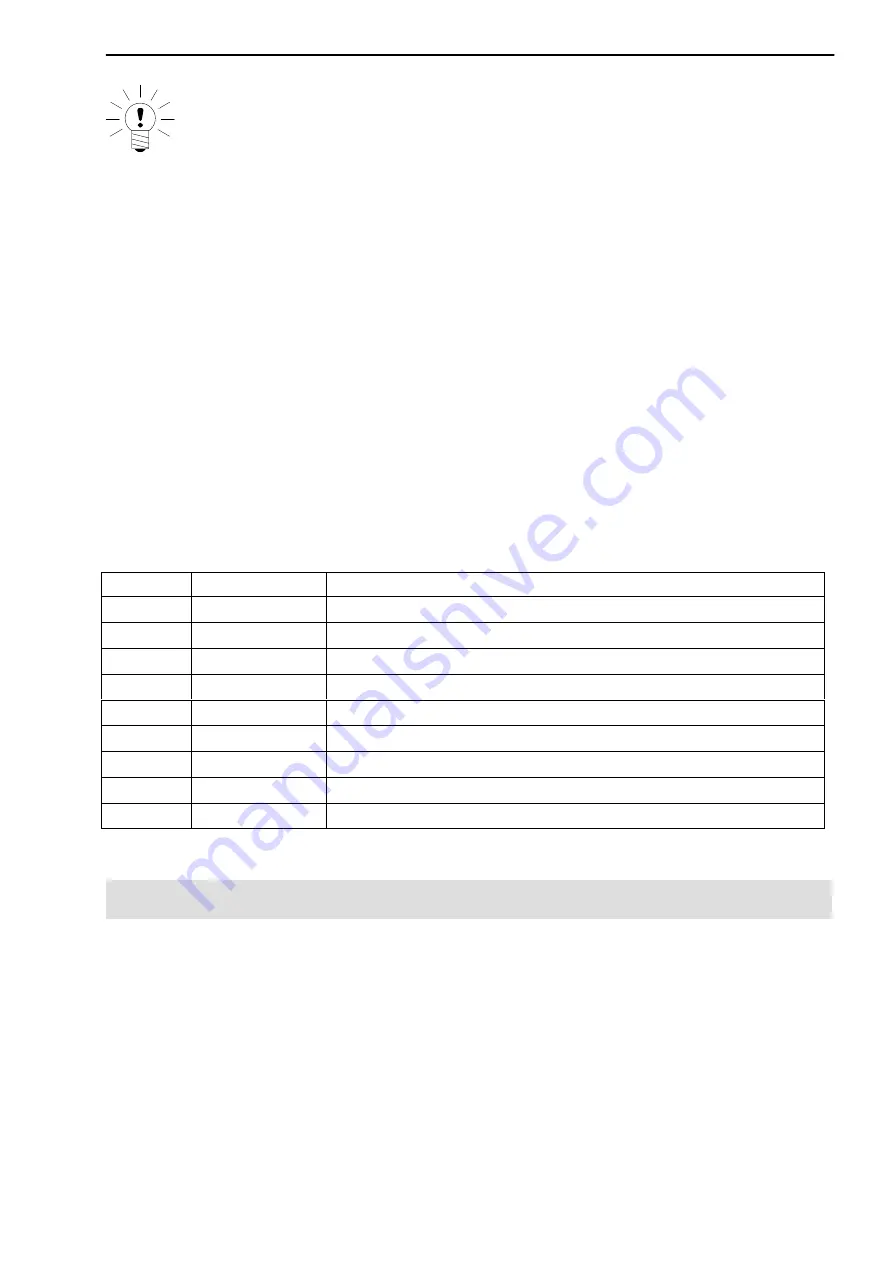
63
PME-MP70DP
A0658-7.3 en
HBM
NOTE
The status of the MP70DP can be queried via the MP70DP device status.
A CAN slave fault can also be detected and indicated after about 10
seconds (bit 14). This bit is also set when a number of errors are present
on the CAN Bus. This can include, for example, missing PDOs because
a CAN node has been lost. The exact time of the indication depends on
the number of nodes and the network load. This method of alarm
indication is therefore not suitable for high‐speed processes.
10.3.2 Outputs
Limit values
Limit value levels are realized in the same format as measured values (16‐bit
integer, 32‐bit integer or float format, see chapter 10.3.1). The switching
direction and hysteresis remain unchanged and can be set via the control
panel or the CAN Bus.
Control word
Bits
Name
Meaning
0
ZERO
Edge of 0 to 1 triggers zeroing
1
TAR
Edge of 0 to 1 triggers taring
2
res
reserved
3
res
reserved
4
CLRPEAK1
1 clears the MAX memory
5
CLRPEAK2
1 clears the MIN memory
6
HOLDPEAK1
1 freezes the MAX memory
7
HOLDPEAK2
1 freezes the MIN memory
8..15
res
reserved
10.4 PROFIBUS diagnosis
The external diagnosis made available by the MP70DP module is a device
diagnosis, that can be enabled using the parameterization diagram.
External diagnosis is 4 bytes long. The first byte contains the identifier for
device diagnosis, and in the second and third bytes, a bit is reserved for
errors that affect output, for the different causes of the error.