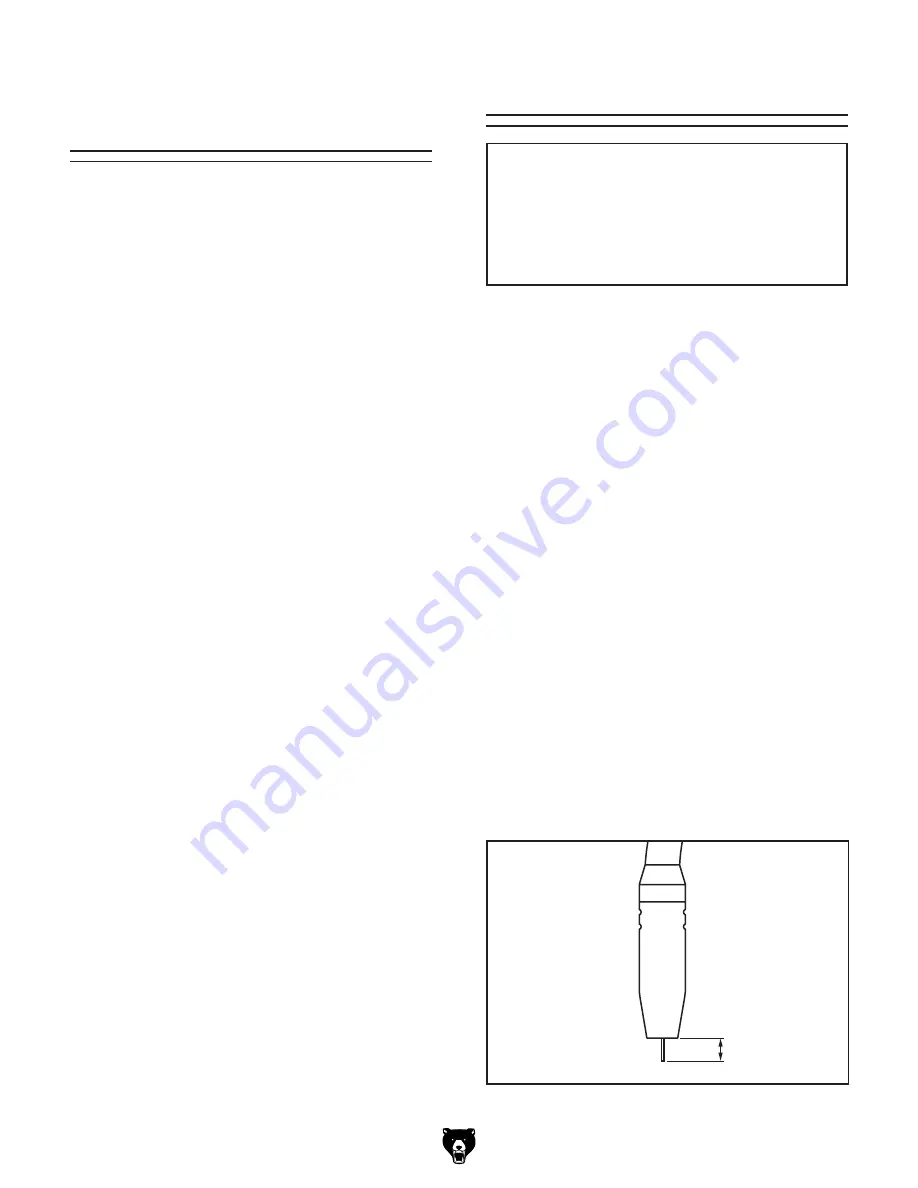
Model G0879 (Mfd. Since 6/19)
-23-
Basic Operation
NOTICE
It is beyond the scope of this manual to
instruct how to properly weld. No manual is
a replacement for formal training or instruc-
tion. It is highly recommended that the user
seek formal training with extensive practice.
Figure 20. Welding wire stick-out.
1
⁄
4
"
Workpiece
Inspection
Some workpieces are not safe to weld or may
require modification before they are safe to weld.
Before welding, inspect all workpieces for the
following:
•
Material Type: This machine is intended for
mild steel welding using flux cored wire. Be
aware of the side affects of welding different
kinds of metals. Take proper precautions and
think about the workpiece you are welding
on. Know what type of material you are work-
ing with; welding certain treated metals, such
as galvanized steel, can create severely toxic
fumes.
•
Foreign Objects: Paint, grease, chemicals,
rust, and other unwanted substances can
affect the quality and safety of welds. Ensure
work area is free of flammable materials
Make sure the workpiece is clean before
welding, for both the location of the weld and
the ground clamp.
•
Sealed containers: DO NOT weld, burn
or heat sealed or pressurized containers.
Observe specific guidelines when welding a
workpiece to ensure safe practice has not
been overlooked.
Becoming familiar with welding techniques and
settings requires practice and experience. Take
time to practice and understand the basic vari-
ables of welding techniques and settings.
To perform a basic weld:
1. Follow all safety guidelines to ensure envi-
ronment and workpiece are safe for welding
practice (see
Workpiece Inspection, and
Safety on Page 8).
2. Wear all recommended and approved welding
safety gear, including welding hood, gloves,
long sleeves, and boots (see
Additional
Safety for Welders on Page 10).
3. Connect ground clamp to workpiece, near
intended location of weld.
4. Plug in welder and turn machine ON.
5. Point gun away from yourself and any con-
ductive material. Squeeze trigger to release
welding wire. Cut back wire to about
1
⁄
4
" stick-
out from contact tip (see
Figure 20).
Summary of Contents for G0879
Page 36: ......