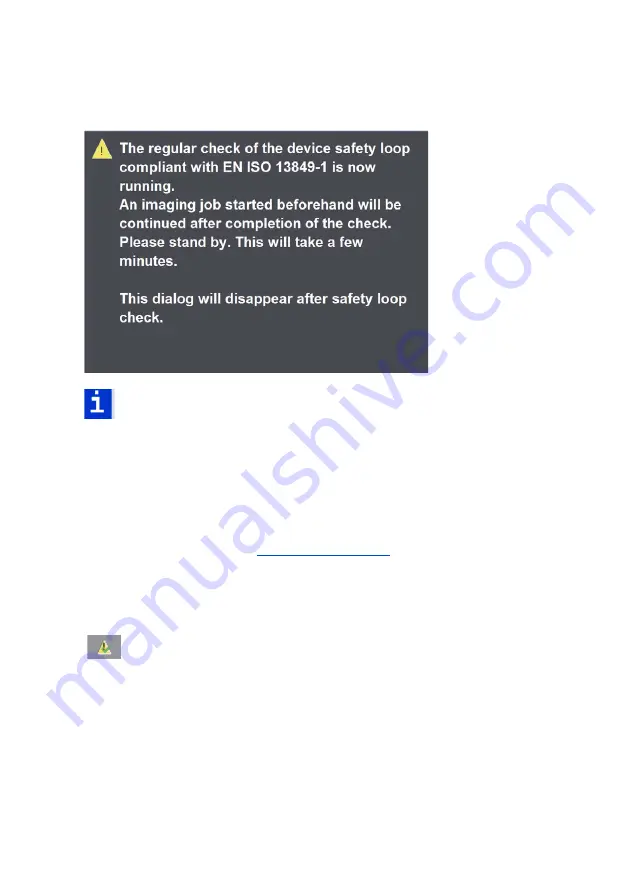
Before you start ...
Suprasetter 145/162/190 – User’s Guide
Note: During the check of the safety loop, it is not possible to image
plates.
The window closes automatically as soon as the check is finished (this can take
some minutes).
Manual check of the safety loop
The user can run an early check of the safety loop at any time before the 24-
hour time limit expires (see
) if, for example, a suitable
moment in production allows this.
Start check of safety loop
The check of the safety loop starts after you click this button in the
user interface and confirm again.
Summary of Contents for PG.010.000B
Page 1: ...Suprasetter 145 162 190 User s Guide 08 2019 Order No PG 999 0005...
Page 22: ......
Page 28: ......
Page 46: ...Operation 46 Version 2019 Fig 6 Removing a Printing Plate...
Page 51: ...Operation Suprasetter 145 162 190 User s Guide 51 Fig 15 Insert side panel Side panel...
Page 52: ......
Page 78: ...Disposal 78 Version 2019 Fig 3 Recorder disposal 1 PCBs in punches 2 Distributor PCB 2 1...
Page 80: ...Disposal 80 Version 2019 Fig 5 Recorder disposal 1 Light barrier pcb 1...
Page 82: ...Disposal 82 Version 2019 Fig 7 Disposal of the recorder 6 1 Pilot lamps 1...
Page 84: ...Disposal 84 Version 2019 Fig 9 Recorder disposal 1 2 Table top 2 1...
Page 92: ......
Page 103: ...Technical Data Suprasetter 145 162 190 User s Guide 103 Air Inlet Air Outlet AC outlet...
Page 105: ...Technical Data Suprasetter 145 162 190 User s Guide 105 Power switch with identification label...
Page 115: ......