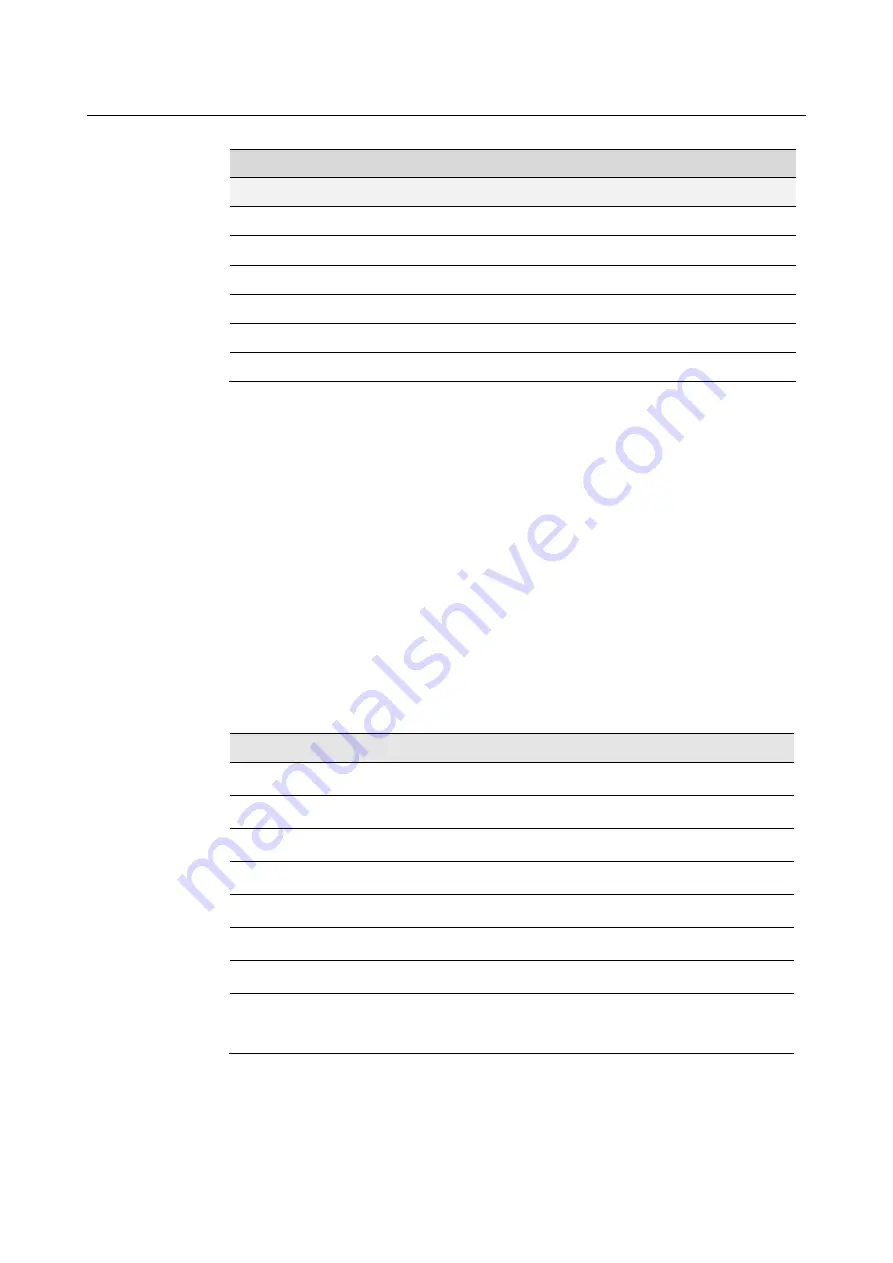
Chapter 3 Installation
48
Terminal
Parameter
Minimum
Format
Maximum
Unit
Digital input
EIx/SIx/FIx/DIx
Voltage
-
V
EIx/SIx/FIx/DIx
OFF area
-
V
EIx/SIx/FIx/DIx
ON area
-
V
EIx/SIx/FIx/DIx
Current (11-30V)
-
mV
EIx/SIx/FIx/DIx
Functions
-
PNP
-
Format
EIx/SIx/FIx/DIx
IEC 61131-2
-
3
-
Format
3.9
Configuring the Safety Input
Since a single signal loss should not lead to a loss of the safety function, all the I/O's
related to the safety should be duplexed.
Safety Input should always comply with the common specs of the digital I/O.
When you install the safety device or equipment, you should comply with the
instructions from Chapter 2 Safety and Chapter 3 Installation.
Safety inputs include emergency stop and safety protection stop. Emergency stop input
is for emergency stopping of the robot and safety protection stop input is for protection
of all the safety classes. Their functions are different from each other in this sense.
Emergency Stop
Safety protection stop
Robot stops the movement
Example
Example
Run the program
Stop
Pause
Robot power
Off
On
Initialization
Manual
Auto or manual
Frequency of use
Low
Mid
Re-initialization required
Break release only
No
Stop category (IEC 60204)
1
2
Performance level (ISO
13849-1)
PLd
PLd
Summary of Contents for HCR-5
Page 1: ...HCR 5 Collaborative Robot User Manual Aug 2019 V 2 001 ...
Page 2: ......
Page 14: ......
Page 96: ...Chapter 8 Safety Settings 96 ...
Page 101: ...Chapter 8 Safety Settings 101 3 Press the OK button ...
Page 188: ...Chapter 15 Maintenance 188 4 When the confirmation window appears press YES ...
Page 192: ...192 Appendix B Certification Safety ...
Page 193: ...193 ...
Page 194: ...194 MD Machinery Directive ...
Page 195: ...195 LVD Low Voltage Directive ...
Page 196: ...196 EMC Electro Magnetic Compatibility ...
Page 197: ...197 Cleanroom Body ...
Page 198: ...198 Cleanroom Controller ...
Page 199: ...199 Appendix C Dimensions for Installation ...
Page 205: ......