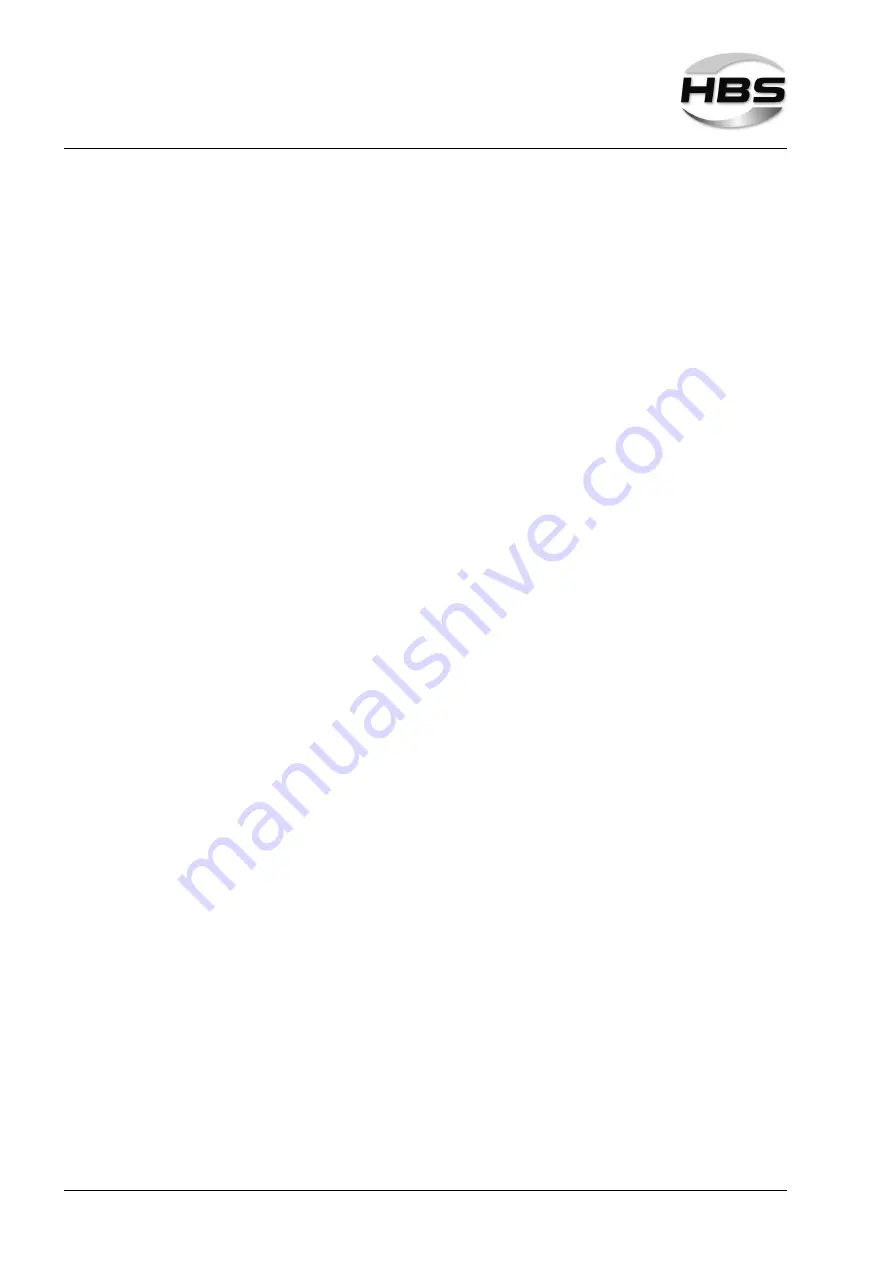
©HBS Bolzenschweiss-Systeme GmbH & Co. KG
All rights reserved – Reprinting, in whole or in part, only with the approval of the manufacturer
22
9 Welding Process
–
The weld pool solidifies and the welding element is physically connected to the
workpiece.
–
The time period between ignition of the arc and solidification of the weld pool is
about 3 ms.
– The use of contact welding for rapidly oxidizing materials like aluminium and alu-
minium alloys is not recommended because the arcing period with contact welding
is longer than with gap stud welding.
Summary of Contents for ACCU-TWIN 92-10-2280
Page 49: ......