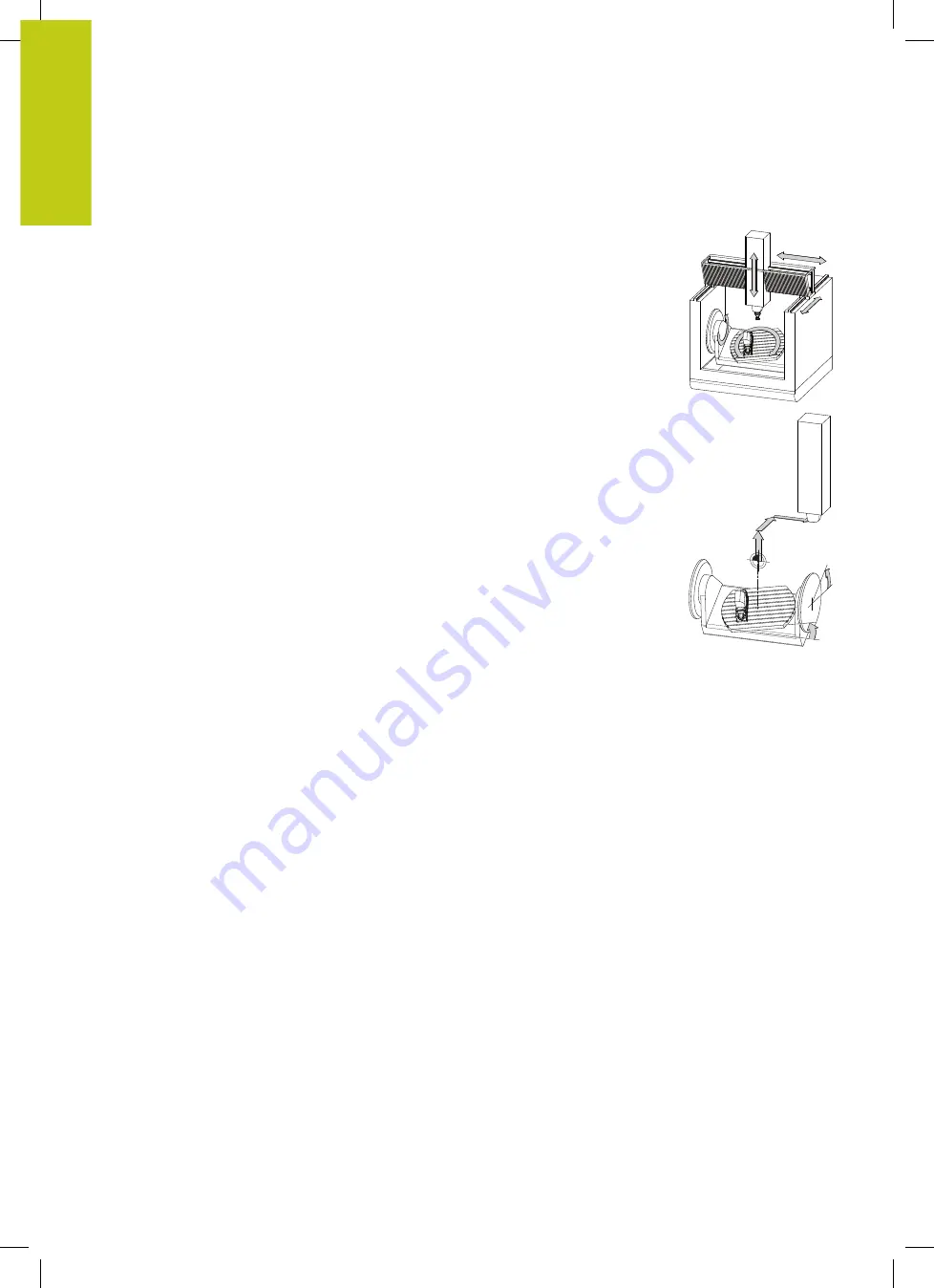
Fundamentals, file management
3.1
Fundamentals
3
114
HEIDENHAIN | TNC 620 | ISO Programming User's Manual | 9/2016
Machine coordinate system M-CS
The machine coordinate system corresponds to the description of
kinematics and therefore to the actual mechanical design of the
machine tool.
Because the mechanics of a machine tool never precisely
correspond to a Cartesian coordinate system, the machine
coordinate system consists of several one-dimensional coordinate
systems. These one-dimensional coordinate systems correspond to
the physical machine axes that are not obligatorily perpendicular to
each other.
The position and orientation of the one-dimensional coordinate
systems are defined with the aid of translations and rotations
based on the spindle tip in the description of kinematics.
The position of the coordinate origin, the so-called machine
datum, is defined by the machine manufacturer during machine
configuration. The values in the machine configuration define the
zero positions of the encoders and the corresponding machine
axes. The machine zero point is not obligatorily located in the
theoretical intersection of the physical axes. It can therefore also be
located outside of the traverse range.
Because the machine configuration values cannot be modified by
the user, the machine coordinate system is used for determining
constant positions, e.g. the tool change point.
MZP
Machine zero point MZP:
M
achine
Z
ero
P
oint
Summary of Contents for TNC 620 Programming Station
Page 4: ......
Page 5: ...Fundamentals ...
Page 28: ...Contents 28 HEIDENHAIN TNC 620 ISO Programming User s Manual 9 2016 ...
Page 57: ...1 First Steps with the TNC 620 ...
Page 77: ...2 Introduction ...
Page 110: ......
Page 111: ...3 Fundamentals file management ...
Page 166: ......
Page 167: ...4 Programming aids ...
Page 194: ......
Page 195: ...5 Tools ...
Page 234: ......
Page 235: ...6 Programming contours ...
Page 284: ......
Page 285: ...7 Data transfer from CAD files ...
Page 304: ......
Page 305: ...8 Subprograms and program section repeats ...
Page 323: ...9 Programming Q parameters ...
Page 384: ......
Page 385: ...10 Miscellaneous functions ...
Page 407: ...11 Special functions ...
Page 433: ...12 Multiple axis machining ...
Page 475: ...13 Pallet management ...
Page 480: ......
Page 481: ...14 Manual Operation and Setup ...
Page 549: ...15 Positioning with Manual Data Input ...
Page 554: ......
Page 555: ...16 Test Run and Program Run ...
Page 590: ......
Page 591: ...17 MOD Functions ...
Page 622: ......
Page 623: ...18 Tables and Overviews ...