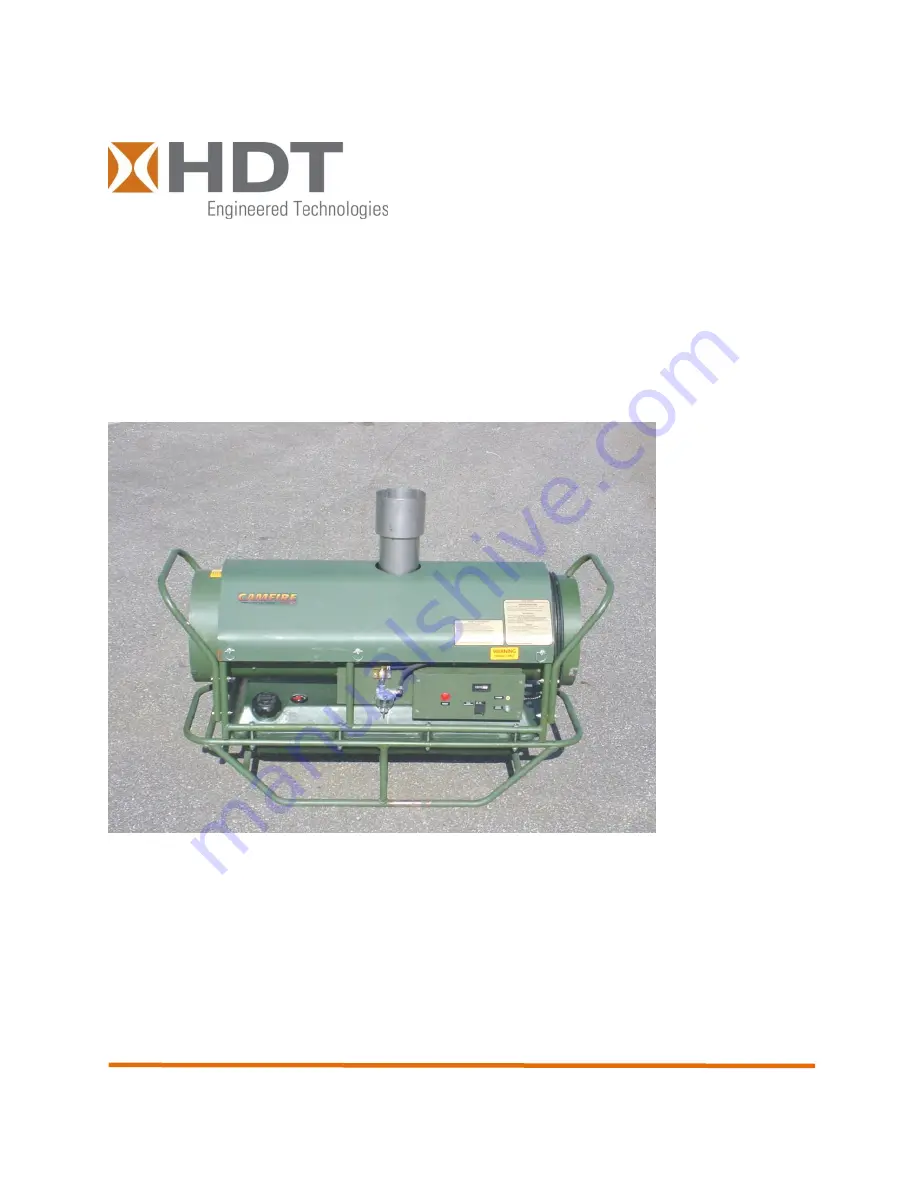
`
MV60-EU Series Heaters, 220 VAC, 50-60 Hz
SHELTER HEATER
60,000 BTU Multi-fuel Shelter Heater
Operation and Maintenance Manual
HDT
–Tactical Systems Business Unit
30525 Aurora Rd
Solon, Ohio 44139-2795
Tech Support: (800) 684-6111
www.hdtglobal.com
MANUAL PART NUMBER: 53858
REVISION 3
– 26APRIL2011
Summary of Contents for Camfire MV60S-EU
Page 2: ...THIS PAGE INTENTIONALLY LEFT BLANK ...
Page 22: ...Operation and Maintenance Manual 22 ...
Page 23: ...Operation and Maintenance Manual 23 Chapter 2 Setup and Operation of the CAMFIRE Heater ...
Page 24: ...Operation and Maintenance Manual 24 ...
Page 36: ...Operation and Maintenance Manual 36 ...
Page 37: ...Operation and Maintenance Manual 37 Chapter 3 Troubleshooting ...
Page 53: ...Operation and Maintenance Manual 53 Chapter 4 Maintenance ...
Page 86: ...86 ...
Page 87: ...87 Chapter 5 Illustrated Parts Listing ...
Page 90: ...90 Figure 5 2 MV60 EU FULL ASSEMBLY ...
Page 92: ...92 Figure 5 3 COMBUSTION CHAMBER ASSEMBLY 53504 18 ...
Page 94: ...94 Figure 5 4 BURNER HEAD ASSEMBLY 3 4 2 8 6 7 6 5 9 1 10 ...
Page 96: ...96 Figure 5 5 MV60 CONTROL BOX FUEL BRACKET ASSEMBLY ...
Page 98: ...98 Figure 5 6B CONTROL BOX ASSEMBLY ...
Page 100: ...100 Figure 5 7 MOTOR PUMP BRACKET ASSEMBLY 53745 ...
Page 102: ...102 Figure 5 8 MOTOR AND PUMP ASSEMBLY 53485 ...
Page 104: ...104 ...
Page 105: ...105 Chapter 6 Schematics and Wiring Diagrams ...