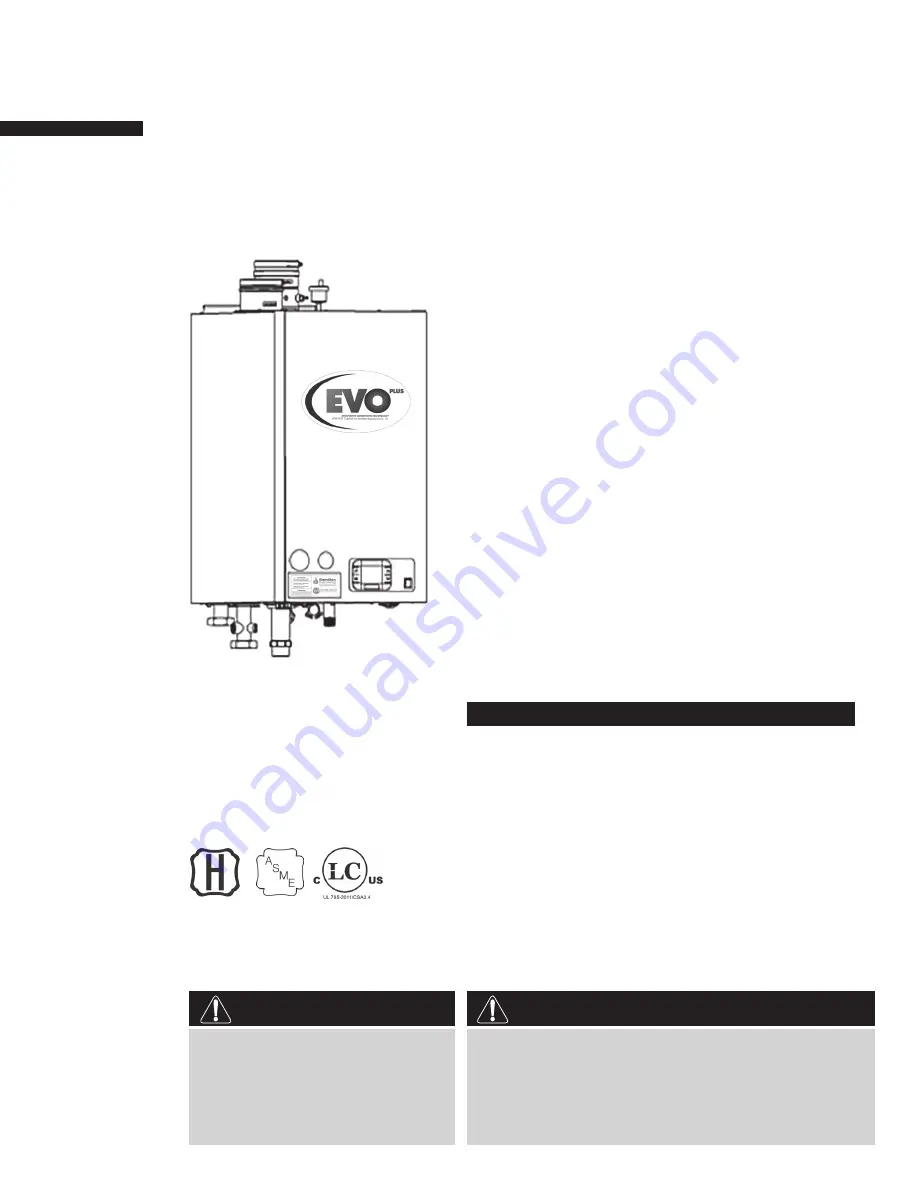
INSTALLING, OPERATING & MAINTAINING
EVO 299.2/.3–599.2/.3 High Efficiency
Water Heaters and Heating Boilers
EVO 299.2/.3–599.2/.3
300,000 BTU/hr
399,000 BTU/hr
630,000 BTU/hr
Do not store or use gasoline or other flammable vapors
and liquids in the vicinity of this or any other appliance
.
WHAT TO DO IF YOU SMELL GAS:
• Do not try to light any appliance
• Do not touch any electrical switch
• Do not use any phone in your building
Immediately call your gas supplier from a neighbor’s
phone. Follow the gas supplier instructions. If you cannot
reach your gas supplier, call the fire department.
If the information in this manual is not
followed exactly, a fire or explosion may
result causing property damage, personal
injury or death.
WARNING
New York
Massachusetts
SCAQMD
CEC Listed
MEA 425-05-E C1-0319-441 Compliant Rule1146.2 California Energy Commission
ANSI Z21.13-2014/CSA 4.9-2014
UL 795-2011/CSA 3.4
SCAQMD 1146.2
WARNING
These appliances MUST be installed by a properly licensed individual in
the City and State which the unit is being installed. All start up adjustments
and subsequent service work must be done by a similarly licensed
contractor or a factory trained service individual. Failure to comply could
result in loss of warranty and or severe personal injury, death and or
substantial property damage.
These instructions are required to be
kept with the appliance on the left side, in the pocket
provided.