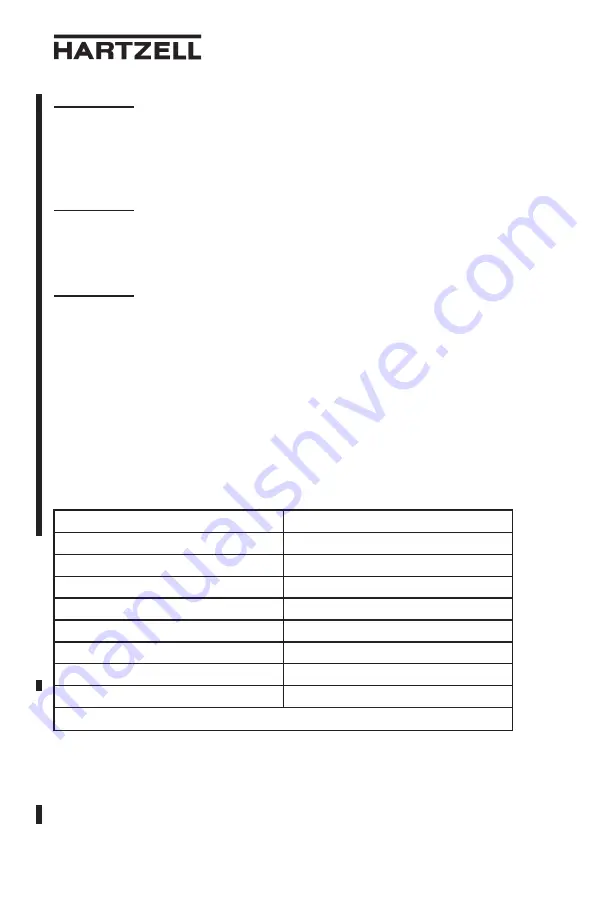
Propeller Owner’s Manual
139
INSTALLATION AND REMOVAL
61-00-39
Page 3-10
Rev. 17 Apr/20
Torque Table
Table 3-2
CAUTION 1: FOR A PROPELLER THAT DOES NOT USE A
LUBRICATED (WET) TORQUE, THE MOUNTING
HARDWARE MUST BE CLEAN AND DRY TO
PREVENT EXCESSIVE PRELOAD OF THE
MOUNTING FLANGE.
CAUTION 2:
TORQUE VALUES WITH “WET” NOTED AFTER
THEM ARE BASED ON LUBRICATED THREADS
WITH APPROVED ANTI-SEIZE COMPOUND
MIL-PRF-83483( ).
CAUTION 3
: REFER TO FIGURE 3-1 FOR TORQUE READING
WHEN USING A TORQUE WRENCH ADAPTER.
Hardware
Torque
A flange mounting bolts
100-105 Ft-Lbs (136-142 N•m) wet
F flange mounting bolts
80-90 Ft-Lbs (108-122 N•m)
N/P flange mounting bolts
100-105 Ft-Lbs (136-142 N•m) wet
W flange mounting nuts
120-125 Ft-Lbs (163-170 N•m)
Spinner mounting bolts
30-40 Ft-Lbs (41-54 N•m)
Piston nut (lock nut)
120 Ft-Lbs (163 N•m)*
Guide rod jam nuts
10 Ft-Lbs (14 N•m)*
Check Nut (beta valve assembly)
9-11 Ft-Lbs (12-15 N•m)
* Torque tolerance is ±10% unless otherwise noted.