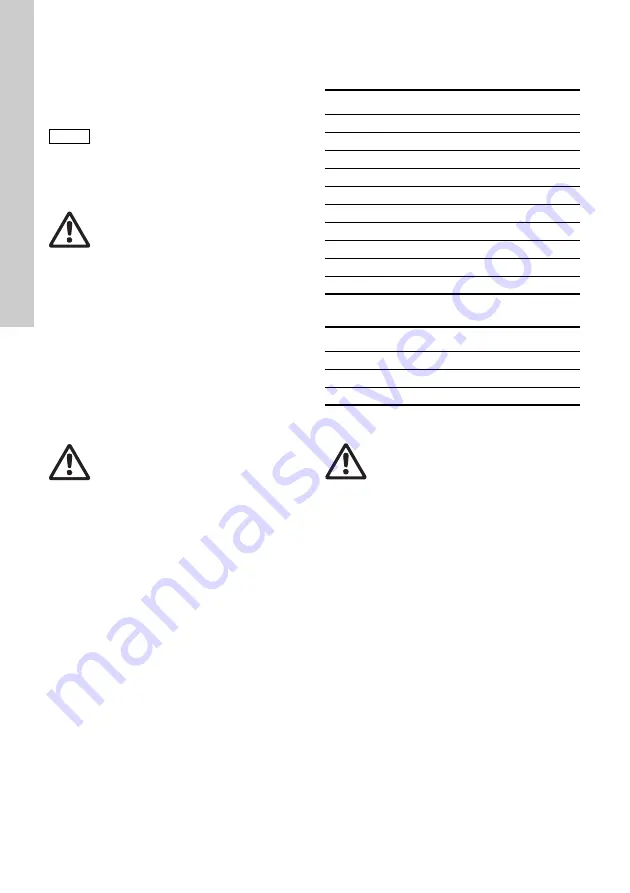
En
gl
is
h (
G
B)
10
5. Startup
Before starting the pump, submerge the pump inlet
in the pumped liquid.
Open the isolating valve, if fitted, and check the level
switch setting.
6. Maintenance and service
Before carrying out maintenance and service, it must
be ensured that the pump has been thoroughly
flushed with clean water. Rinse the pump parts in
water after dismantling.
Check the pump and replace the oil once a year. If
the pump is used for pumping liquids containing
abrasive particles or it is operating continuously, the
pump must be checked at shorter intervals.
6.1 Oil
The pump contains approx. 60 ml non-poisonous oil.
Used oil must be disposed of in accordance with
local regulations.
If the drained oil contains water or other impurities,
we recommend that you replace the shaft seal.
6.2 Construction
The construction of the pump will appear from the
table below and fig. D, page
.
6.3 Service kits
6.4 Contaminated pumps
If you request Grundfos to service the pump, contact
Grundfos with details about the pumped liquid, etc.
before you return the pump for service. Otherwise
Grundfos can refuse to accept the pump for service.
Possible costs of returning the pump are paid by the
customer.
However, any application for service (no matter to
whom it may be made) must include details about
the pumped liquid if the pump has been used for
liquids which are injurious to health or toxic.
Note
The pump may be run briefly to check the
direction of rotation without being
submerged in the pumped liquid.
Warning
Before starting any work on the product,
make sure that the power supply has been
switched off and that it cannot be
accidentally switched on.
Warning
Out of consideration for the personal
safety and health, this work must be
carried out by specially trained persons.
Furthermore, all rules and regulations
covering safety, health and environment
must be observed.
Be careful during dismantling as you will
get access to sharp edges, etc., which
may cause cuts. Wear protective gloves.
A possible replacement of the cable or the
level switch must be carried out by an
authorised Grundfos service workshop.
Pos.
Description
50
Pump housing
37a
O-ring
49
Impeller
150
Motor with flange
66
Washer
84
Base
67
Lock nut
6
Inlet part
105a
Shaft seal
182
Level switch
Service kit
Part number
Shaft seal, standard
96429307
Shaft seal, FKM
96429308
Oil
96010646
If a pump has been used for a liquid which
is injurious to health or toxic, the pump will
be classified as contaminated.
Summary of Contents for UNILIFT AP35B
Page 2: ...2...
Page 15: ...BG 15 3 3 1 1 2 3 1 2 3 4 5 1 3 10 ELCB 30 mA 3...
Page 17: ...BG 17 4 3 A B 196 197 1 2 3 4 3 4 5 6 7 8 9 10 4 4 C 198 90 4 5 5 30 5 TM03 4192 1806 270 mm...
Page 19: ...BG 19 7 1 a b c d e f 2 a b c d e f 3 1 3 a b c d 3 1 e f g...
Page 20: ...BG 20 8 1 2 Grundfos 4 a b c d e f...
Page 69: ...GR 69 3 3 1 1 2 3 1 2 3 4 5 1 3 10 ELCB 30 mA 3 mm...
Page 71: ...GR 71 4 3 A B 196 197 1 2 3 4 3 4 5 6 7 8 9 10 4 4 C 198 90 4 5 5 min 5 TM03 4192 1806 270 mm...
Page 73: ...GR 73 7 1 a b c d e f 2 a b c d e f 3 1 3 a b c d 3 1 e f g 4 a b c d e f...
Page 74: ...GR 74 8 1 2 Grundfos...
Page 168: ...UA 168 3 3 1 1 2 3 1 2 3 4 5 1 3 10 ELCB 30 A 3...
Page 170: ...UA 170 4 3 196 197 1 2 3 4 3 4 5 6 7 8 9 10 4 4 198 90 4 5 5 30 5 TM03 4192 1806 270 mm...
Page 172: ...UA 172 7 1 a b c d e f 2 a b c d e f 3 1 3 a b c d 3 1 e f g...
Page 173: ...UA 173 8 1 2 Grundfos 4 a b c d e f...
Page 176: ...CN 176 3 3 1 1 2 3 1 2 3 4 5 1 3 10 30 mA ELCB 3 mm PE...
Page 178: ...CN 178 4 3 A B 196 197 1 2 3 4 3 4 5 6 7 8 9 10 4 4 C 198 90 4 5 30 5 5 TM03 4192 1806 270 mm...
Page 180: ...CN 180 7 8 1 2 1 a b c d e f 2 a b c d e f 3 1 3 a b c d 3 1 e f g 4 a b c d e f...
Page 191: ...Arabic AR 191 198 90 4 4 4 4 5 30 4 5 4 5 TM03 4192 1806 5 5 5 5 270 mm...
Page 193: ...Arabic AR 193 3 3 10 30 3 PE 3 1 3 1 1 1 2 2 3 3 1 1 2 2 3 3 4 4 1 3 5 5...
Page 199: ...Appendix 199 Fig D TM03 4209 1806...
Page 200: ...200...
Page 201: ...201...