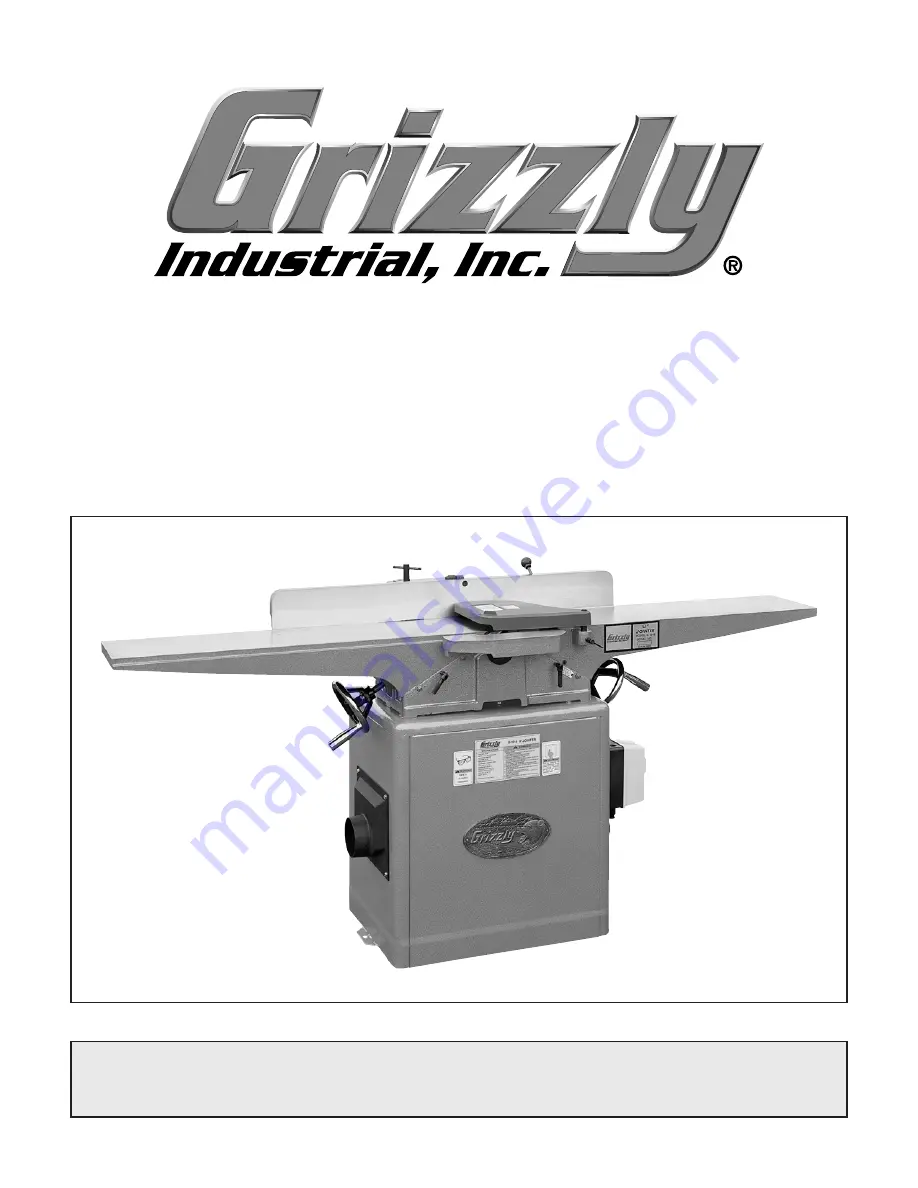
Model G0500 Shown
MODEL G0500/G1018/G1018HW
8" JOINTER
OWNER'S MaNuaL
Copyright © JANUAry, 2003 By grizzly iNdUstriAl, iNC., revised JUly, 2012 (tr)
WaRNING: NO pORTION Of THIS MaNuaL May bE REpRODucED IN aNy SHapE
OR fORM WITHOuT THE WRITTEN appROvaL Of GRIzzLy INDuSTRIaL, INc.
#tr4986 priNted iN tAiWAN