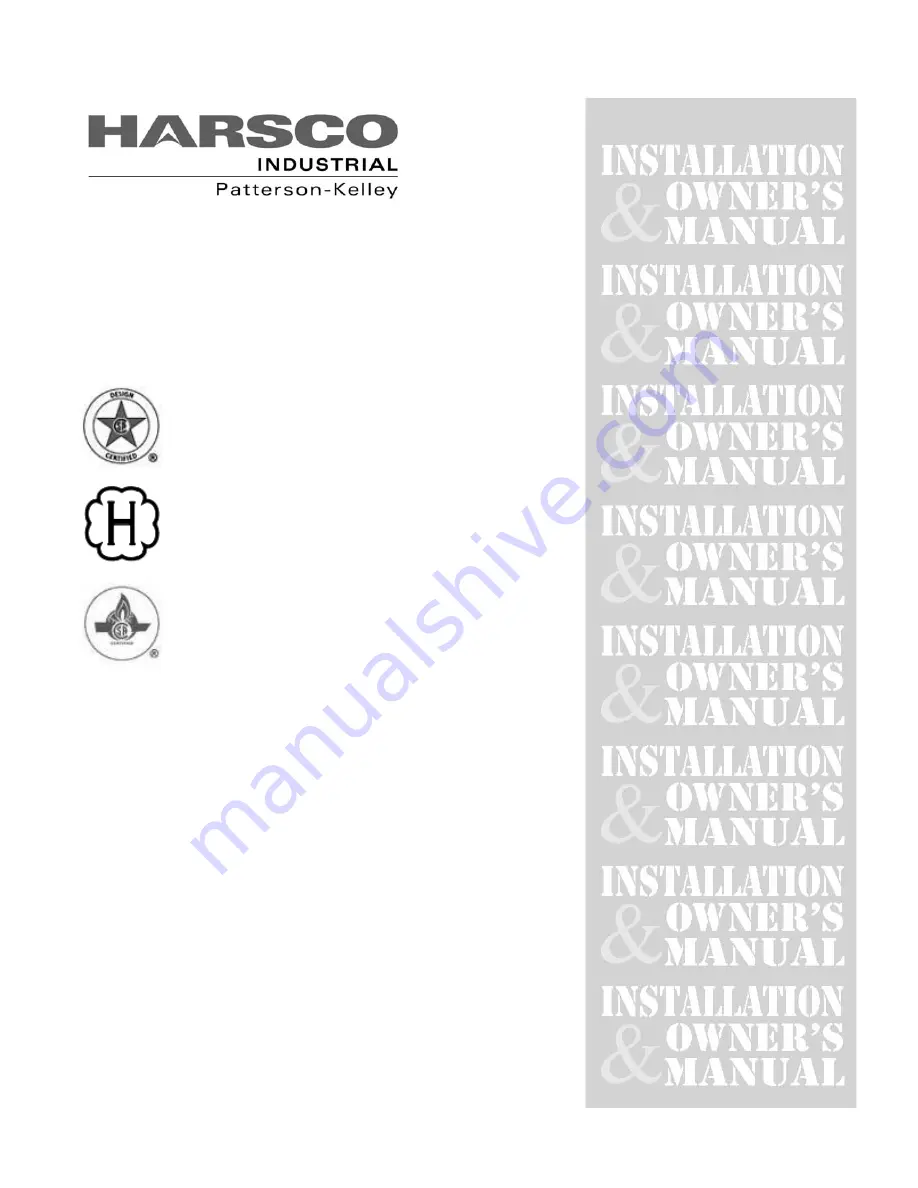
©2010 Harsco Industrial, Patterson-Kelley
Printed : 6/8/2012
MACH
®
GAS FIRED BOILER
C1500H/C2000H/C2500/C3000/C4000
Natural Gas/Propane/Dual Fuel
Model #:_______ Serial #______________________
Start-Up Date:
_______________________
Harsco Industrial, Patterson-Kelley
100 Burson Street
East Stroudsburg, PA 18301
Telephone: 570.476.7261
Toll Free: 877.728.5351
Facsimile: 570.476.7247
www.harscopk.com
MACH
®
C1500H – C4000
Rev. 1.03 (06/08/2012)
C.S.A Design-Certified
Complies with ANSI Z21.13/CSA 4.9
Gas-Fired Low Pressure Steam and Hot Water
Boilers
ASME Code, Section IV
Certified by Harsco Industrial, Patterson-Kelley
C.S.A Design-Certified
Complies with ANSI Z21.13/CSA 4.9
Gas-Fired Low Pressure Steam and Hot Water
Boilers
Summary of Contents for P-K MACH C1500H
Page 2: ...MACH Gas Fired Boiler 2...
Page 6: ...MACH Gas Fired Boiler 6...
Page 56: ...MACH Gas Fired Boiler 56 6 1 WIRING DIAGRAMS 6 1 1 MACH Boiler C1500H C2000H Wiring Diagram...
Page 58: ...MACH Gas Fired Boiler 58 6 1 3 MACH C3000 C4000 240VAC Boiler Wiring Diagram...
Page 59: ...MACH Gas Fired Boiler 59 6 1 4 MACH C3000 C4000 480VAC Wiring Diagram...
Page 60: ...MACH Gas Fired Boiler 60 6 1 5 MACH C1500H GG C2000H GG Dual Fuel Boiler Wiring Diagram...
Page 61: ...MACH Gas Fired Boiler 61 6 1 6 MACH C2500GG Dual Fuel Boiler Wiring Diagram...
Page 62: ...MACH Gas Fired Boiler 62 6 1 7 MACH C3000GG C4000GG 240VAC Dual Fuel Boiler Wiring Diagram...
Page 63: ...MACH Gas Fired Boiler 63 6 1 8 MACH C3000GG C4000GG 480VAC Dual Fuel Boiler Wiring Diagram...
Page 84: ...MACH Gas Fired Boiler 84...