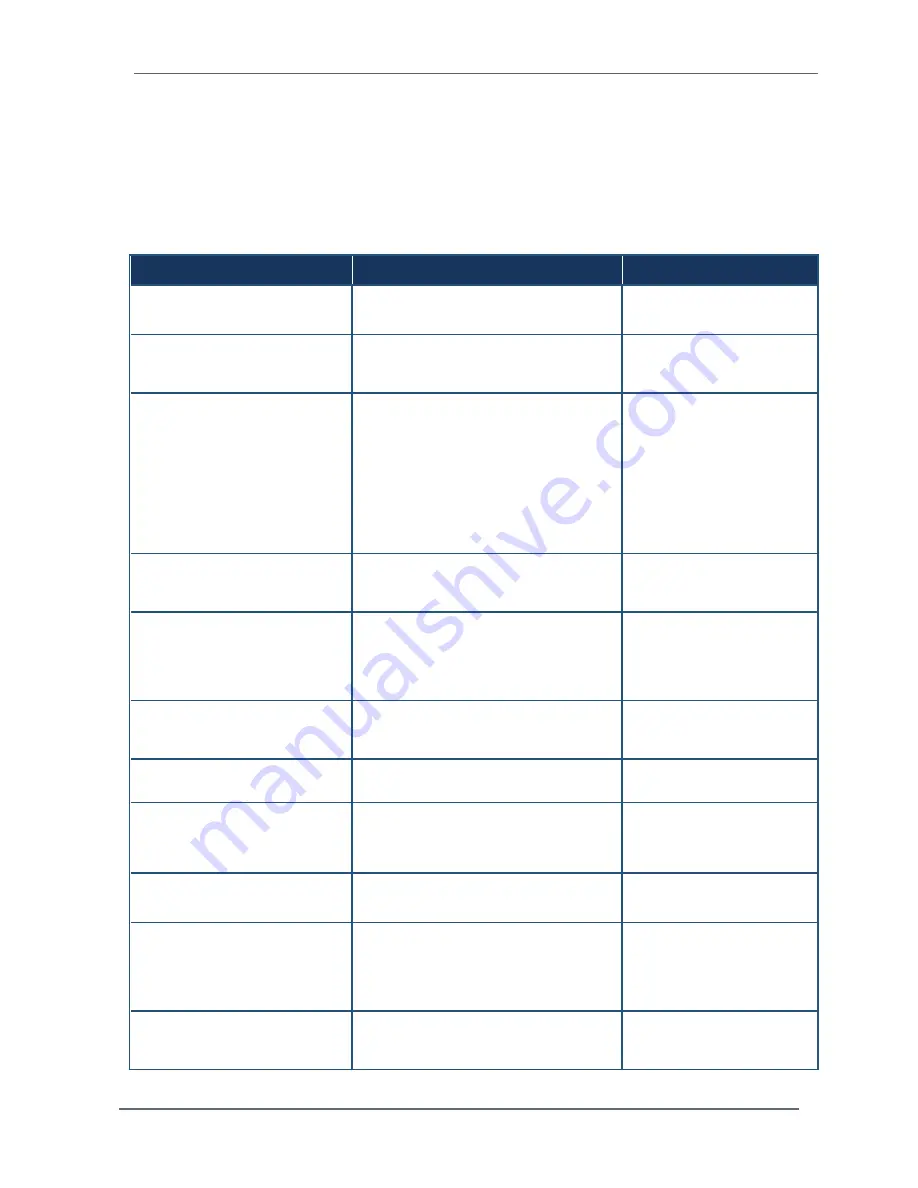
Chapter 6 – Troubleshooting
Hardy Process Solutions HI 6200 Weigh Processor User Guide
63
6.1 Troubleshooting Table
Table 6-1 lists possible problems that can occur with the HI 6200, their cause, and their
resolution.
Table 6-1. Troubleshooting Table
Name/Code #
Definition
Action
Command Success
command Status 0
Command passed
None
Command fail
Command Status 1
Command Failed. Applies to pass/fail
commands like C2 Search
Command specific.
Reevaluate the command
and conditions.
ADC Convert error
Command status error 2
Statusword bit 0
Load Cell input out of range (i.e., voltage
not 0-15 mV and flashing red LED will
display).
Can result from overloaded or
mismounted load cell. In this state weight
readings do not respond to changes.
May also be caused with a wiring issue
like broken/loose wire or mis-wired
(reversed)
Check the voltage levels to
the module from each load
cell. +5 V for excitation and
sense lines and 0-15 mV on
signal lines. If voltage is bad,
disconnect each one at the
summing box to find a
problem load cell.
Statusword, bit 1 AC Convert
Failure
Output from the A/D converter to
processor is bad. The module shows a
solid red LED.
Contact Tech Support or
request an RMA# to return
module for evaluation/repair
Statusword bit 2 Status Motion
Command status error 4
The rate of scale weight change over 1
second exceeds the motion tolerance
setting. If the setting is too low, motion
may be indicated when no changes occur.
If the weight is changing,
stabilize it. If not, increase the
motion tolerance setting until
the motion bit goes off with
static weight.
Statusword bit 3 EEPROM write
error
Module cannot write (save settings) to
non-volatile memory. EEPROM is
probably bad.
Contact Tech Support or
request an RMA# to return
module for evaluation/repair
Statusword bit 4 Status Center
Zero
Indicates the gross weight is reading at
the calibration zero point.
None
Statusword bit 6 In Progress
Command Status 0xFF
Command is in progress.
None
Statusword bit 7 not found
Command Status 0x80
The parameter ID is invalid
Correct the parameter ID
Command Status 5 No C2
When trying to perform a C2 calibration,
the module cannot read the data from the
load cells.
Check the wiring to ensure
proper connections and
orientation. Find the problem
load cell by disconnecting
them at the summing box.
Command Status 6 C2 Capacities
not equal
C2 load cells have unequal capacities due
to using mismatched load cells or faulty
C2 programming.
Verify each load cell is correct
per the spec sheet delivered
with the cell.