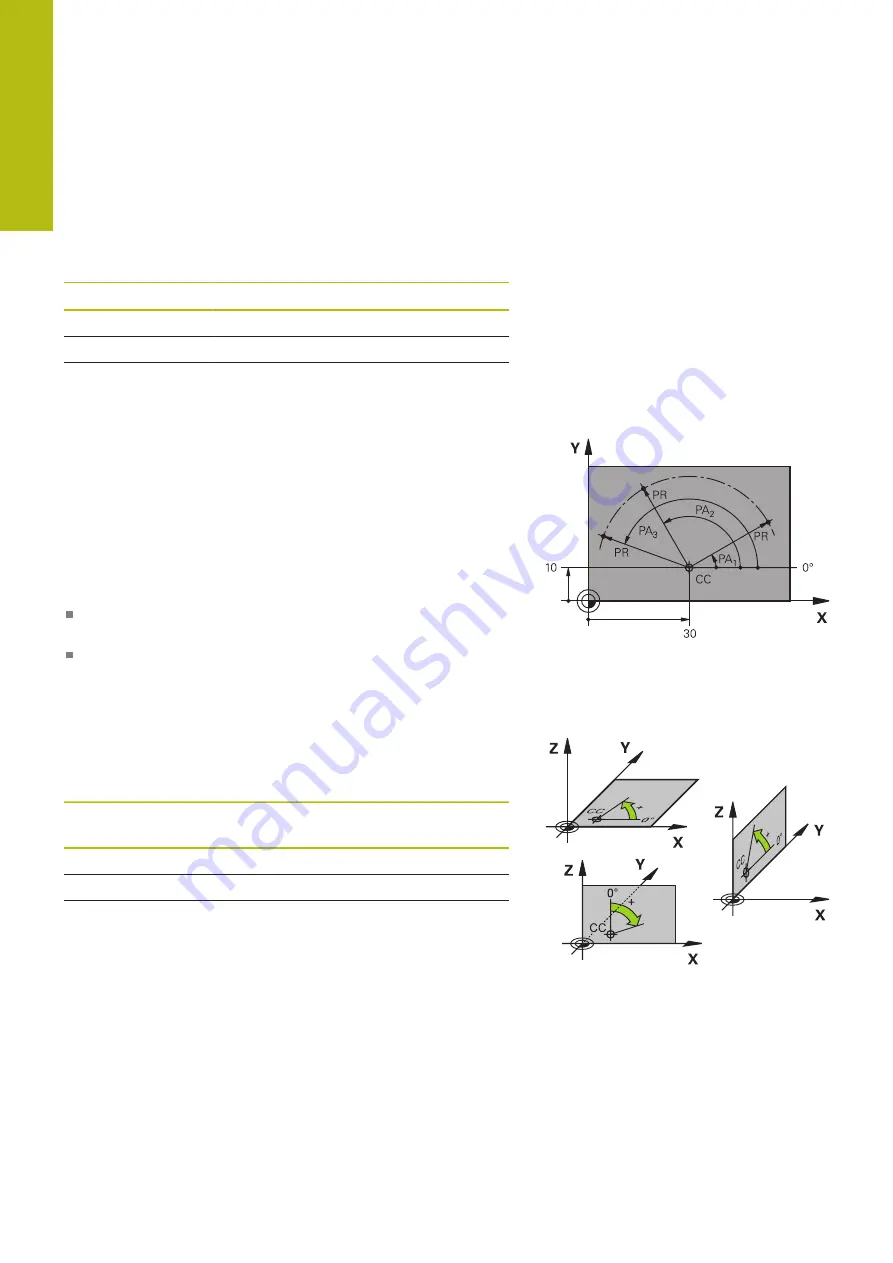
Fundamentals, File Management | Fundamentals
4
158
HEIDENHAIN | TNC 640 | Conversational Programming User's Manual | 10/2017
Designation of the axes on milling machines
The X, Y and Z axes on your milling machine are also referred to as
tool axis, principal axis (1st axis) and secondary axis (2nd axis). The
assignment of the tool axis is decisive for the assignment of the
principal and secondary axes.
Tool axis
Principal axis
Secondary axis
X
Y
Z
Y
Z
X
Z
X
Y
Polar coordinates
If the production drawing is dimensioned in Cartesian coordinates,
you also write the NC program using Cartesian coordinates. For
parts containing circular arcs or angles it is often simpler to give the
dimensions in polar coordinates.
While the Cartesian coordinates X, Y and Z are three-dimensional
and can describe points in space, polar coordinates are two-
dimensional and describe points in a plane. Polar coordinates have
their datum at a circle center (CC), or pole. A position in a plane can
be clearly defined by the:
Polar Radius, the distance from the circle center CC to the
position, and the
Polar Angle, the value of the angle between the angle reference
axis and the line that connects the circle center CC with the
position.
Setting the pole and the angle reference axis
The pole is set by entering two Cartesian coordinates in one of the
three planes. These coordinates also set the reference axis for the
polar angle PA.
Coordinates of the pole
(plane)
Reference axis of the angle
X/Y
+X
Y/Z
+Y
Z/X
+Z
Summary of Contents for TNC 640
Page 4: ......
Page 5: ...Fundamentals ...
Page 36: ...Contents 36 HEIDENHAIN TNC 640 Conversational Programming User s Manual 10 2017 ...
Page 67: ...1 First Steps with the TNC 640 ...
Page 90: ......
Page 91: ...2 Introduction ...
Page 130: ......
Page 131: ...3 Operating the Touchscreen ...
Page 144: ......
Page 145: ...4 Fundamentals File Management ...
Page 206: ......
Page 207: ...5 Programming Aids ...
Page 236: ......
Page 237: ...6 Tools ...
Page 281: ...7 Programming Contours ...
Page 333: ...8 Data Transfer from CAD Files ...
Page 355: ...9 Subprograms and Program Section Repeats ...
Page 374: ......
Page 375: ...10 Programming Q Parameters ...
Page 478: ......
Page 479: ...11 Miscellaneous Functions ...
Page 501: ...12 Special Functions ...
Page 584: ......
Page 585: ...13 Multiple Axis Machining ...
Page 650: ......
Page 651: ...14 Pallet Management ...
Page 664: ......
Page 665: ...15 Batch Process Manager ...
Page 673: ...16 Turning ...
Page 713: ...17 Manual Operation and Setup ...
Page 797: ...18 Positioning with Manual Data Input ...
Page 803: ...19 Test Run and Program Run ...
Page 843: ...20 MOD Functions ...
Page 881: ...21 Tables and Overviews ...