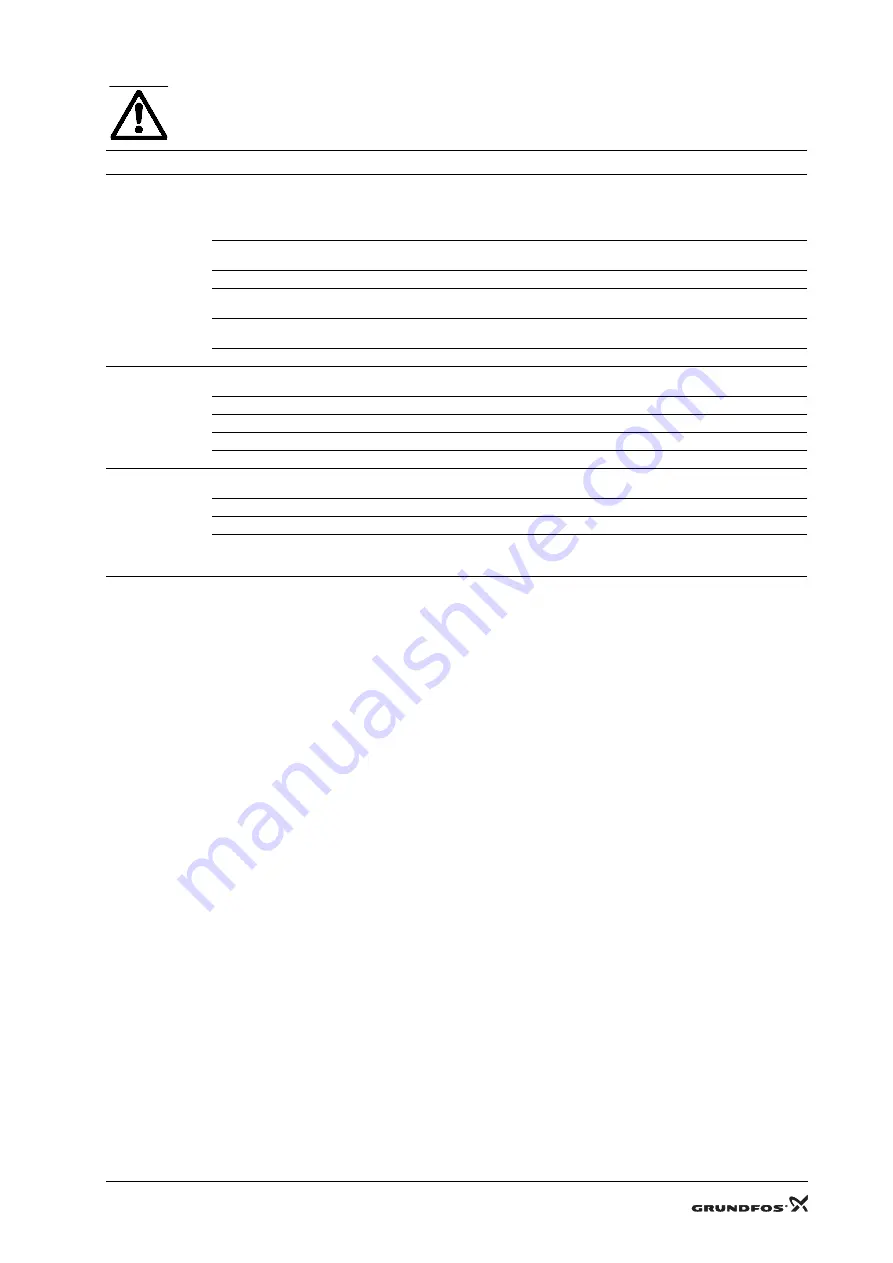
4.5 Fault finding
Before starting work on the pump, make sure that the electricity supply has been switched off and that it cannot be
accidentally switched on.
Fault
Possible cause
Remedy
The pump stops
during operation.
No water supply.
Low-pressure switch has cut out.
The level switch has cut out.
Check that the low-pressure switch functions normally and is
adjusted correctly.
Check that the minimum inlet pressure is correct. If not, check the
feed pump.
Check the water level in the water tank.
The fuses are blown.
Check and replace the main fuses and/or fuses for control circuit,
if necessary.
The motor starter overload unit has tripped out.
Reset the starter overload.
The magnetic coil in the motor starter/contactor is
defective (not cutting in).
Replace the coil. Check the coil voltage.
The control circuit has cut out or is defective.
Check the control circuit and the contacts in the monitoring
devices (low-pressure switch, level switch, etc.).
The motor/supply cable is defective.
Check motor and cable
The pump runs, but
gives no water or
develops any
pressure.
No or insufficient water supply at the pump suction
port.
Check that the inlet pressure is at least 0 bar.
The piping system or pump is choked up.
Check the piping system and pump.
The prefilter is clogged.
Clean the prefilter.
The pump is worn.
Replace wear parts. Contact Grundfos Service.
Wrong direction of rotation.
Interchange two phases in the motor main connection.
The pump runs at
reduced capacity.
The pump is partly blocked by impurities.
Dismantle, clean and check the pump.
Replace defective parts. Contact Grundfos Service.
The pump is defective.
Replace defective parts. Contact Grundfos Service.
The prefilter is clogged.
Clean the prefilter.
The motor speed is too low.
Check the electricity supply.
Contact the electricity supply authorities, if necessary.
If a frequency converter is used, adjust the speed.