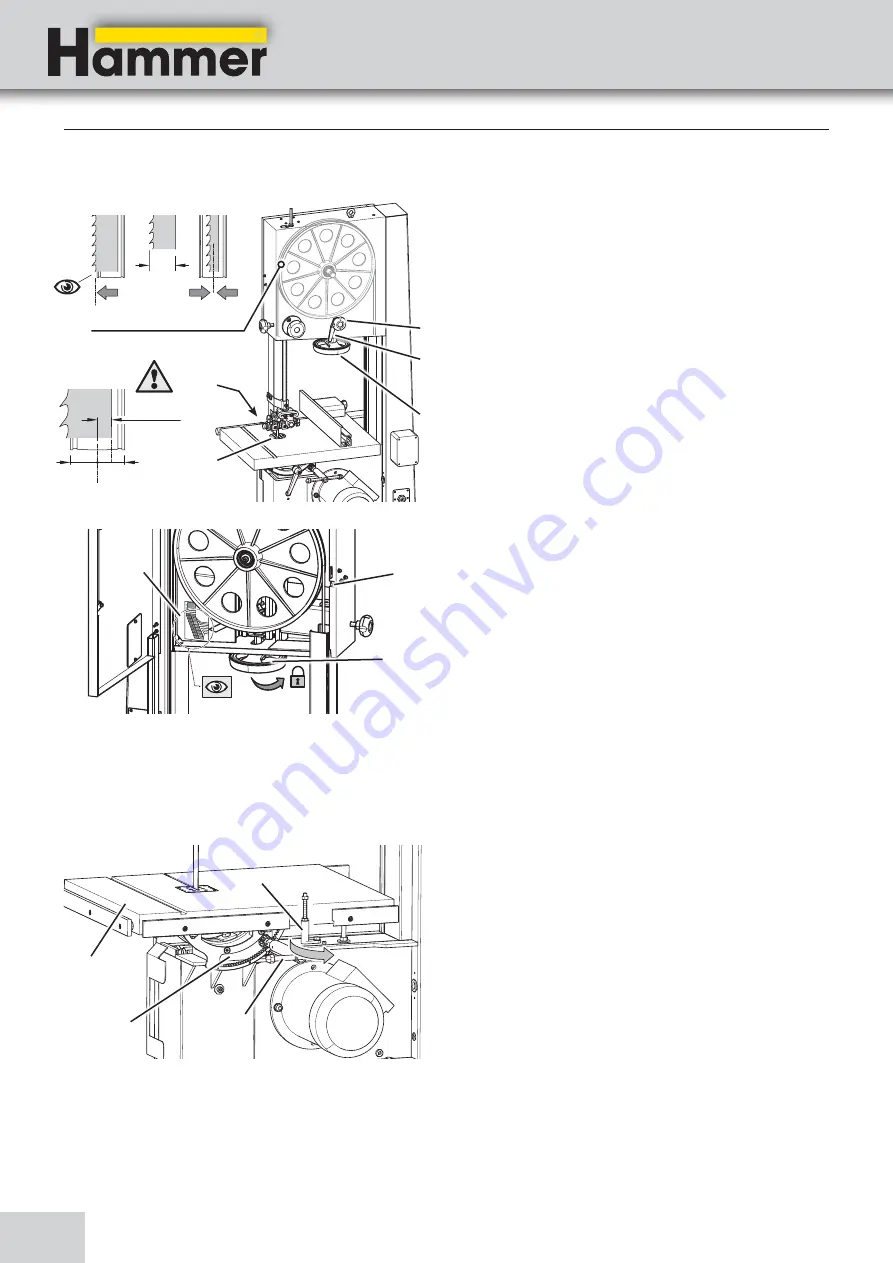
22
6 -16
mm
> 16
min 3 mm
1/2 1/2
&
%
/
%
#
$
!
"
!
"
#
$
Bandsaw
N3700 e-classic / N3800 / N4400
7.3 Saw blade replacement/tension
7.4 Tilting the table
Fig. 7-4: Tilt
The machine working table can be tilted up to an angle
from -5° (N4400: -10°) up to +45°.
Adjusting the angle:
To tilt, remove the table padding to enable the saw belt
to move through the table unimpeded. Open the clam-
ping screw with the supplied spanner and tilt the table to
the desired angle, which is displayed on the mitre scale.
Tighten the clamping screw again.
Tilt -5° or -10°:
• Swing away the stop
• Adjusting the angle
To tilt the table back to its normal position, loosen the
clamping screw once again and tilt the table up to the
stop in the 0° position and clamp it in that position.
(Swing back the stop)
!
Work bench
"
Clamping lever
#
Lever
$
Fence - 0°
Operation
1.
Disconnect the machine from the mains supply.
2.
Remove table insert and positioning pin.
Open wheel door.
3.
Loosen the blade tension hand wheel by turning it
clockwise. Unthread old blade through the machine
table.
4.
Place new saw blade over both wheels (note the di-
rection of the cut!).
Release the clamping lever and set the saw blade
track using the hand wheel:
see sketches
5.
Turn the wheels manually and ensure that the saw
belt glides properly around the wheels and does not
collide with any solid machine parts.
6.
Clamp the clamping lever.
Check the saw blade tension and if required, adjust
with the hand wheel. The values refer to the saw bla-
de width.
Fig. 7-3: Saw blade replacement
!
Positioning pin
"
Table insert
#
Handwheel - Saw blade track
$
Clamping lever
%
Blade tension hand wheel
&
Scale
/
Securing bolt (Optional equipment)