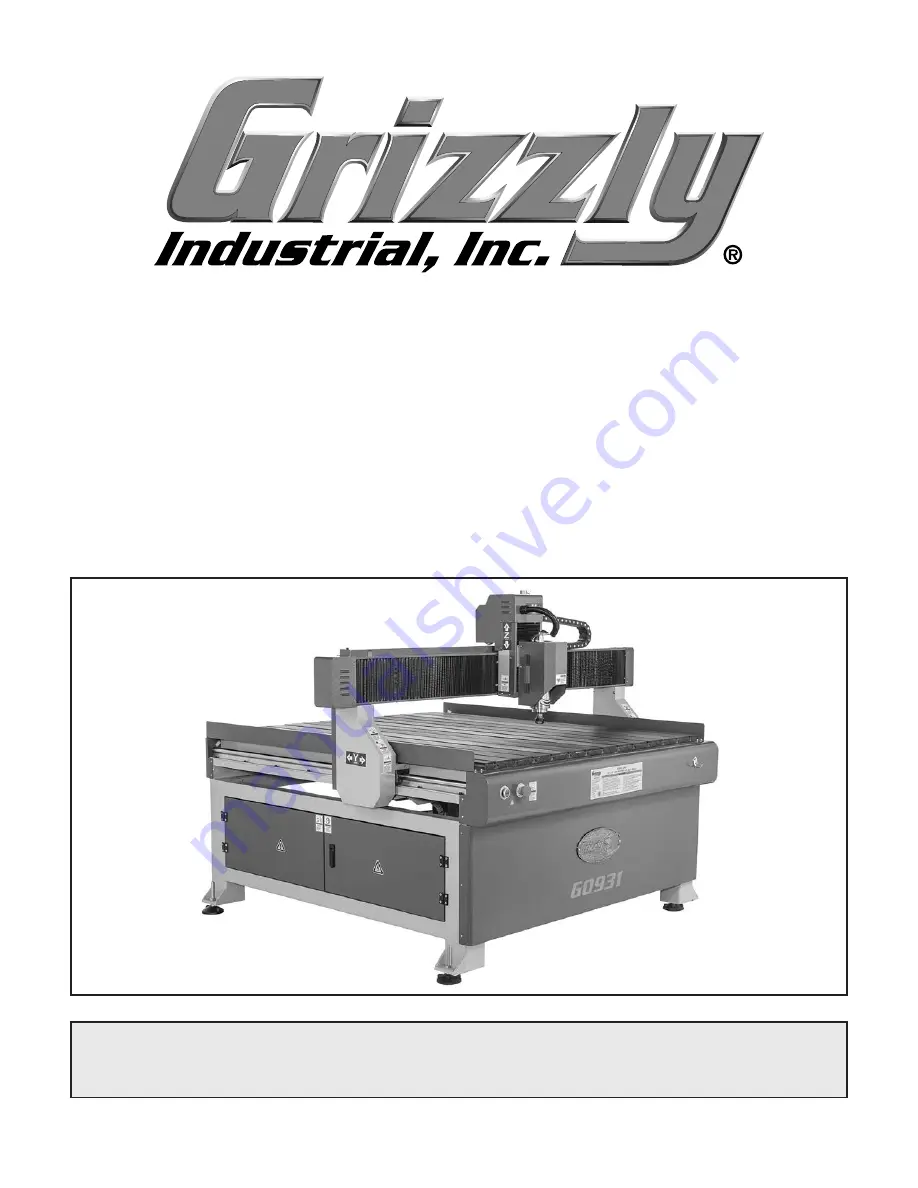
MODEL G0931
47" X 47" CNC ROUTER
w/T-SLOT TABLE
OWNER'S MANUAL
(For models manufactured since 02/21)
COPYRIGHT © APRIL, 2022 BY GRIZZLY INDUSTRIAL, INC.
WARNING: NO PORTION OF THIS MANUAL MAY BE REPRODUCED IN ANY SHAPE
OR FORM WITHOUT THE WRITTEN APPROVAL OF GRIZZLY INDUSTRIAL, INC.
#KS22105 PRINTED IN CHINA
V1.04.22
***Keep for Future Reference***